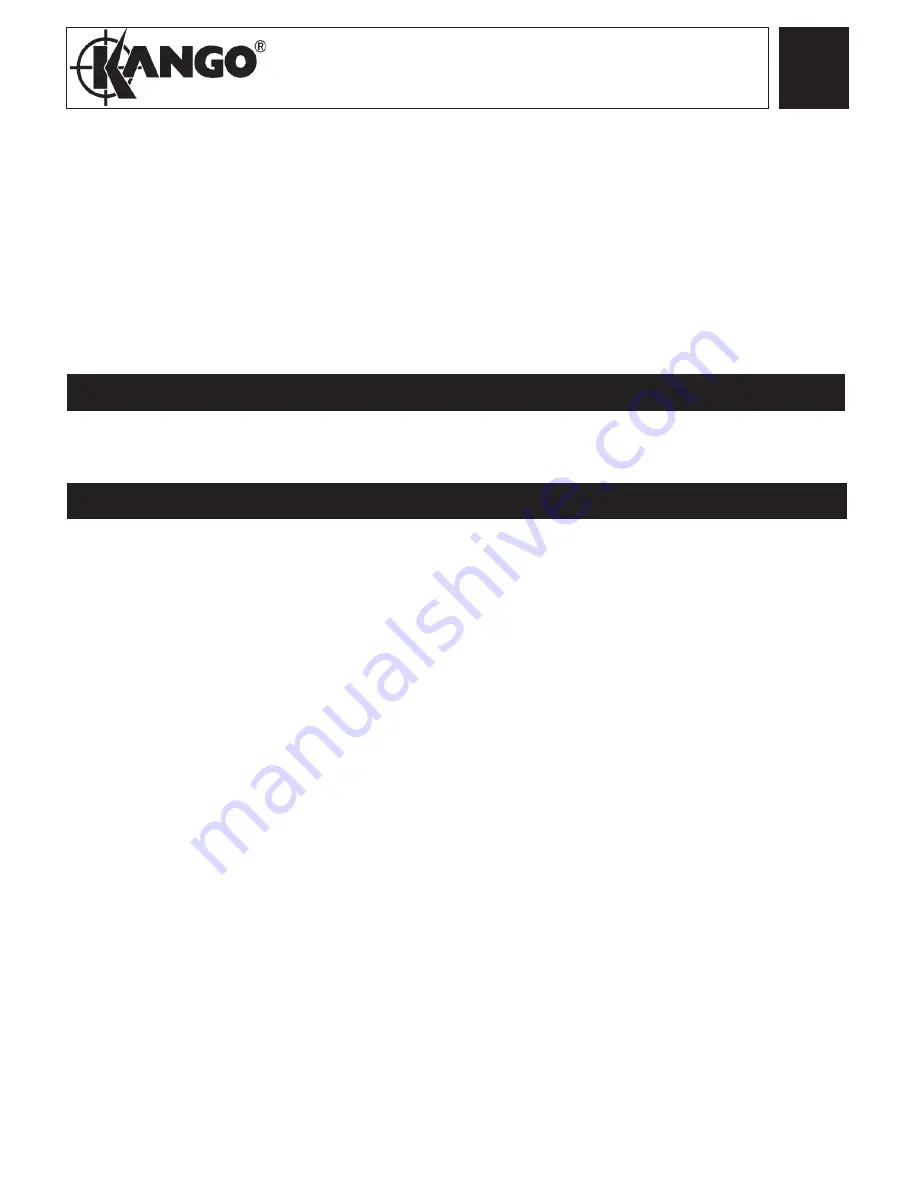
Service and Repair Manual
Model 840S
2
WARRANTY AND LIABILITY STATEMENT
All repairs may be completed with standard workshop tools and equipment.
SERVICE TOOLS
Use only Authorized parts. Any damage or malfunction caused by the use of unauthorized parts
is not covered by Warranty or Product Liability.
General
For best performance hammers should be serviced at regular intervals, any indication that the hammer is not performing as specified
should be investigated to prevent any adverse damage occuring.
ALL SEALS, GASKETS, GREASE OR OTHER PARTS DEEMED NECESSARY FOR SERVICING ARE IN THE SERVICE KIT.
ALL NEEDLE ROLLER BEARINGS SHOULD BE PRESSED WITH THE ROUNDED EDGE ENTERING THE BORE FIRST, AND THE PRESS TOOL
PRESSING AGAINST THE FLAT SURFACE OF THE BEARING.
Cleaning
All mechanical parts with the exception of any sealed bearings should be cleaned in a suitable cleaning fluid. Electrical parts should be
cleaned by the use of compressed air. PRECAUTIONS MUST BE TAKEN FOR PERSONAL SAFETY THE USE OF EYE PROTECTION AND
GLOVES IS RECOMMENDED.
Inspection
All mechanical and electric parts should be inspected for wear and replaced as required.