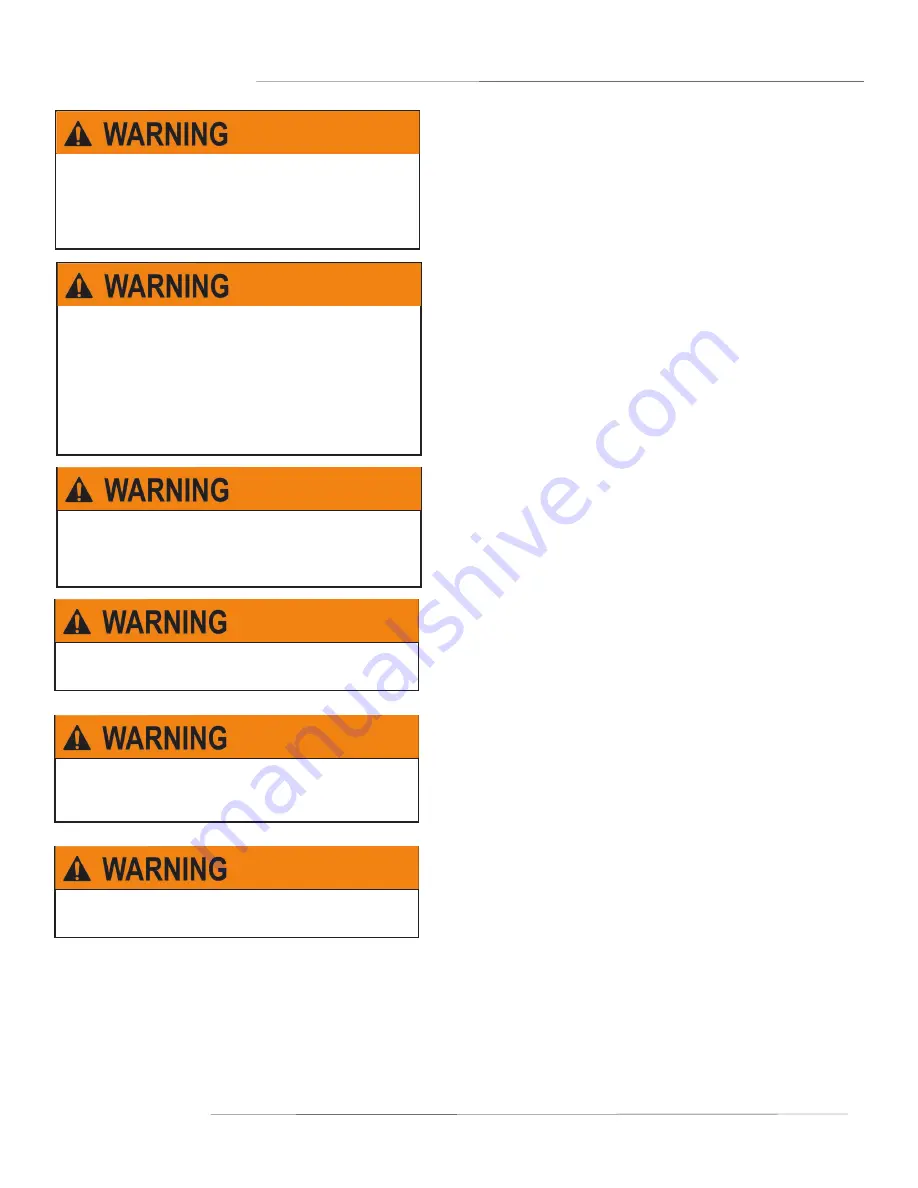
Dowel Drill
Manual
22
PRESSURE
REGULATOR
THESE REGULATORS ARE INTENDED FOR USE IN
INDUSTRIAL COMPRESSED AIR SYSTEMS ONLY.
DO NOT USE THESE REGULATORS WHERE PRES-
SURE OR TEMPERATURE CAN EXCEED RATED
OPERATING CONDITIONS. SEE SPECIFICATIONS.
IF OUTLET PRESSURES IN EXCESS OF THE
REGULATOR PRESSURE SETTING COULD CAUSE
DOWNSTREAM EQUIPMENT TO RUPTURE OR
MALFUNCTION, INSTALL A PRESSURE RELIEF DE-
VICE DOWNSTREAM OF THE REGULATOR. THE
RELIEF PRESSURE AND FLOW CAPACITY OF THE
RELIEF DEVICE MUST SATISFY SYSTEM REQUIRE-
MENTS.
BEFORE USING WITH FLUIDS OTHER THAN AIR,
FOR NON-INDUSTRIAL APPLICATIONS, OR FOR
LIFE SUPPORT SYSTEMS, CONSULT C.A. NOR-
GREN CO
FOR COMPRESSED AIR SERVICE ONLY. NOT TO
BE USED ON LIFE SUPPORT SYSTEMS.
MAINTENANCE
INSTILLATION
OPERATION ADJUSTMENTS
Install regulators so the airflow is in the direction of
the arrow as indicated on the head of unit. Regula-
tors should be installed downstream from filters and
upstream from lubricators, but as close as possible to
the pneumatic tools or appliances being serviced. The
regulator will accurately control secondary pressure
between 5 and 200 PSI (0.34 and 13.8 Bar), maximum
primary pressure is 250 PSI (17 Bar). The self-bleed
feature permits use on dead-end applications.
Units are die cast aluminum. Do not over
torque when installing regulator or gauge. Use
of Teflon tape is not recommended.
After the regulator is installed, back off pressure by
adjusting T-handle counterclockwise before the air
is turned on. Turn on air supply and adjust T-handle
clockwise until the pressure gauge shows desired
pressure. To lock the T-handle, tighten lock nut on
adjustment screw.
On detection of air leaks, pressure fluctuation, or
“creep”, depressurize system and remove bottom cap.
Inspect valve seat for damage or wear. Inspect seat
in head casting for foreign material or damage. Clean
with naptha or kerosene and blow out with air. Replace
any damaged parts. If leaks persist, remove spring
cage, inspect piston and piston seat for wear or for-
eign materials. Replace any damaged Parts.
Regulator is preset at factory to 85 PSI, Do not
adjust, as it will void your warranty.
Summary of Contents for A-1-24
Page 20: ...Dowel Drill Manual 20 PARTS MANUAL...
Page 21: ...21 Dowel Drill Manual PARTS MANUAL...
Page 26: ...Dowel Drill Manual 26 NOTES...