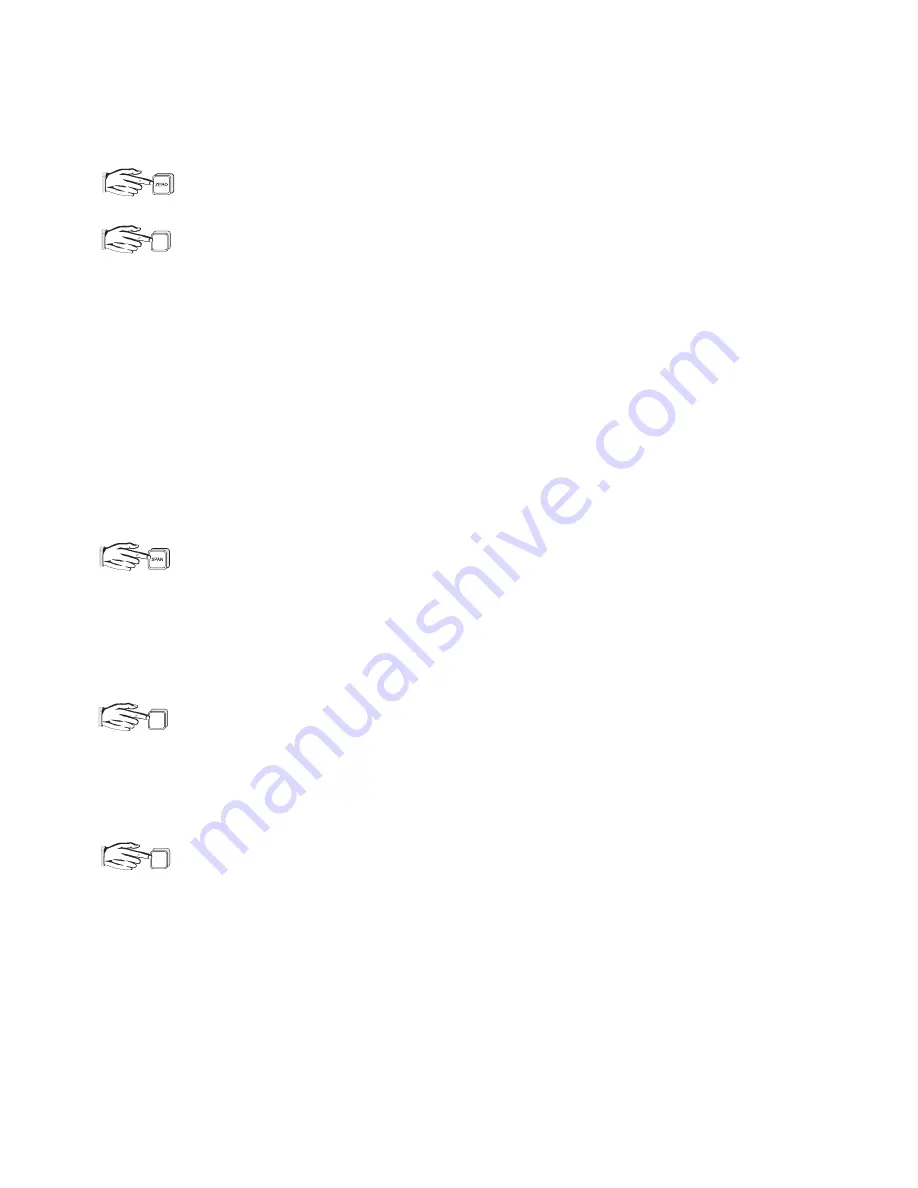
ZERO
The average load applied to the belt scale by the empty running belt is calculated and stored in memory as a
Zero count. After the belt has run empty for sufficient time (15 minutes or more)...
[ZERO] is displayed in the FEATURE field. The current Zero counts are displayed in the
VALUE field. [ENTER: CALIBRATE MODE] is displayed in the AUX 2 field.
to initiate the calibration. [CALIB] is displayed in the CALIB field and [ZERO IN PROGRESS]
is displayed in the AUX 2 field. The time required to complete the calibration is dependent upon
Belt Speed (P4), and Belt Length (P6). Calibration time (and accuracy) is also dependent upon
Calibration Duration. (Refer to Parameters/P30 Calibration Duration.) The number of full belt
revolutions remaining until completion, is displayed in the BELT REV field.
When complete, the deviation from the last Zero calibration is displayed in the
Value field, as a percent of span.
SPAN
The simulated material load provide by the Test Weight (or number of Test Weights) is calculated and stored
in memory as a Span count. (Refer to Alternate Test References, if a Test Weight is not used.)
With the belt running empty, and no Test Weight applied to the belt scale...
[SPAN] is displayed in the FEATURE field. The current Span counts are displayed in the
VALUE field.
With [CALIB] displayed in the CALIB field, apply the Test Weight to the belt scale
(as described in the belt scale manual).
If [CALIB] is not displayed, respond to the CompuScale III display prompts until this
indicator is obtained, before applying the Test Weight.
to initiate the calibration. The time required to complete the calibration is dependent upon
Belt Speed (P4), and Belt Length (P6). Calibration time (and accuracy) is also dependent
upon Calibration Duration. (Refer to Parameters/P30 Calibration Duration.) The number of full
belt revolutions remaining until completion, is displayed in the BELT REV field.
When complete, the deviation from the last Span calibration, is displayed in the VALUE field,
as a percent of span.
to accept the new calibration. Otherwise, investigate the reason for the deviation and
perform the Span calibration again.
CALIBRATION ACCURACY
With the Initial Zero and Initial Span calibration complete, RUN mode operation is possible, however greater
calibration accuracy may be required. The Test Reference value (P7) is an approximation, and may require
adjustment for maximum calibration accuracy to be achieved.
To adjust the Span calibration for maximum accuracy, perform a material test. (Refer to Parameters/P8 Span
Adjust). The Test Reference value (P7) is automatically adjusted so the Test Weight will accurately simulate
material load during future Span calibrations.
The CompuScale III is ready to be put into service, (refer to Operation).
ENTER
ENTER
ENTER
PL-367
6 – 2