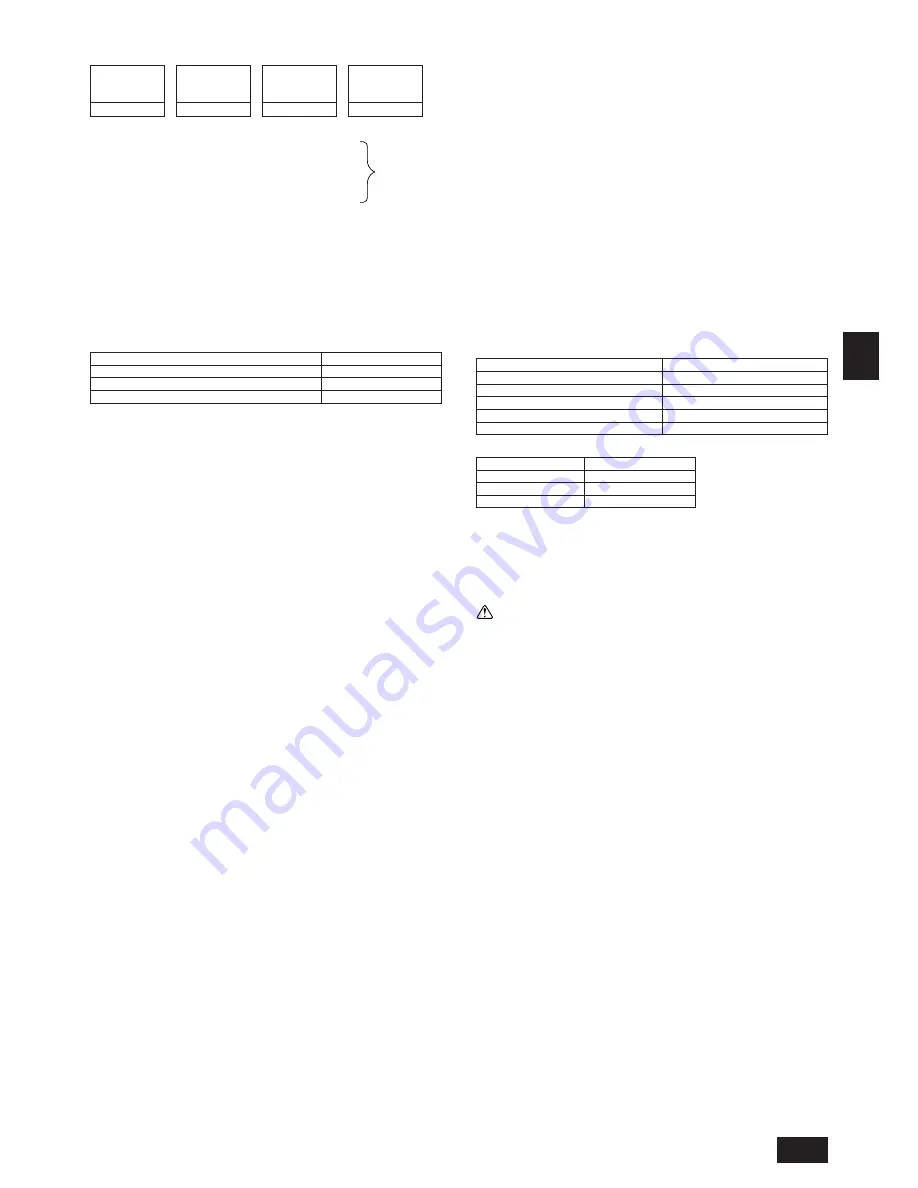
9
GB
D
F
I
NL
E
P
GR
RU
TR
<Additional Charge>
<Example>
Indoor 1: 40
A: ø19.05
40 m
a: ø6.35
10 m
2: 100
B: ø9.52
10 m
b: ø9.52
5 m
3: 40
C: ø9.52
15 m
c: ø6.35
10 m
4: 32
d: ø6.35
10 m
5: 63
e: ø9.52
10 m
The total length of each liquid line is as follows:
ø19.05: A = 40 m
ø9.52: B + b + e = 10 + 5 + 10 = 25 m
ø6.35: a + c + d = 10 + 10 + 10 = 30 m
Therefore,
<Calculation example>
Additional refrigerant charge
= 40
×
0.16 + 25
×
0.06 + 30
×
0.024 + 2 = 10.7 kg
Value of
α
Total capacity of connecting indoor units
α
to Model 80
1.0 kg
Models 81 to 160
1.5 kg
Models 161 to 325
2.0 kg
E
Open (Operate slowly)
F
Cap, copper packing
[Remove the cap and operate the valve stem. Always reinstall the cap after op-
eration is completed. (Valve stem cap tightening torque: 25 N·m (250 kg·cm) or
more)]
G
Service port
[Use this port to evacuate the refrigerant piping and add an additional charge at
the site.
Open and close the port using a double-ended wrench.
Always reinstall the cap after operation is completed. (Service port cap tightening
torque: 14 N·m (140 kg·cm) or more)]
H
Flare nut
[Tightening torque: 120 N·m (1200 kg·cm)
Loosen and tighten this nut using a double-ended wrench.
Coat the flare contact surface with refrigerator oil (Ester oil, ether oil or alkylbenzene
[small amount]).]
I
ø19.05
J
ø25.4 (PQRY-P200)
ø28.58 (PQRY-P250)
K
Field piping
[Braze to the connecting pipe. (When brazing, use unoxidized brazing.)]
L
Close-packed packing
M
Hollow packing
Appropriate tightening torque by torque wrench:
Copper pipe external dia. (mm)
Tightening torque (N·m) / (kg·cm)
ø6.35
14 to 18 / 140 to 180
ø9.52
35 to 42 / 350 to 420
ø12.7
50 to 57.5 / 500 to 575
ø15.88
75 to 80 / 750 to 800
ø19.05
100 to 140 / 1000 to 1400
Tightening angle standard:
Pipe diameter (mm)
Tightening angle (
°
)
ø6.35, ø9.52
60 to 90
ø12.7, ø15.88
30 to 60
ø19.05
20 to 35
[Fig. 8.2.3] (P.3)
Note:
If a torque wrench is not available, use the following method as a standard:
When you tighten the flare nut with a wrench, you will reach a point where
the tightening torque will abrupt increase. Turn the flare nut beyond this point
by the angle shown in the table above.
Caution:
•
Always remove the connecting pipe from the ball valve and braze it out-
side the unit.
- Brazing the connecting pipe while it is installed will heat the ball valve and
cause trouble or gas leakage. The piping, etc. inside the unit may also be
burned.
•
Use ester oil, ether oil or alkylbenzene (small amount) as the refrigerator
oil to coat flares and flange connections. (For R407C models)
- The refrigerator oil will degrade if it is mixed with a large amount of mineral
oil.
8.3. Airtight test, evacuation, and refrigerant
charging
1
Airtight test
Perform with the stop valve of the heat source unit closed, and pressurize the
connection piping and the indoor unit from the service port provided on the
stop valve of the heat source unit. (Always pressurize from both the liquid pipe
and the gas pipe service ports.)
[Fig. 8.3.1] (P.3)
A
Nitrogen gas
B
To indoor unit
C
System analyzer
D
Lo Knob
E
Hi Knob
F
Stop valve
G
Low press pipe
H
High press pipe
I
Heat source unit
J
Service port
<For R407C models>
The method of conducting the airtight test is basically the same as for R22 models.
However, since the restrictions have a large affect on deterioration of the refrigera-
tor oil, always observe them. Also, with nonazeotropic refrigerant (R407C, etc.),
gas leakage causes the composition to change and affects performance. There-
fore, perform the airtightness test cautiously.
8.2. Caution for piping connection/valve
operation
•
Conduct piping connection and valve operation accurately.
•
The gas side connecting pipe is being assembled for shipment.
1
For brazing to the connecting pipe with flange, remove the connecting pipe
with flange from the ball valve, and braze it at the outside of the unit.
2
During the time when removing the connecting pipe with flange, remove
the seal attached on the back side of this sheet and paste it onto the flange
surface of the ball valve to prevent the entry of dust into the valve.
3
The refrigerant circuit is closed with a round, close-packed packing at the
shipment to prevent gas leak between flanges. As no operation can be
done under this state, be sure replace the packing with the hollow packing
attached at the piping connection.
4
At the mounting of the hollow packing, wipe off dust attached on the flange
sheet surface and the packing. Coat refrigerating machine oil (Ester oil,
ether oil or alkylbenzene [small amount]) onto both surfaces of the pack-
ing.
[Fig. 8.2.1] (P.3)
•
After evacuation and refrigerant charge, ensure that the handle is fully open. If
operating with the valve closed, abnormal pressure will be imparted to the
high- or low-pressure side of the refrigerant circuit, giving damage to the com-
pressor, four-way valve, etc.
•
Determine the amount of additional refrigerant charge by using the formula,
and charge refrigerant additionally through the service port after completing
piping connection work.
•
After completing work, tighten the service port and cap securely not to gener-
ate gas leak.
[Fig. 8.2.2] (P.3)
<A> [Ball valve (low press side)]
(This figure shows the valve in the fully open state.)
<B> [Ball valve (high press side)]
A
Valve stem
[Fully closed at the factory, when connecting the piping, when evacuating, and
when charging additional refrigerant. Open fully after the operations above are
completed.]
B
Stopper pin [Prevents the valve stem from turning 90
°
or more.]
C
Packing (Accessory)
[Manufacturer: Nichiasu corporation]
[Type: T/#1991-NF]
D
Connecting pipe (Accessory)
[Use packing and securely install this pipe to the valve flange so that gas leakage
will not occur. (Tightening torque: 25 N·m (250 kg·cm)) Coat both surfaces of the
packing with refrigerator oil (Ester oil, ether oil or alkylbenzene [small amount]).]
Liquid pipe size
Total length of
ø6.35
×
0.024
(m)
×
0.024 (kg/m)
Liquid pipe size
Total length of
ø9.52
×
0.06
(m)
×
0.06 (kg/m)
Additional
refrigerant charge
(kg)
Liquid pipe size
Total length of
ø19.05
×
0.16
(m)
×
0.16 (kg/m)
=
+
+
+
α
At the
conditions
below: