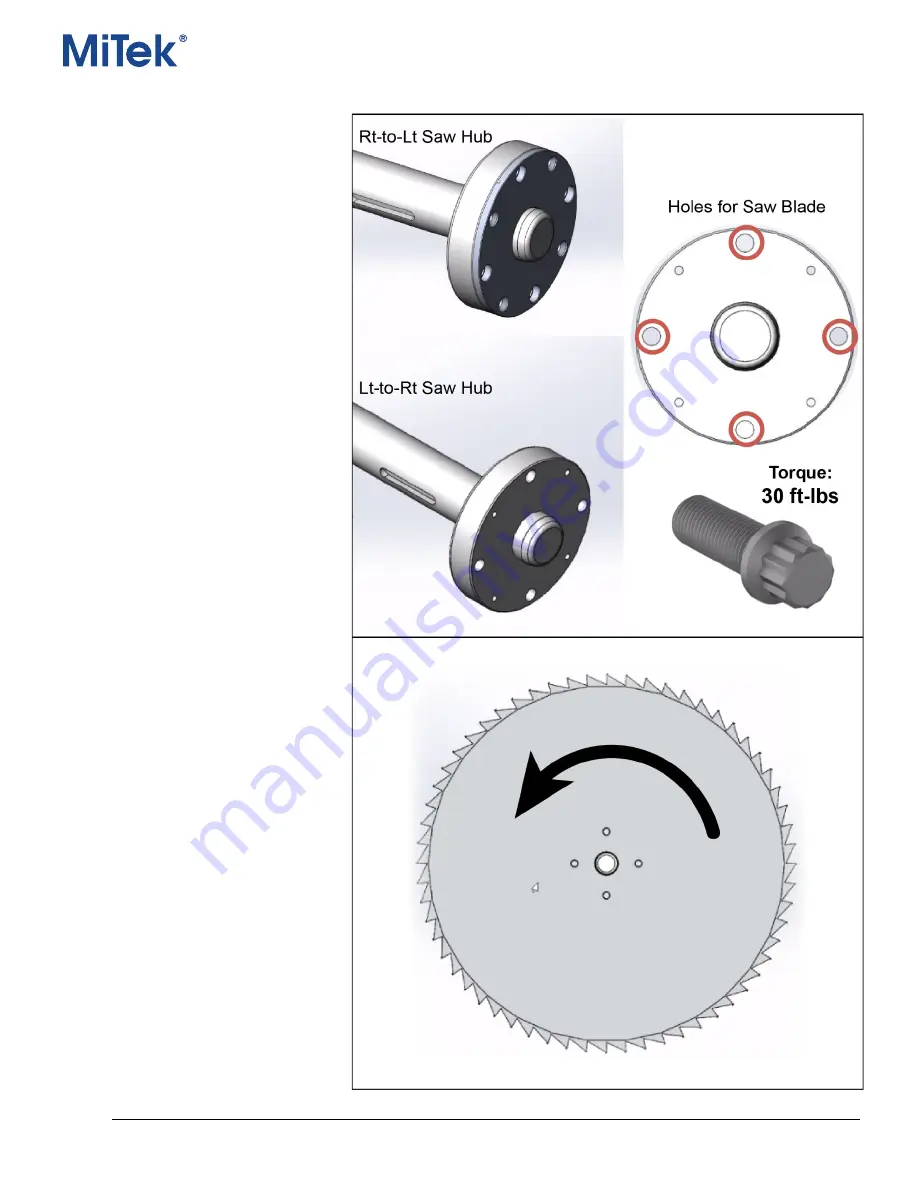
Safety, Operation, & Maintenance Manual
Linear Cut Processing Systems
Replacing the Saw Blade
001128
26
7
Replacing the Saw Blade
Supplies:
•
3/8” 12-point socket
•
Torque wrench driver
Frequency:
Recommended once a week for 1-shift
operations, but adjust as needed for your
schedule and environment.
Procedure:
1.
Lockout/tagout
2.
Open saw chamber door.
3.
Manually turn rotational
assembly until the blade and hub
are at a convenient angle.
4.
Remove 4 bolts holding saw
blade.
5.
Remove saw blade and set aside
for retipping or safe disposal.
6.
Place new or sharpened saw
blade on arbor.
7.
Tighten the bolts to the torque
specification shown in the
graphic.