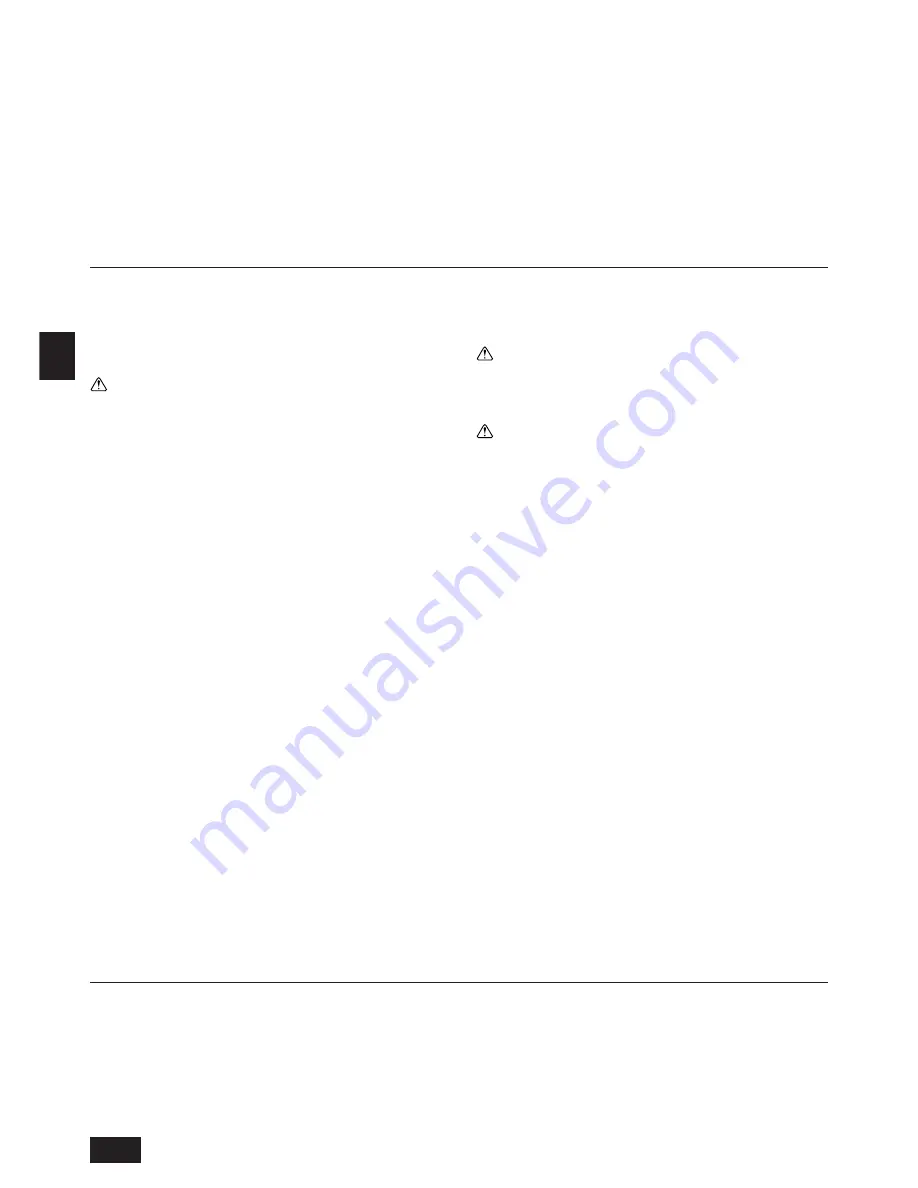
8
GB
D
F
I
NL
E
P
GR
RU
TR
8. Additional refrigerant charge
7. Refrigerant piping installation
A
Always use a non-oxidizing brazing material for brazing the parts. If a non-
oxidizing brazing material is not used, it could cause clogging or damage to
the compressor unit.
B
Never perform heat source unit piping connection work when it is raining.
Warning:
When installing and moving the unit, do not charge it with refrigerant other
than the refrigerant specified on the unit.
- Mixing of a different refrigerant, air, etc. may cause the refrigerant cycle to mal-
function and result in severe damage.
Caution:
•
Use a vacuum pump with a reverse flow check valve. (For R407C models)
- If the vacuum pump does not have a reverse flow check valve, the vacuum
pump oil may flow back into the refrigerant cycle and cause deterioration of
the refrigerator oil and other trouble.
•
Do not use the tools shown below used with conventional refrigerant.
(For R407C models)
(Gauge manifold, charge hose, gas leak detector, check valve, refrigerant
charge base, vacuum gauge, refrigerant recovery equipment)
- Mixing of conventional refrigerant and refrigerator oil may cause the refrig-
erator oil to deteriorate.
- Mixing of water will cause the refrigerator oil to deteriorate.
- R407C refrigerant does not contain any chlorine. Therefore, gas leak detec-
tors for conventional refrigerants will not react to it.
•
Manage the tools more carefully than normal. (For R407C models)
- If dust, dirt, or water gets in the refrigerant cycle, the refrigerator oil will dete-
riorate.
•
Never use existing refrigerant piping. (For R407C models)
- The large amount of chlorine in conventional refrigerant and refrigerator oil
in the existing piping will cause the new refrigerant to deteriorate.
•
Store the piping to be used during installation indoors and keep both
ends of the piping sealed until just before brazing.
- If dust, dirt, or water gets into the refrigerant cycle, the oil will deteriorate and
the compressor may fail.
•
Do not use a charging cylinder. (For R407C models)
- Using a charging cylinder may cause the refrigerant to deteriorate.
•
Do not use special detergents for washing piping.
7.2. Refrigerant piping system
Connection Example
[Fig. 7.2.1] (P.3)
Å
High press pipe
ı
Low press pipe
Ç
Connection of heat source unit/BC controller
Î
Total capacity of indoor units
‰
Liquid line
Ï
Gas line
Ì
Model number
A
BC controller
B
Indoor unit (20~140)
C
Indoor unit (200, 250)
3
Please consult with a water quality control specialist about water quality
control methods and water quality calculations before using anti-corrosive
solutions for water quality management.
4
When replacing a previously installed air conditioning device (even when
only the heat exchanger is being replaced), first conduct a water quality
analysis and check for possible corrosion.
Corrosion can occur in cold-water systems even if there has been no prior
signs of corrosion.
If the water quality level has dropped, please adjust water quality suffi-
ciently before replacing the unit.
6.4. Pump interlock
The heat source unit may become damaged if it is operated with no water circulat-
ing through the pipes.
Be sure to interlock unit operation and the water-circuit pump. Use the terminal
blocks for interlocking (TB8-3, 4) that can be found on the unit.
In the case of a pump interlock circuit signal connection to the TB8-3, 4, remove
the short-circuit wire. Also, to prevent mistaken error detection, resulting from a
poor connection, in the pressure valve 63PW, use a low maintained current of 5mA
or less.
[Fig. 6.4.1] (P.2)
A
Short-circuit wire (Connected before delivery from manufacturer)
B
Pump interlock circuit connection
City Multi R2 Series is constituted by an end branching system in which the refrig-
erant piping from heat source unit is branched at BC controller and connected to
each indoor unit.
The connection method adapted is flange connection for low pressure pipe and
flare connection for high pressure pipe between heat source unit and BC controller,
and flare connection between BC controller and indoor unit. Brazing connection is
employed for joint pipe set and branch pipe set.
Warning:
Always use extreme care to prevent the refrigerant gas (R407C) from leaking
while using fire or flame. If the refrigerant gas comes in contact with the
flame from any source, such as a gas stove, it breaks down and generates a
poisonous gas which can cause gas poisoning. Never weld in an unventilated
room. Always conduct an inspection for gas leakage after installation of the
refrigerant piping has been completed.
7.1. Caution
1
Use the following materials for refrigeration piping.
•
Material: Use refrigerant piping made of phosphorus deoxidized copper.
In addition, be sure that the inner and outer surfaces of the pipes are clean
and free of hazardous sulphur, oxides, dust/dirt, shaving particles, oils,
moisture, or any other contaminant. (For R407C models)
2
Commercially available piping often contains dust and other materials. Always
blow it clean with a dry inert gas.
3
Use care to prevent dust, water or other contaminants from entering the piping
during installation.
4
Reduce the number of bending portions as much as possible, and make bend-
ing radius as big as possible.
5
Always observe the restrictions on the refrigerant piping (such as rated length,
the difference between high/low pressures, and piping diameter). Failure to do
so can result in equipment failure or a decline in heating/cooling performance.
6
The City Multi Series WR2 will stop due an abnormality due to excessive or
insufficient coolant. At such a time, always properly charge the unit. When
servicing, always check the notes concerning pipe length and amount of addi-
tional refrigerant at both locations, the refrigerant volume calculation table on
the back of the service panel and the additional refrigerant section on the la-
bels for the combined number of indoor units.
7
Use liquid refrigerant to fill the system.
8
Never use refrigerant to perform an air purge. Always evacuate using a vacuum
pump.
9
Always insulate the piping properly. Insufficient insulation will result in a de-
cline in heating/cooling performance, water drops from condensation and other
such problems.
0
When connecting the refrigerant piping, make sure the ball valve of the heat
source unit is completely closed (the factory setting) and do not operate it until
the refrigerant piping for the heat source and indoor units has been connected,
a refrigerant leakage test has been performed and the evacuation process has
been completed.
At the time of shipping, the heat source unit is charged with the refrigerant. As this
charge does not include the amount needed for extended piping, additional charg-
ing for each refrigerant line will be required on site. In order that future servicing
may be properly provided, always keep a record of the size and length of each
refrigerant line and the amount of additional charge by writing it in the space pro-
vided on the heat source unit.
8.1. Calculation of Additional Refrigerant
Charge
•
Calculate the amount of additional charge based on the length of the piping
extension and the size of the refrigerant line.
•
Use the table to the right as guide to calculating the amount of additional charg-
ing and charge the system according.
•
If the calculation results of the calculation result in a fraction of less than 0.1 kg.
For example, if the result of the calculation was 10.62 kg, round the result up to
10.7 kg.