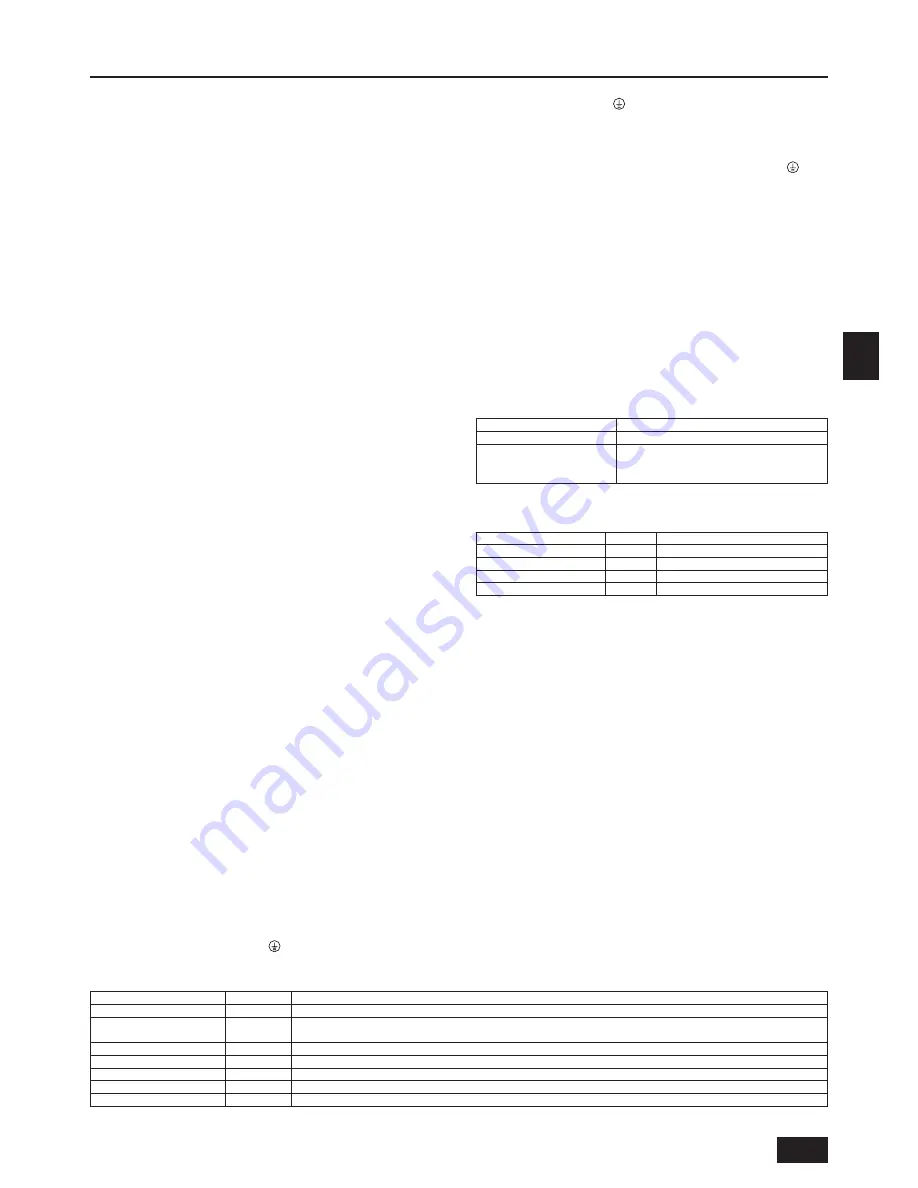
11
GB
D
F
I
NL
E
P
GR
RU
TR
Example of a group operation system with multiple heat source units (Shielding wires and address setting are
necessary.)
<Examples of Transmission Cable Wiring>
[Fig. 9.3.1] M-NET Remote Controller (P.4)
[Fig. 9.3.2] MA Remote Controller (P.4)
A
Group 1
B
Group 3
C
Group 5
D
Shielded Wire
E
Sub Remote Controller
( ) Address
2
Wiring examples
•
Controller name, symbol and allowable number of controllers.
2. Remote control cables
Kind of remote control cable
Cable diameter
Remarks
2-core cable (unshielded)
0.3 to 1.25 mm
2
When 10 m is exceeded, use cable with the
same specifications as (1) Transmission line
wiring
9. Wiring
9.1. Caution
1
Follow ordinance of your governmental organization for technical standard re-
lated to electrical equipment, wiring regulations and guidance of each electric
power company.
2
Wiring for control (hereinafter referred to as transmission line) shall be (5 cm or
more) apart from power source wiring so that it is not influenced by electric
noise from power source wiring. (Do not insert transmission line and power
source wire in the same conduit.)
3
Be sure to provide designated grounding work to heat source unit.
4
Give some allowance to wiring for electrical part box of indoor and heat source
units, because the box is sometimes removed at the time of service work.
5
Never connect the main power source to terminal block of transmission line. If
connected, electrical parts will be burnt out.
6
Use 2-core shield cable for transmission line. If transmission lines of different
systems are wired with the same multiplecore cable, the resultant poor trans-
mitting and receiving will cause erroneous operations.
7
Only the transmission line specified should be connected to the terminal block
for heat source unit transmission.
(Transmission line to be connected with indoor unit : Terminal block TB3 for
transmission line, Other : Terminal block TB7 for centralized control)
Erroneous connection does not allow the system to operate.
8
In case to connect with the upper class controller or to conduct group opera-
tion in different refrigerant systems, the control line for transmission is required
between the heat source units each other.
Connect this control line between the terminal blocks for centralized control.
(2-wire line with no polarity)
When conducting group operation in different refrigerant systems without con-
necting to the upper class controller, replace the insertion of the short circuit
connector from CN41 of one heat source unit to CN40.
9
Group is set by operating the remote controller.
0
The unused knockout holes should be closed and the opening of refrigerant
pipes, water pipes, power source and transmission wires should be filled with
putty and so on to prevent from rain. (field construction)
9.2. Control box and connecting position of
wiring
1. Connect the indoor unit transmission line to transmission terminal block (TB3),
or connect the wiring between heat source units or the wiring with the central
control system to the central control terminal block (TB7).
Name
heat source unit controller
BC Controller
Indoor Unit Controller
Remote Controller
Symbol
OC
BC
IC
RC
Allowable number of controllers
One controller for one OC
Two to ten controllers for one OC
Maximum of two per group
When using shielded wiring, connect shield ground of the indoor unit transmis-
sion line to the earth screw (
) and connect shield ground of the line between
heat source units and the central control system transmission line to the shield
(S) terminal of the central control terminal block (TB7) shield (S) terminal. In
addition, in the case of heat source units whose power supply connector CN41
has been replaced by CN40, the shield terminal (S) of terminal block (TB7) of
the central control system should also be connected to the ground (
).
[Fig. 9.2.1] (P.4)
A
Power source
B
Transmission line
2. Conduit mounting plates (ø27) are being provided. Pass the power supply and
transmission wires through the appropriate knock-out holes, then remove the
knock-out piece from the bottom of the terminal box and connect the wires.
3. Fix power source wiring to terminal box by using buffer bushing for tensile
force (PG connection or the like).
9.3. Wiring transmission cables
1
Types of control cables
1. Wiring transmission cables
•
Types of transmission cables: Shielding wire CVVS or CPEVS
•
Cable diameter: More than 1.25 mm
2
•
Maximum wiring length: Within 200 m
<Wiring Method and Address Settings>
a. Always use shielded wire when making connections between the heat source unit (OC) and the indoor unit (IC), as well for all OC-OC, and IC-IC wiring intervals.
b. Use feed wiring to connect terminals M1 and M2 and the ground terminal on the transmission cable terminal block (TB3) of each heat source unit (OC) to terminals M1,
M2 and terminal S on the transmission cable block of the indoor unit (IC).
c.
Connect terminals 1 (M1) and 2 (M2) on the transmission cable terminal block of the indoor unit (IC) that has the most recent address within the same group to the
terminal block on the remote controller (RC).
d. Connect together terminals M1, M2 and terminal S on the terminal block for central control (TB7) for the heat source unit (OC).
e. On one heat source unit only, change the jumper connector on the control panel from CN41 to CN40.
f.
Connect the terminal S on the terminal block for central control (TB7) for the heat source unit (OC) for the unit into which the jumper connector was inserted into CN40
in Step above to the ground terminal
in the electrical component box.
g. Set the address setting switch as follows.
*
To set the heat source unit address to 100, the heat source address setting switch must be set to 50.
Unit
Range
Setting Method
IC (Main)
01 to 50
Use the most recent address within the same group of indoor units
IC (Sub)
01 to 50
Use an address, other than that of the IC (Main) from among the units within the same group of indoor units. This must be
in sequence with the IC (Main)
Heat source Unit
51 to 100
Use the most recent address of all the indoor units plus 50
BC controller
51 to 100
Heat source unit address plus 1
M-NET R/C (Main)
101 to 150
Set at an IC (Main) address within the same group plus 100
M-NET R/C (Sub)
151 to 200
Set at an IC (Main) address within the same group plus 150
MA R/C
–
Unnecessary address setting (Necessary main/sub setting)
h. The group setting operations among the multiple indoor units is done by the remote controller (RC) after the electrical power has been turned on.