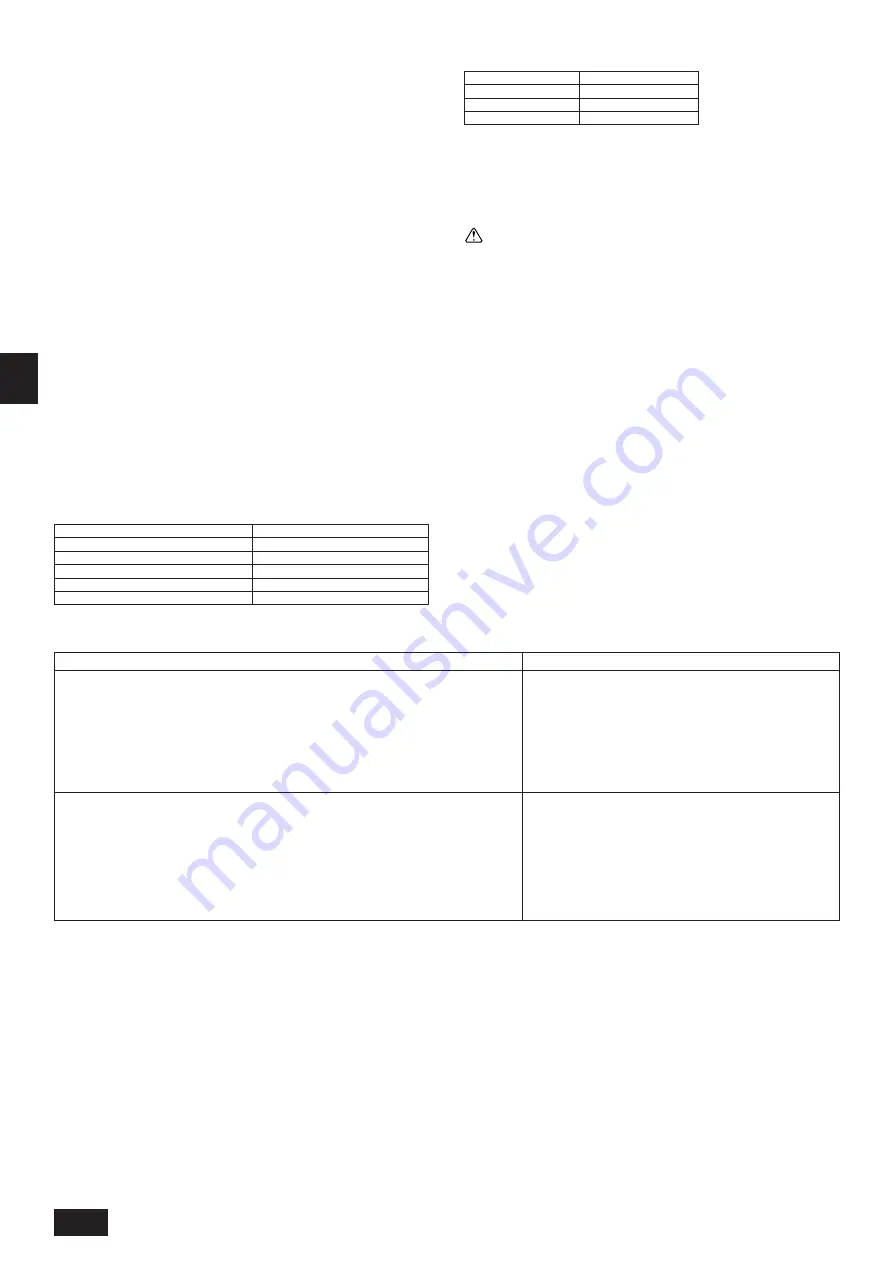
10
GB
D
F
I
NL
E
P
GR
RU
TR
Restriction
• If a flammable gas or air (oxygen) is used as the pressurization
gas, it may catch fire or explode.
• Do not use a refrigerant other than that indicated on the unit.
• Sealing with gas from a cylinder will cause the composition of
the refrigerant in the cylinder to change. (For R407C models)
• Use a pressure gauge, charge box, and other parts especially for
R407C. (For R407C models)
• An electric leak detector for R22 cannot detect leaks of R407C.
• Do not use a haloid torch. (Leaks cannot be detected.)
Airtight test procedure
1. Nitrogen gas pressurization
(1) After pressurizing to the design pressure (2.94 MPa) using nitrogen gas, let stand for about
one day. If the pressure does not drop, airtightness is good.
However, if the pressure drops, since the leaking point is unknown, the following bubble test
may also be performed.
(2) After the pressurization described above, spray the flare connection parts, brazed parts, flanges,
and other parts that may leak with a bubbling agent (Kyuboflex, etc.) and visually check for bubbles.
(3) After the airtight test, wipe off the bubbling agent.
2. Pressurization using refrigerant gas and nitrogen gas
(1) Pressurizing to a gas pressure of approximately 0.2 MPa, pressurize to the design pressure
(2.94 MPa) using nitrogen gas.
However, do not pressurize at one time. Stop during pressurization and check that the pres-
sure does not drop.
(2) Check for gas leaks by checking the flare connection parts, brazed parts, flanges, and other
parts which may leak using an R407C compatible electric leak detector.
(3) This test may be used together the with bubble type gas leak test.
2
Evacuation
Evacuate with the ball valve of the outdoor unit closed and evacuate both the
connection piping and the indoor unit from the service port provided on the ball
valve of the outdoor unit using a vacuum pump. (Always evacuate from the
service port of both the high press pipe and the low press pipe.) After the
vacuum reaches 650 Pa [abs], continue evacuation for at least one hour or
more.
* Never perform air purging using refrigerant.
[Fig. 8.3.2] (P.3)
A
System analyzer
B
Lo Knob
C
Hi Knob
D
Ball valve
E
Low press pipe
F
High press pipe
G
Service port
H
Three-way joint
I
Valve
J
Valve
K
Cylinder
L
Scale
M
Vacuum pump
Note:
•
Always add an appropriate amount of refrigerant. Also always seal the
system with liquid refrigerant. Too much or too little refrigerant will cause
trouble.
[Fig. 8.2.2] (P.3)
<A> [Ball valve (low press side)]
(This figure shows the valve in the fully open state.)
<B> [Ball valve (high press side)]
A
Valve stem
[Fully closed at the factory, when connecting the piping, when evacuating, and
when charging additional refrigerant. Open fully after the operations above are
completed.]
B
Stopper pin [Prevents the valve stem from turning 90
°
or more.]
C
Packing (Accessory)
[Manufacturer: Nichiasu corporation]
[Type: T/#1991-NF]
D
Connecting pipe (Accessory)
[Use packing and securely install this pipe to the valve flange so that gas leakage
will not occur. (Tightening torque: low press side 43 N·m (430 kg·cm), high press
side 25 N·m (250 kg·cm)) Coat both surfaces of the packing with refrigerator oil
(Ester oil, ether oil or alkylbenzene [small amount]).]
E
Open (Operate slowly)
F
Cap, copper packing
[Remove the cap and operate the valve stem. Always reinstall the cap after opera-
tion is completed. (Valve stem cap tightening torque: 25 N·m (250 kg·cm) or more)]
G
Service port
[Use this port to evacuate the refrigerant piping and add an additional charge at
the site.
Open and close the port using a double-ended wrench.
Always reinstall the cap after operation is completed. (Service port cap tightening
torque: 14 N·m (140 kg·cm) or more)]
H
ø25.4
I
ø34.93
J
Field piping
[Braze to the connecting pipe. (When brazing, use unoxidized brazing.)]
K
Close-packed packing
L
Hollow packing
Appropriate tightening torque by torque wrench:
Copper pipe external dia. (mm)
Tightening torque (N·m) / (kg·cm)
ø6.35
14 to 18 / 140 to 180
ø9.52
35 to 42 / 350 to 420
ø12.7
50 to 57.5 / 500 to 575
ø15.88
75 to 80 / 750 to 800
ø19.05
100 to 140 / 1000 to 1400
Tightening angle standard:
Pipe diameter (mm)
Tightening angle (
°
)
ø6.35, ø9.52
60 to 90
ø12.7, ø15.88
30 to 60
ø19.05
20 to 35
[Fig. 8.2.3] (P.3)
Note:
If a torque wrench is not available, use the following method as a standard:
When you tighten the flare nut with a wrench, you will reach a point where
the tightening torque will abruptly increase. Turn the flare nut beyond this
point by the angle shown in the table above.
Caution:
•
Always remove the connecting pipe from the ball valve and braze it out-
side the unit.
- Brazing the connecting pipe while it is installed will heat the ball valve and
cause trouble or gas leakage. The piping, etc. inside the unit may also be
burned.
•
Use ester oil, ether oil or alkylbenzene (small amount) as the refrigerator
oil to coat flares and flange connections. (For R407C models)
- The refrigerator oil will degrade if it is mixed with a large amount of mineral oil.
8.3. Airtight test, evacuation, and refrigerant
charging
1
Airtight test
Perform with the stop valve of the outdoor unit closed, and pressurize the con-
nection piping and the indoor unit from the service port provided on the stop
valve of the outdoor unit. (Always pressurize from both the high press pipe and
the low press pipe service ports.)
[Fig. 8.3.1] (P.3)
A
Nitrogen gas
B
To indoor unit
C
System analyzer
D
Lo Knob
E
Hi Knob
F
Stop valve
G
Low press pipe
H
High press pipe
I
Outdoor unit
J
Service port
<For R407C models>
The method of conducting the airtight test is basically the same as for R22 models.
However, since the restrictions have a large affect on deterioration of the refrigera-
tor oil, always observe them. Also, with nonazeotropic refrigerant (R407C, etc.),
gas leakage causes the composition to change and affects performance. There-
fore, perform the airtightness test cautiously.
•
Use a gauge manifold, charging hose, and other parts for the refrigerant
indicated on the unit.
•
Use a graviometer. (One that can measure down to 0.1 kg.)
•
Use a vacuum pump with a reverse flow check valve. (For R407C models)
(Recommended vacuum gauge: ROBINAIR 14830A Thermistor Vacuum
Gauge)
Also use a vacuum gauge that reaches 0.5 Torr or greater after operating
for five minutes.
3
Refrigerant Charging (For R407C models)
Since the refrigerant used with the unit is nonazerotropic, it must be charged in the
liquid state. Consequently, when charging the unit with refrigerant from a cylinder,
if the cylinder does not have a syphon pipe, charge the liquid refrigerant by turning
the cylinder upside-down as shown below. If the cylinder has a syphon pipe like
that shown in the figure at the right, the liquid refrigerant can be charged with the
cylinder standing upright. Therefore, give careful attention to the cylinder specifica-
tions. If the unit should be charged with gas refrigerant, replace all the refrigerant
with new refrigerant. Do not use the refrigerant remaining in the cylinder.
[Fig. 8.3.3] (P.3)