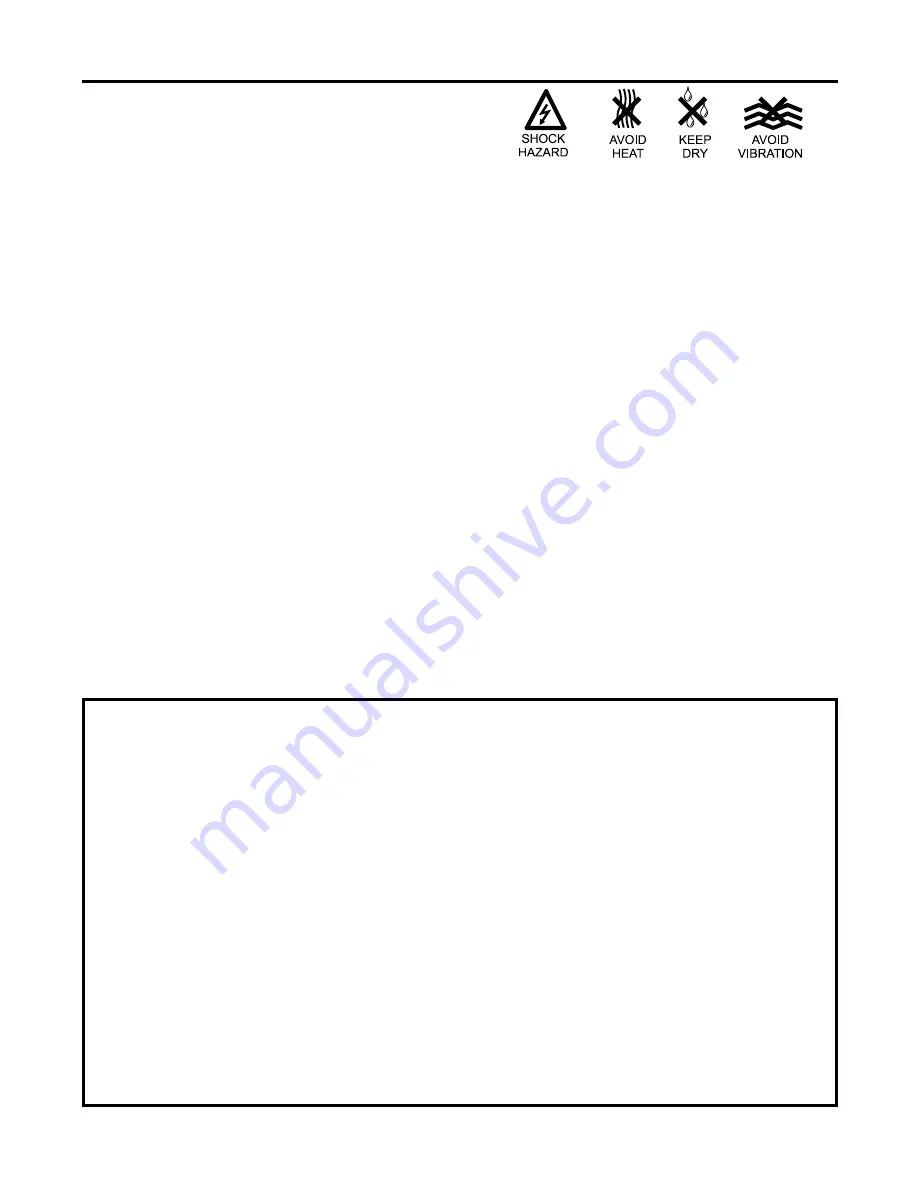
i
Safety Warnings
•
This symbol
denotes an important safety tip or warning.
Please read these instructions carefully before performing any
of the procedures contained in this manual.
•
DO NOT INSTALL, REMOVE, OR REWIRE THIS
EQUIPMENT WITH POWER APPLIED. Have a qualified
electrical technician install, adjust and service this equipment.
Follow the National Electrical Code and all other applicable
electrical and safety codes, including the provisions of the
Occupational Safety and Health Act (OSHA), when installing
equipment.
•
Reduce the chance of an electrical fire, shock, or explosion by
proper grounding, over-current protection, thermal protection, and
enclosure. Follow sound maintenance procedures
.
It is possible for a drive to run at full speed as a result
of a component failure. Minarik strongly recommends
the installation of a master switch in the main power input
to stop the drive in an emergency.
Circuit potentials are at 115 VAC above earth ground.
Avoid direct contact with the printed circuit board or with
circuit elements to prevent the risk of serious injury or
fatality. Use a non-metallic screwdriver for adjusting the
calibration trimpots. Use approved personal protective
equipment and insulated tools if working on this drive
with power applied.
250-0146r3_readers_spreads.qxd 7/10/01 4:40 PM Page i
Summary of Contents for MM30000 Series
Page 1: ...SCR Adjustable Speed Drives for DC Brush Motors User s Manual MM30000 Series Model MM31640A...
Page 8: ...2 Figure 1 Dimensions Dimensions...
Page 24: ...18 Operation Figure 9 Dynamic Brake Connection...
Page 41: ...35 Figure 20 Diagnostic LED Locations POWER LED CURRENT LIMIT LED...
Page 46: ...Notes...