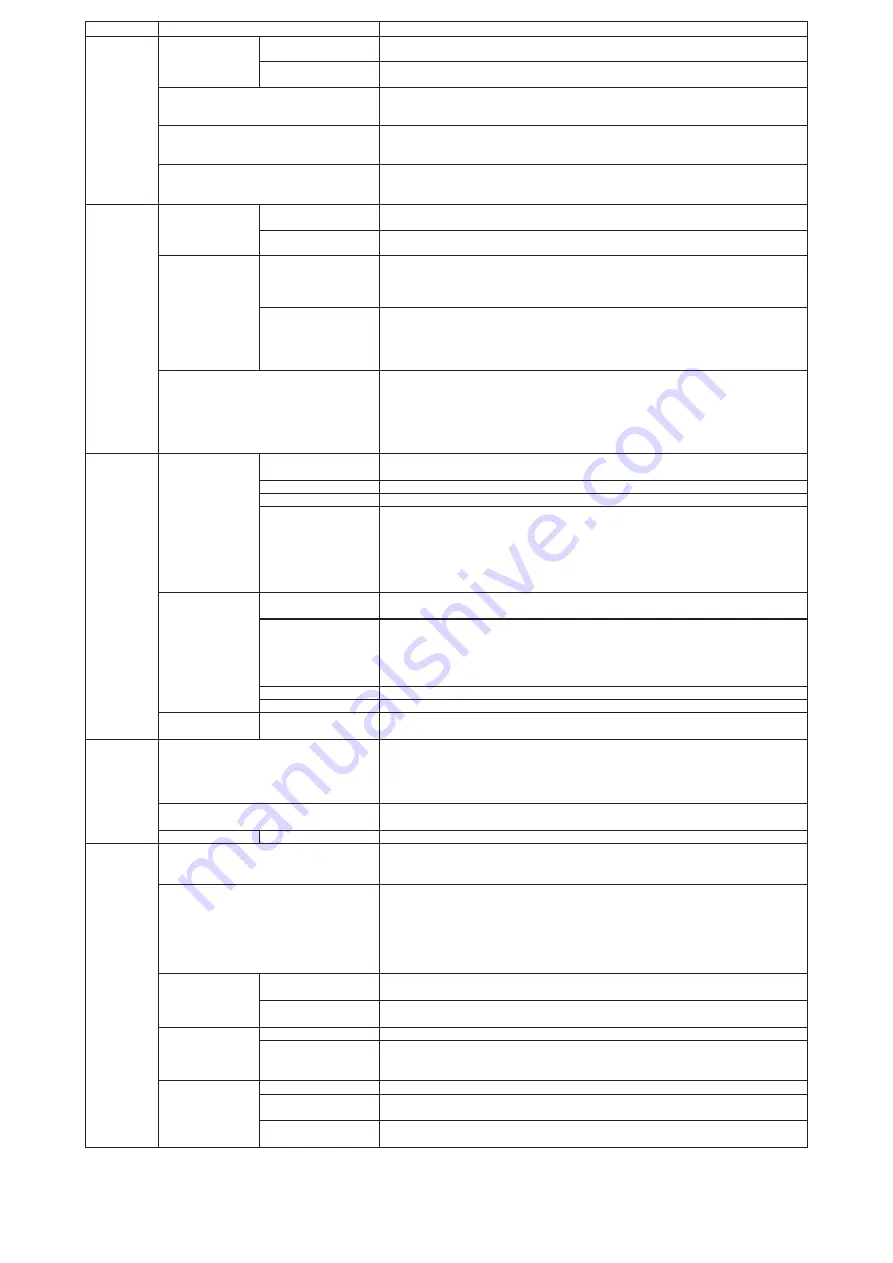
OCH791 _111
Main menu
Setting and display items
Setting details
Timer
Timer
ON/OFF timer
*1
Use to set the operation ON/OFF times.
• Time can be set in 5-minute increments.
Auto-OFF timer
Use to set the Auto-OFF time.
• Time can be set to a value from 30 to 240 in 10-minute increments.
Weekly timer
*1, *2
Use to set the weekly operation ON/OFF times.
• Up to 8 operation patterns can be set for each day.
(Not valid when the ON/OFF timer is enabled.)
OU silent mode
*1, *3
Use to set the time periods in which priority is given to quiet operation of outdoor units over
temperature control. Set the Start/Stop times for each day of the week.
•
Select the desired silent level from ˝Normal,˝ ˝Middle,˝ and ˝Quiet.˝
Night setback
*1
Use to make Night setback settings.
• Select ˝Yes˝ to enable the setting, and ˝No˝ to disable the setting.
The temperature range and the start/stop times can be set.
Energy saving Restriction
Temp. range
*2
Use to restrict the preset temperature range.
•
Different temperature ranges can be set for different operation modes.
Operation lock
Use to lock selected functions.
• The locked functions cannot be operated.
Energy saving
Auto return
*2
Use to get the units to operate at the preset temperature after performing energy saving
operation for a specified time period.
• Time can be set to a value from 30 and 120 in 10-minute increments.
(This function will not be valid when the preset temperature ranges are restricted.)
Schedule
*1, *3
Set the start/stop times to operate the units in the energy saving mode for
each day of the week, and set the energy saving rate.
• Up to 4 energy saving operation patterns can be set for each day.
• Time can be set in 5-minute increments.
• Energy saving rate can be set to a value from 0% or 50 to 90% in 10% increments.
Energy data (for unit time, month, and day)
Displays the amount of power consumption during operation.
• Unit time data: Data for the last one-month period can be displayed in 30-minute units.
• Monthly/daily data: Data for the last 14-month period are displayed in day-and month-
units.
* Data can be deleted.
* Data are obtained based on the power consumption estimated from the operating state.
Initial setting
Basic setting
Main/Sub
When connecting 2 remote controllers, one of them needs to be designated as a sub
controller.
Clock
Use to set the current time.
Daylight saving time
Set the daylight saving time.
Administrator password The administrator password is required to make the settings for the following items.
• Timer setting
• Energy saving setting
• Weekly timer setting
• Restriction setting
• Outdoor unit silent mode setting
• Night set back
Display setting
Main display
Use to switch between ˝Full˝ and ˝Basic˝ modes for the Main display, and use to change
the background colors of the display to black.
Display details
Make the settings for the remote controller related items as necessary.
Clock: The initial settings are ˝Yes˝ and ˝24h˝ format.
Temperature: Set either Celsius (°C) or Fahrenheit (°F).
Room temp.: Set Show or Hide.
Auto mode: Set Auto mode display or Only Auto display.
Contrast • Brightness
Use to adjust screen contrast and brightness.
Language selection
Use to select the desired language.
Operation setting
Auto mode
Whether or not to use Auto mode can be selected by using the button.
This setting is valid only when indoor units with Auto mode function are connected.
Maintenance Error information
Use to check error information when an error occurs.
• Check code, error source, refrigerant address, model name, manufacturing number,
contact information (dealer's phone number) can be displayed.
(The model name, manufacturing number, and contact information need to be registered
in advance to be displayed.)
Filter information
Use to check the filter status.
•
The filter sign can be reset.
Cleaning
Auto descending panel
Use to lift and lower the auto descending panel (Optional parts).
Service
Test run
Select ˝Test run˝ from the Service menu to bring up the Test run menu.
• Test run
• Drain pump test run
Input maintenance info.
Select ˝Input maintenance Info.˝ from the Service menu to bring up the Maintenance
information screen.
The following settings can be made from the Maintenance Information screen.
• Model name input
• Serial No. input
• Dealer information input
• Initialize maintenance info.
Settings
Function setting
Make the settings for the indoor unit functions via the remote controller as
necessary.
LOSSNAY setting
This setting is required only when the operation of CITY MULTI units is interlocked with
LOSSNAY units.
Check
Error history
Display the error history and execute ˝delete error history˝.
Diagnosis
Self check: Error history of each unit can be checked via the remote controller.
Remote controller check: When the remote controller does not work properly, use the
remote controller checking function to troubleshoot the problem.
Others
Maintenance password Use to change the maintenance password.
Initialize remote
controller
Use to initialize the remote controller to the factory shipment status.
Remote controller
information
Use to display the remote controller model name, software version, and serial number.
*1. Clock setting is required.
*2.
1°C (2°F) increments.
*3. This function is available only when certain outdoor units are connected.