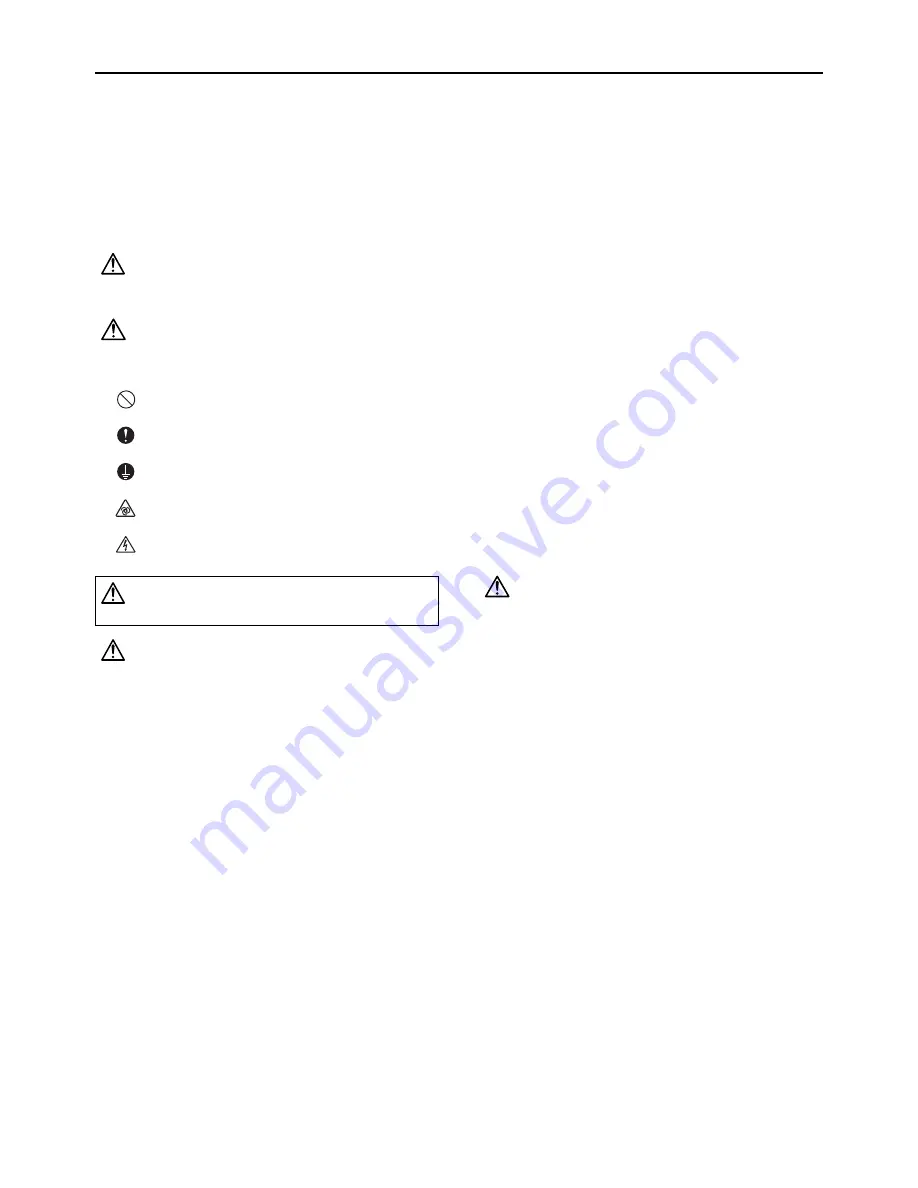
ii
HWE1804A
GB
Safety Precautions
Read before installation and performing electrical work
Symbol explanations
Ask your dealer or a qualified technician to install the unit.
- Improper installation by the user may result in water leakage, electric shock,
or fire.
Properly install the unit on a surface that can withstand its weight.
- Unit installed on an unstable surface may fall and cause injury.
Only use specified cables. Securely connect each cable so that the ter-
minals do not carry the weight of the cable.
- Improperly connected cables may produce heat and start a fire.
Take appropriate safety measures against wind gusts and earthquakes
to prevent the unit from toppling over.
- Improper installation may cause the unit to topple over and cause injury or
damage to the unit.
Only use accessories (i.e., air cleaners, humidifiers, electric heaters)
recommended by Mitsubishi Electric.
Do not make any modifications or alterations to the unit.
Consult your dealer for repair.
- Improper repair may result in water leakage, electric shock, or fire.
Do not touch the heat exchanger fins with bare hands.
- The fins are sharp and pose a risk of cuts.
In the event of a refrigerant leak, thoroughly ventilate the room.
- If gaseous refrigerant leaks out and comes in contact with an open flame,
toxic gases will be generated.
Properly install the unit according to the instructions in the Installation
Manual.
- Improper installation may result in water leakage, electric shock, or fire.
Have all electrical work performed by an authorized electrician accord-
ing to the local regulations and the instructions in this manual. Use a
dedicated circuit.
- Insufficient power supply capacity or improper installation of the unit may re-
sult in malfunctions of the unit, electric shock, or fire.
Disconnect all electric power supplies before accessing of electric
parts (inner of control box, fan motor, drain pump etc.)
- Touching electric parts result in electric shock.
Keep electrical parts away from water.
- Wet electrical parts pose a risk of electric shock, smoke, or fire.
Securely attach the control box cover.
- If the cover is not installed properly, dust or water may infiltrate and pose a
risk of electric shock, smoke, or fire.
Only use the type of refrigerant that is indicated on the unit when install-
ing or relocating the unit.
- Infiltration of any other types of refrigerant or air into the unit may adversely
affect the refrigerant cycle and may cause the pipes to burst or explode.
When installing the unit in a small space, take appropriate precautions
to prevent leaked refrigerant from reaching the limiting concentration.
- Leaked refrigerant gas will displace oxygen and may cause oxygen starva-
tion. Consult your dealer before installing the unit.
Consult your dealer or a qualified technician when moving or reinstall-
ing the unit.
- Improper installation may result in water leakage, electric shock, or fire.
After completing the service work, check for a refrigerant leak.
- If leaked refrigerant is exposed to a heat source, such as a fan heater, stove,
or electric grill, toxic gases will be generated.
Do not try to defeat the safety features of the unit.
- Forced operation of the pressure switch or the temperature switch by defeat-
ing the safety features for these devices, or the use of accessories other than
the ones that are recommended by Mitsubishi Electric may result in smoke,
fire, or explosion.
Consult your dealer for proper disposal method.
Do not use a leak detection additive.
Precautions for handling units for use with R410A
Do not use the existing refrigerant piping.
- A large amount of chlorine that may be contained in the residual refrigerant
and refrigerator oil in the existing piping may cause the refrigerator oil in the
new unit to deteriorate.
Use refrigerant piping materials made of phosphorus deoxidized cop-
per. Keep the inner and outer surfaces of the pipes clean and free of
such contaminants as sulfur, oxides, dust, dirt, shaving particles, oil,
and moisture.
- Contaminants in the refrigerant piping may cause the refrigerator oil to de-
teriorate.
Store the piping materials indoors, and keep both ends of the pipes
sealed until immediately before brazing. (Keep elbows and other joints
wrapped in plastic.)
- Infiltration of dust, dirt, or water into the refrigerant system may cause the
refrigerator oil to deteriorate or cause the compressor to malfunction.
Use a small amount of ester oil, ether oil, or alkyl benzene to coat flares
and flanges.
- Infiltration of a large amount of mineral oil may cause the refrigerator oil to
deteriorate.
Charge the system with refrigerant in the liquid phase.
- If gaseous refrigerant is drawn out of the cylinder first, the composition of the
remaining refrigerant in the cylinder will change and become unsuitable for
use.
Only use R410A.
- The use of other types of refrigerant that contain chloride may cause the re-
frigerator oil to deteriorate.
Use a vacuum pump with a check valve.
- If a vacuum pump that is not equipped with a check valve is used, the vac-
uum pump oil may flow into the refrigerant cycle and cause the refrigerator
oil to deteriorate.
Prepare tools for exclusive use with R410A. Do not use the following
tools if they have been used with the conventional refrigerant: gauge
manifold, charging hose, gas leak detector, check valve, refrigerant
charge base, vacuum gauge, and refrigerant recovery equipment.
- If the refrigerant or the refrigerator oil that may be left on these tools are
mixed in with R410A, it may cause the refrigerator oil in the new system to
deteriorate.
Infiltration of water may cause the refrigerator oil to deteriorate.
Leak detectors for conventional refrigerants will not detect an R410A leak
because R410A is free of chlorine.
Thoroughly read the following safety precautions prior to installation.
Observe these safety precautions for your safety.
This equipment may have adverse effects on the equipment on the same power supply system.
Contact the local power authority before connecting to the system.
WARNING
This symbol indicates that failure to follow the instructions exactly as
stated poses the risk of serious injury or death.
CAUTION
This symbol indicates that failure to follow the instructions exactly as
stated poses the risk of serious injury or damage to the unit.
Indicates an action that must be avoided.
Indicates important instructions.
Indicates a parts that requires grounding.
Indicates that caution must be taken with rotating parts. (This
symbol is on the main unit label.) <Color: Yellow>
Indicates that the parts that are marked with this symbol pose
a risk of electric shock. (This symbol is on the main unit label.)
<Color: Yellow>
WARNING
Carefully read the labels affixed to the main unit.
WARNING
CAUTION
Summary of Contents for CITY MULTI PEFY Series
Page 1: ......
Page 5: ...HWE1804A GB ...
Page 47: ... 42 VIII Disassembly Procedure GB HWE1804A ...
Page 48: ......