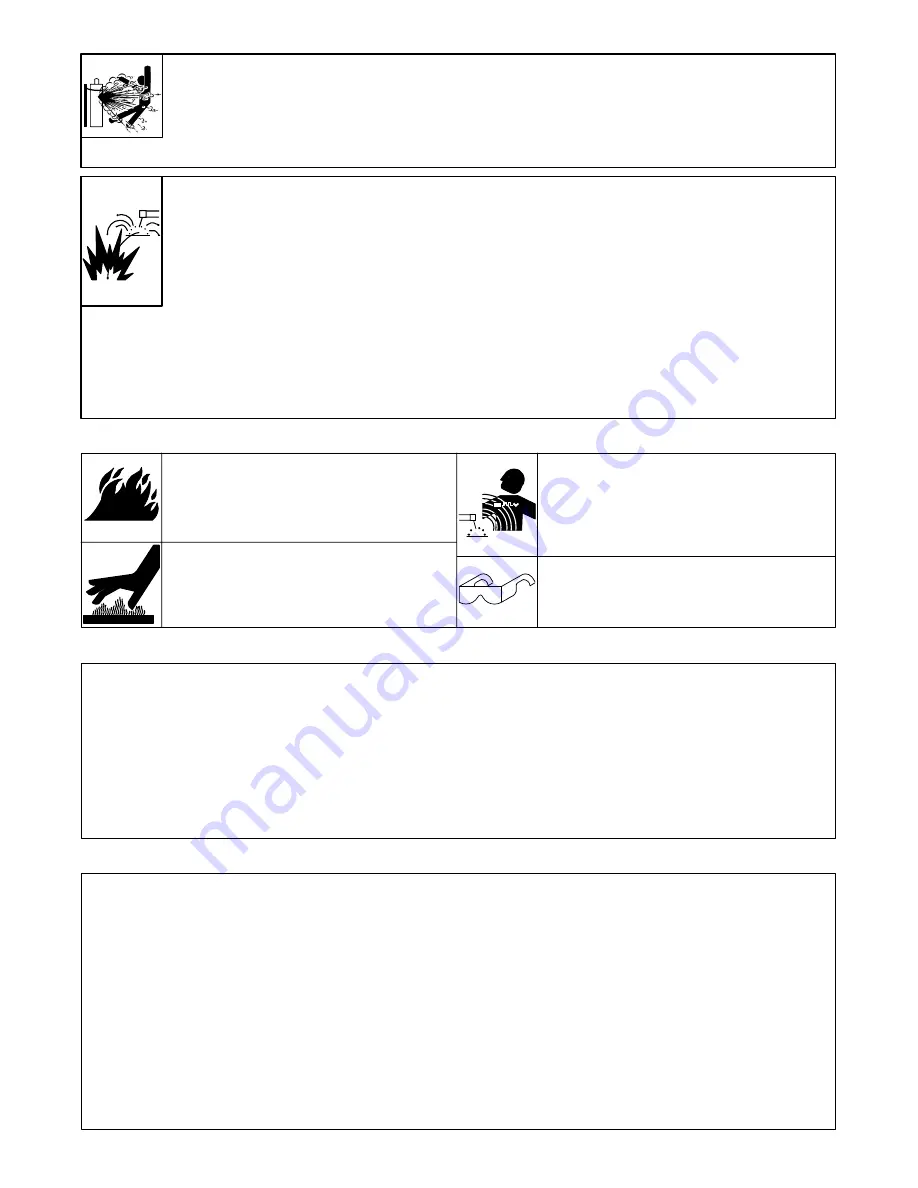
OM-116 Page 2
CYLINDERS can explode if damaged.
Shielding gas cylinders contain gas under high
pressure. If damaged, a cylinder can explode. Since
gas cylinders are normally part of the welding
process, be sure to treat them carefully.
1.
Protect compressed gas cylinders from excessive heat,
mechanical shocks, slag, open flames, sparks, and arcs.
2.
Keep cylinders away from any welding or other electrical circuits.
3.
Never drape an electrode holder over a gas cylinder.
4.
Never allow a welding electrode to touch any cylinder.
5.
Never weld on a pressurized cylinder – explosion will result.
WELDING can cause fire or
explosion.
Welding on closed containers, such as tanks,
drums, or pipes, can cause them to blow up. Sparks
can fly off from the welding arc. The flying sparks,
hot workpiece, and hot equipment can cause fires
and burns. Accidental contact of electrode to metal
objects can cause sparks, explosion, overheating,
or fire. Check and be sure the area is safe before
doing any welding.
1.
Protect yourself and others from flying sparks and hot metal.
2.
Do not weld where flying sparks can strike flammable material.
3.
Remove all flammables within 35 ft (10.7 m) of the welding arc. If
this is not possible, tightly cover them with approved covers.
4.
Be alert that welding sparks and hot materials from welding can
easily go through small cracks and openings to adjacent areas.
5.
Watch for fire, and keep a fire extinguisher nearby.
6.
Be aware that welding on a ceiling, floor, bulkhead, or partition
can cause fire on the hidden side.
7.
Do not weld on closed containers such as tanks, drums, or pipes,
unless they are properly prepared according to AWS F4.1 (see
Safety Standards).
8.
Connect work cable to the work as close to the welding area as
practical to prevent welding current from traveling long, possibly
unknown paths and causing electric shock and fire hazards.
9.
Do not use welder to thaw frozen pipes.
10. Remove stick electrode from holder when not in use.
11. Wear oil-free protective garments such as leather gloves, heavy
shirt, cuffless trousers, high shoes, and a cap.
12. Remove any combustibles, such as a butane lighter or matches,
from your person before doing any welding.
1-3.
Additional Installation, Operation, And Maintenance Hazards
FIRE OR EXPLOSION can result from
placing unit on, over, or near
combustible surfaces.
1.
Do not install unit on, over, or near combustible
surfaces or flammables.
HOT PARTS can cause severe burns.
1.
Do not touch hot parts bare handed. Allow cooling
period before beginning.
MAGNETIC FIELDS FROM HIGH
CURRENTS can affect pacemaker
operation.
1.
Wearers should consult their doctor before going
near arc welding, gouging, or spot welding
operations.
FLYING PIECES OF METAL or DIRT can
injure eyes.
1.
Wear safety glasses with side shields or face
shield.
1-4.
Principal Safety Standards
Safety in Welding and Cutting, ANSI Standard Z49.1, from American
Welding Society, 550 N.W. LeJeune Rd, Miami FL 33126
Safety and Health Standards, OSHA 29 CFR 1910, from
Superintendent of Documents, U.S. Government Printing Office,
Washington, D.C. 20402.
Recommended Safe Practices for the Preparation for Welding and
Cutting of Containers That Have Held Hazardous Substances,
American Welding Society Standard AWS F4.1, from American
Welding Society, 550 N.W. LeJeune Rd, Miami, FL 33126
National Electrical Code, NFPA Standard 70, from National Fire
Protection Association, Batterymarch Park, Quincy, MA 02269.
Code for Safety in Welding and Cutting, CSA Standard W117.2, from
Canadian Standards Association, Standards Sales, 178 Rexdale
Boulevard, Rexdale, Ontario, Canada M9W 1R3.
Safe Practices For Occupation And Educational Eye And Face
Protection, ANSI Standard Z87.1, from American National Standards
Institute, 1430 Broadway, New York, NY 10018.
Cutting And Welding Processes, NFPA Standard 51B, from National
Fire Protection Association, Batterymarch Park, Quincy, MA 02269.
1-5.
EMF Information
Considerations About Welding And The Effects Of Low Frequency
Electric And Magnetic Fields
The following is a quotation from the General Conclusions Section of
the U.S. Congress, Office of Technology Assessment, Biological
Effects of Power Frequency Electric & Magnetic Fields – Background
Paper, OTA-BP-E-53 (Washington, DC: U.S. Government Printing
Office, May 1989): “. . . there is now a very large volume of scientific
findings based on experiments at the cellular level and from studies
with animals and people which clearly establish that low frequency
magnetic fields can interact with, and produce changes in, biological
systems. While most of this work is of very high quality, the results are
complex. Current scientific understanding does not yet allow us to
interpret the evidence in a single coherent framework. Even more
frustrating, it does not yet allow us to draw definite conclusions about
questions of possible risk or to offer clear science-based advice on
strategies to minimize or avoid potential risks.”
To reduce magnetic fields in the workplace, use the following
procedures:
1.
Keep cables close together by twisting or taping them.
2.
Arrange cables to one side and away from the operator.
3.
Do not coil or drape cables around the body.
4.
Keep welding power source and cables as far away as
practical.
5.
Connect work clamp to workpiece as close to the weld as
possible.
About Pacemakers:
The above procedures are also recommended for pacemaker
wearers. Consult your doctor for complete information.