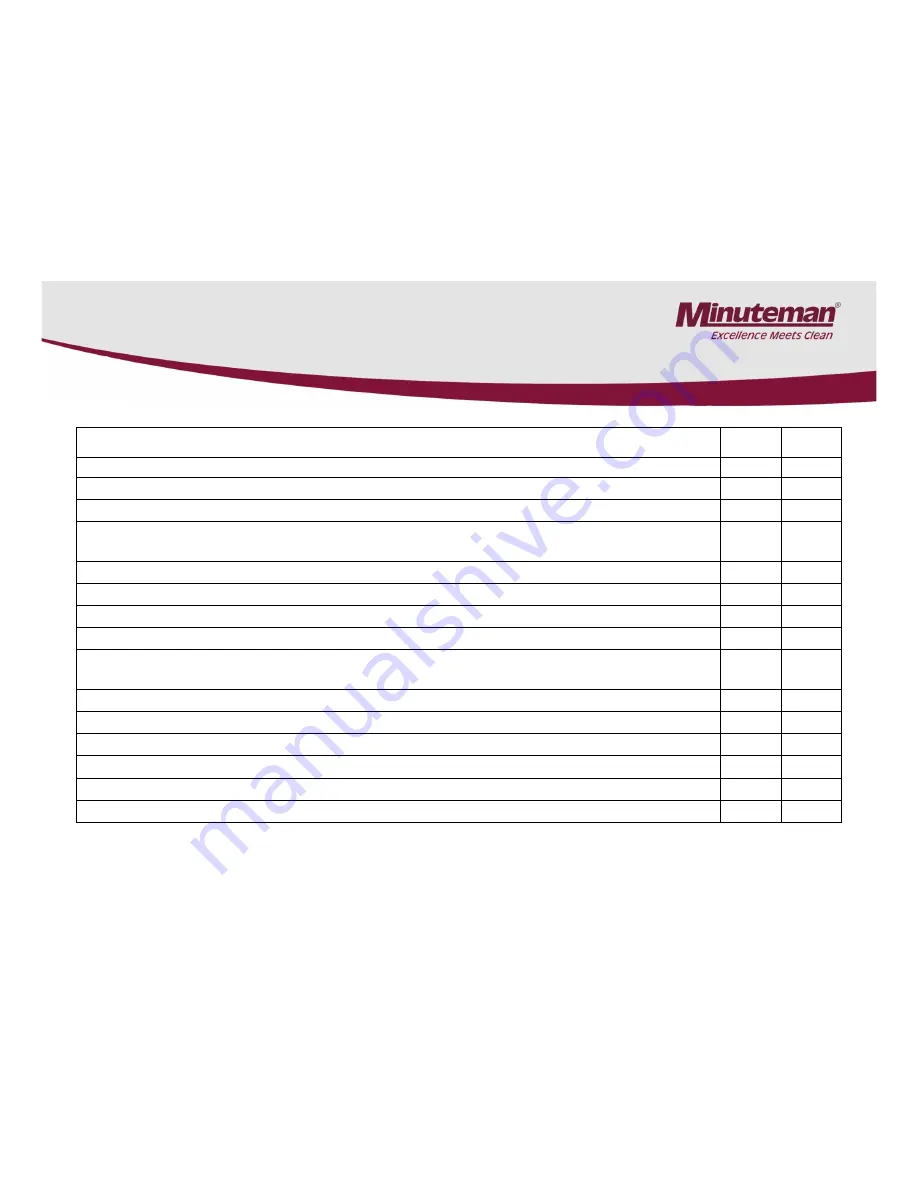
3.1 Minuteman System Maintenance K
Page 10
To be performed by the customer/user
Interval
Daily Weekly
Fill the clean water tank and mix the proper amount and type of cleaning solution.
O
Charger the batteries.
O
Check the brush head, Clean if needed with a damp cloth. Do not get water inside
the motor.
O
Check the squeegee, clean if needed
O
Check the lid gasket on the recovery tank.
O
Empty and flush the recovery tank with clean water.
O
Clean the filter/float inside the recovery tank.
O
Check the water levels of all the batteries. Add distilled water, if needed. Do not
over fill.
O
Check the pads and brushes for wear. Replace if needed.
O
Check the squeegee hose for clogs, damage and wear. Replace if needed
O
Check the squeegee rubbers for cuts and wear. Flip the blade(s) over or replace.
O
Check the solution filter. Clean if needed.
O
Flush the clean water solution tank with warm water.
O
Test all the functions of the machine.
O
Summary of Contents for E17BD
Page 6: ...2 Technical Specifications E17BD E20 Page 6 ...
Page 7: ...2 1 Dimensions E17BD E20 BD With a Straight Squeegee Page 7 ...
Page 8: ...2 2 Dimensions E17 E20 With Curved Squeegee Page 8 ...
Page 11: ...3 2 Minuteman System Maintenance I Page 11 ...
Page 12: ...3 3 Minuteman System Maintenance II Page 12 ...
Page 13: ...3 4 Minuteman System Maintenance S Page 13 ...
Page 39: ...11 Squeegee Curved 11 Page 39 ...
Page 40: ...11 Squeegee Curved 11 1 Page 40 ...
Page 52: ...17 1 Solution Filter Version 1 17 1 Page 52 ...
Page 64: ...20 Notes Page 64 ...