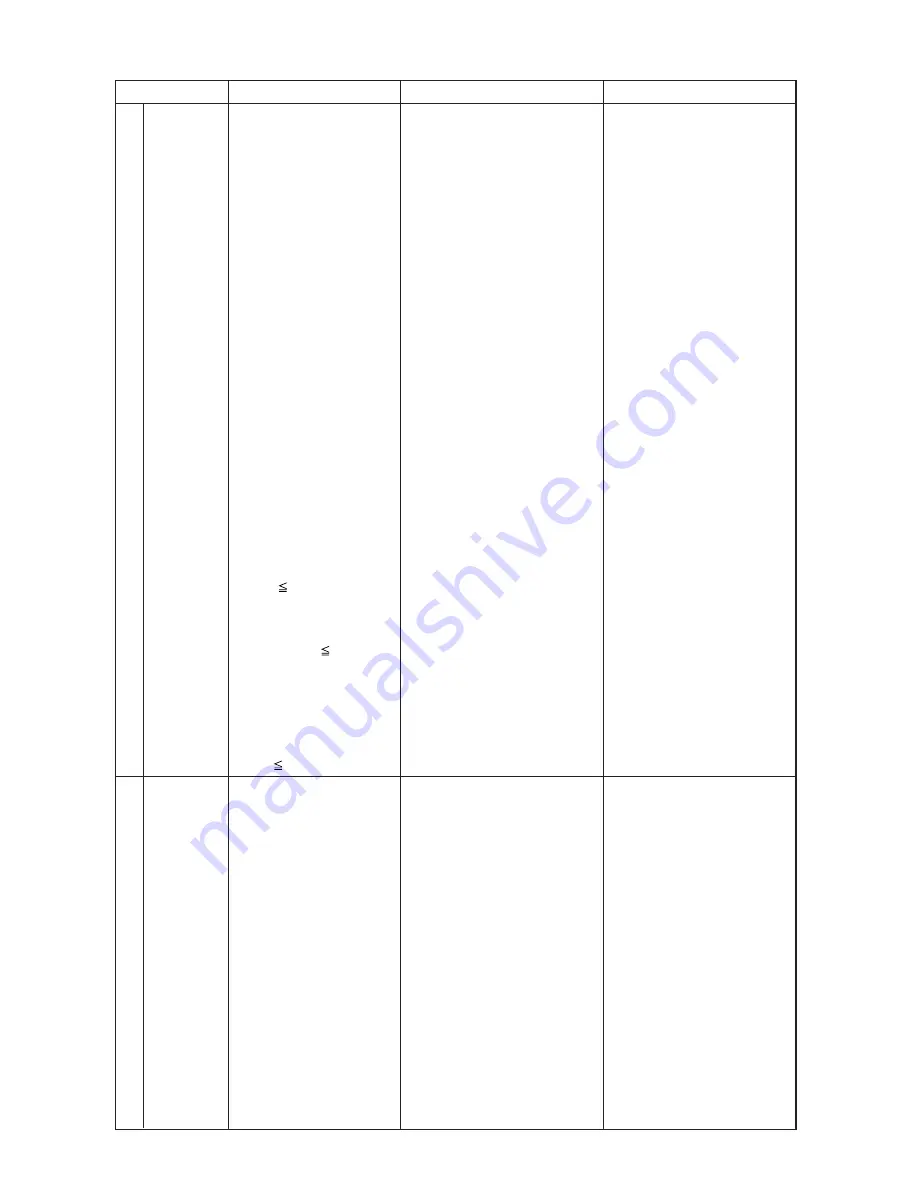
–162–
Checking code
Meaning, detecting method
Cause
Checking method & Countermeasure
1505
1559
Suction
pressure
abnormality
(Variable
capacity unit)
Oil balance
Circuit
abnormality
(Constant
capacity unit)
•
R22 refrigerant models:
1
If it has been determined by
the high pressure pressure,
outlet temperature and low
pressure saturation tempera-
ture that the suction pressure
has approached 0 kg/cm
2
G
(0 MPa) during compressor
operation, back-up control is
performed by the gas bypass.
2
If the condition as in
1
contin-
ues for 3 minutes, the outdoor
unit is stopped and it enters the
re-start prohibit mode for 3 min-
utes after which it is started.
3
If the same condition as in
1
con-
tinues within 30 minutes after re-
starting from the stopped per-
formed in
2
, and error stop is per-
formed and “ 1505 “ is displayed.
4
This error is reset when the power
supply is set to off. (The error re-
set cannot be performed by set-
ting the remote controller to off for
errors such as abnormal outlet
temperature (error code 1102).
5
The vacuum operation protection
is disabled and no error detection
is made after 60 minutes (cumu-
lative) have passed since the
compressor began operating af-
ter the power was turned on.
6
If any one of the following oc-
curs, there will be an error de-
lay and the unit will enter the
3-minute restart mode.
Cooling
If TH2
– 25
°
C when the indoor
unit is operating at 50 % or more
of capacity and the ambient tem-
perature is 15 to 25
°
C or if the
ambient temperature is 25
°
C of
more and TH 3 – 15
°
C.
Heating
If TH3 < – 25
°
C when the ambi-
ent temperature is 0
°
C or more.
Except during defrosting, within
1 hour after recovery from de-
frosting or within 30 minutes of
compressor operation.
•
R407 refrigerant models:
LPS 0 kg/cm
2
G (0 MPa)
1
There will be an error stop
during operation when there is
an inadequacy in the oil bal-
ance circuit connecting the two
units due to the constant ca-
pacity unit TH10b.
If there has been suction pressure er-
ror, do not restart operation by reset-
ting the power supply before the follow-
ing steps have been taken. (Failure to
do follow these steps may cause dam-
age to the compressor.)
<Inspection Procedure>
• Check if there has been a failure to
open the ball valve.
• If the ball valve is open, check if the
extension piping has become plugged.
• Check if there is miss matching of
refrigerant piping, transmission line.
• Check whether or not ET(TH2) ap-
proaches the ambient temperature
after the start of cooling operation.
(Normally there is several degrees
difference between TH2 and TH9.)
----- R22 only
<Steps>
• If the ball valve is open, check if the
extension piping has become plugged.
Also check if there is miss matching of
piping or wiring. After these have been
checked, reset the power supply to re-
set the error error.
Next, operate the unit in the opposite
mode it was in when the error occurred
for 10 to 15 minutes (i.e. operate in cool-
ing mode if the error occurred in heat-
ing mode and vice versa) (This also
applies if there were none of the other
problems such as plugged extension
piping or failure to open the ball valve.)
• If there has been no error after re-
operating after checking the above,
set DIPSW2-10 on the main circuit
board for the outdoor unit to ON.
When these dip switches are set to
ON, the vacuum operation protection
is disabled after 1 hour of operating
time of the compressor has passed
after the power has been turned on.
----- R22 only
• If the temperature of TH2 continues
to approach that of the ambient tem-
perature and if it becomes 15 de-
grees or more higher than TH9 and
the mounting condition thermistor
TH2 is normal, replace the ET cap-
illary. (When cooling only.) --- R 2 2
only
When a oil balance circuit error has
been detected once, before taking
the following steps, do not restart
using the error reset. (This could
damage the compressor)
<Inspection Procedure>
• Confirm that the ball valve on the
oil balance pipe between the con-
stant and variable capacity units has
not been left shut.
• Check the mounting of the TH10b
thermistor on the constant capacity
unit. (check that it has not been
switched with another thermistor or
removed)
<Steps>
• Open the oil balance pipe ball
valves on both units. After check-
ing the mounting of the TH10b ther-
mistor, use the remote controller
reset to make an error reset. Be-
fore restarting the unit, set the con-
stant capacity unit control board
SW3-5 to ON, then restart. (When
these SW are ON, oil balance cir-
cuit abnormality is made invalid.)
•
Operation due to accidental failure to
open the ball valve, especially the ball
valve for the low pressure side.
Cooling: Gas side ball valve
Heating: Liquid side ball valve
•
Temporary vacuum condition due to
the uneven distribution of refrigerant
(insufficient refrigerant in low pres-
sure line) immediately after charging.
•
Miss matching of refrigerant piping,
transmission line.
•
Plugging of ET capillary (CP2) (Cool-
ing) --- R22 only
•
Defective mounting of TH2 ther-
mistor. ---- R22 only
•
The ball valve on the oil balance pipe
between the constant and variable
capacity units has been left shut.
•
There is a problem with the constant
capacity unit TH10b mounting.
Summary of Contents for CITY MULTI PUHY-400YMF-B
Page 16: ... 13 FANCON board CNV CNW CNU CNFC2 ...
Page 17: ... 14 RELAY board CN51C2 CNOUT2 CNRT2 CN52F CN52C2 CNCH ...
Page 26: ... 23 ...
Page 50: ... 47 ...
Page 152: ... 149 Model PUHY 400YMF B 500YMF B ...