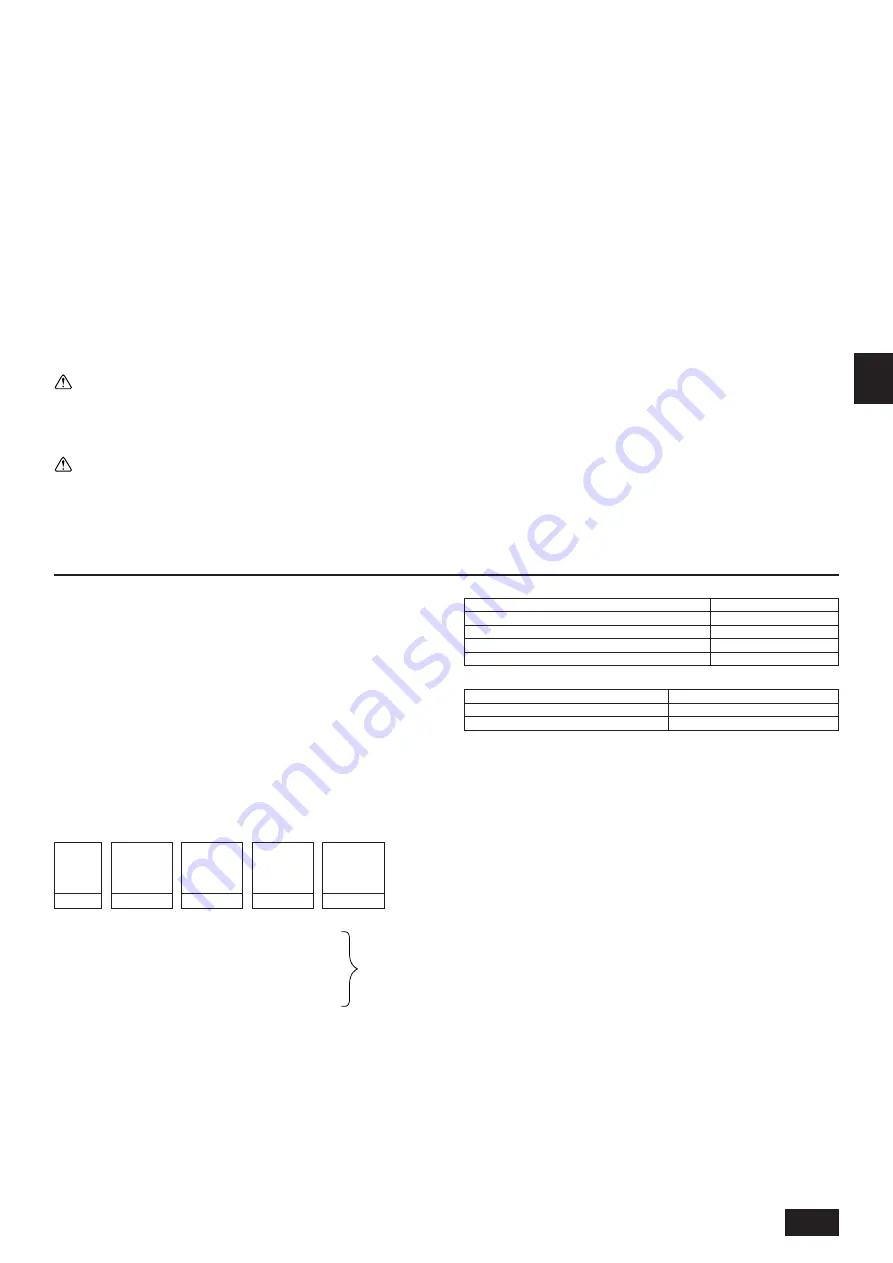
9
GB
D
F
I
NL
E
P
GR
RU
TR
8. Additional Refrigerant Charge
At the time of shipping, the outdoor unit is charged with the refrigerant. As this
charge does not include the amount needed for extended piping, additional charg-
ing for each refrigerant line will be required on site. In order that future servicing
may be properly provided, always keep a record of the size and length of each
refrigerant line and the amount of additional charge by writing it in the space pro-
vided on the outdoor unit.
8.1. Calculation of Additional Refrigerant
Charge
•
Calculate the amount of additional charge based on the length of the piping
extension and the size of the refrigerant line.
•
Use the table to the right as guide to calculating the amount of additional charg-
ing and charge the system accordingly.
•
If the calculation results of the calculation result in a fraction of less than 0.1 kg.
For example, if the result of the calculation was 22.52 kg, round the result up to
22.6 kg.
<Additional Charge>
=
+
+
+
+
α
1
+
α
2
<Example>
Indoor No.1: 40
A: ø25.4
40 m
a: ø6.35
10 m
No.2: 100
B: ø9.52
10 m
b: ø9.52
5 m
No.3: 40
C: ø12.7
10 m
c: ø6.35
10 m
No.4: 32
d: ø6.35
10 m
No.5: 63
e: ø9.52
10 m
No.6: 200
f: ø12.7
10 m
The total length of each liquid line is as follows:
ø19.05: A = 40 m
ø12.7: C + f = 10 +10 = 20 m
ø9.52: B + b + e = 10 + 5 + 10 = 25
ø6.35: a + c + d = 10 + 10 + 10 = 30 m
Therefore,
<Calculation example>
Additional refrigerant charge
= 40
×
0.31 + 20
×
0.12 + 25
×
0.06 + 30
×
0.024 + 2.5 + 3.0 = 22.6 kg
6
The City Multi Series R2 will stop due to an abnormality due to excessive or
insufficient coolant. At such a time, always properly charge the unit. When
servicing, always check the notes concerning pipe length and amount of addi-
tional refrigerant at both locations, the refrigerant volume calculation table on
the back of the service panel and the additional refrigerant section on the la-
bels for the combined number of indoor units.
7
Use liquid refrigerant to fill the system.
8
Never use refrigerant to perform an air purge. Always evacuate using a vacuum
pump.
9
Always insulate the piping properly. Insufficient insulation will result in a de-
cline in heating/cooling performance, water drops from condensation and other
such problems.
0
When connecting the refrigerant piping, make sure the ball valve of the out-
door unit is completely closed (the factory setting) and do not operate it until
the refrigerant piping for the outdoor and indoor units has been connected, a
refrigerant leakage test has been performed and the evacuation process has
been completed.
A
Always use a non-oxidizing brazing material for brazing the parts. If a non-
oxidizing brazing material is not used, it could cause clogging or damage to
the compressor unit.
B
Never perform outdoor unit piping connection work when it is raining.
Warning:
When installing and moving the unit, do not charge it with refrigerant other
than the refrigerant specified on the unit.
- Mixing of a different refrigerant, air, etc. may cause the refrigerant cycle to mal-
function and result in severe damage.
Caution:
•
Use a vacuum pump with a reverse flow check valve. (For R407C models)
- If the vacuum pump does not have a reverse flow check valve, the vacuum
pump oil may flow back into the refrigerant cycle and cause deterioration of
the refrigerator oil and other trouble.
•
Do not use the tools shown below used with conventional refrigerant.
(For R407C models)
(Gauge manifold, charge hose, gas leak detector, check valve, refriger-
ant charge base, vacuum gauge, refrigerant recovery equipment)
- Mixing of conventional refrigerant and refrigerator oil may cause the refrig-
erator oil to deteriorate.
- Mixing of water will cause the refrigerator oil to deteriorate.
- R407C refrigerant does not contain any chlorine. Therefore, gas leak detec-
tors for conventional refrigerants will not react to it.
•
Manage the tools more carefully than normal. (For R407C models)
- If dust, dirt, or water gets in the refrigerant cycle, the refrigerator oil will
deteriorate.
•
Never use existing refrigerant piping. (For R407C models)
- The large amount of chlorine in conventional refrigerant and refrigerator oil
in the existing piping will cause the new refrigerant to deteriorate.
•
Store the piping to be used during installation indoors and keep both
ends of the piping sealed until just before brazing.
- If dust, dirt, or water gets into the refrigerant cycle, the oil will deteriorate and
the compressor may fail.
•
Do not use a charging cylinder. (For R407C models)
- Using a charging cylinder may cause the refrigerant to deteriorate.
•
Do not use special detergents for washing piping.
7.2. Refrigerant piping system
Connection Example
[Fig. 7.2.1]
(P.3)
Å
High press pipe
ı
Low press pipe
Ç
Connection of outdoor unit/BC controller
Î
Total capacity of indoor units
‰
Liquid line
Ï
Gas line
Ì
Model number
A
BC controller (master)
A
' BC controller (slave)
B
Indoor unit (20~140)
C
Indoor unit (200, 250)
Value of
α
1
Total capacity of connecting indoor units
α
1
to Model 330
2.0 kg
Models 331 to 480
2.5 kg
Models 481 to 630
3.0 kg
Models 631 or more
4.0 kg
Value of
α
2
α
2
BC controller (master) only
0 kg
BC controller (slave) connected
3.0 kg
8.2. Caution for piping connection/valve
operation
•
Conduct piping connection and valve operation accurately.
•
The gas side connecting pipe is assembled in factory before shipment.
1
For brazing to the connecting pipe with flange, remove the connecting pipe
with flange from the ball valve, and braze it outside of the unit.
2
During the time when removing the connecting pipe with flange, remove
the seal attached on the back side of this sheet and paste it onto the flange
surface of the ball valve to prevent the entry of dust into the valve.
3
The refrigerant circuit is closed with a round, close-packed packing upon
shipment to prevent gas leak between flanges. As no operation can be
done under this state, be sure to replace the packing with the hollow pack-
ing attached at the piping connection.
4
At the mounting of the hollow packing, wipe off dust attached on the flange
sheet surface and the packing. Coat refrigerating machine oil (Ester oil,
ether oil or alkylbenzene [small amount]) onto both surfaces of the pack-
ing.
[Fig. 8.2.1] (P.3)
•
After evacuation and refrigerant charge, ensure that the handle is fully open. If
operating with the valve closed, abnormal pressure will be imparted to the
high- or low-pressure side of the refrigerant circuit, giving damage to the com-
pressor, four-way valve, etc.
•
Determine the amount of additional refrigerant charge by using the formula,
and charge refrigerant additionally through the service port after completing
piping connection work.
•
After completing work, tighten the service port and cap securely not to gener-
ate gas leak.
At the
conditions
below:
High press
pipe size
Total length of
ø25.4
×
0.31
(m)
×
0.31 (kg/m)
Liquid pipe
size
Total length of
ø12.7
×
0.12
(m)
×
0.12 (kg/m)
Liquid pipe
size
Total length of
ø9.52
×
0.06
(m)
×
0.06 (kg/m)
Liquid pipe
size
Total length of
ø6.35
×
0.024
(m)
×
0.024 (kg/m)
Additional
refrigerant
charge
(kg)