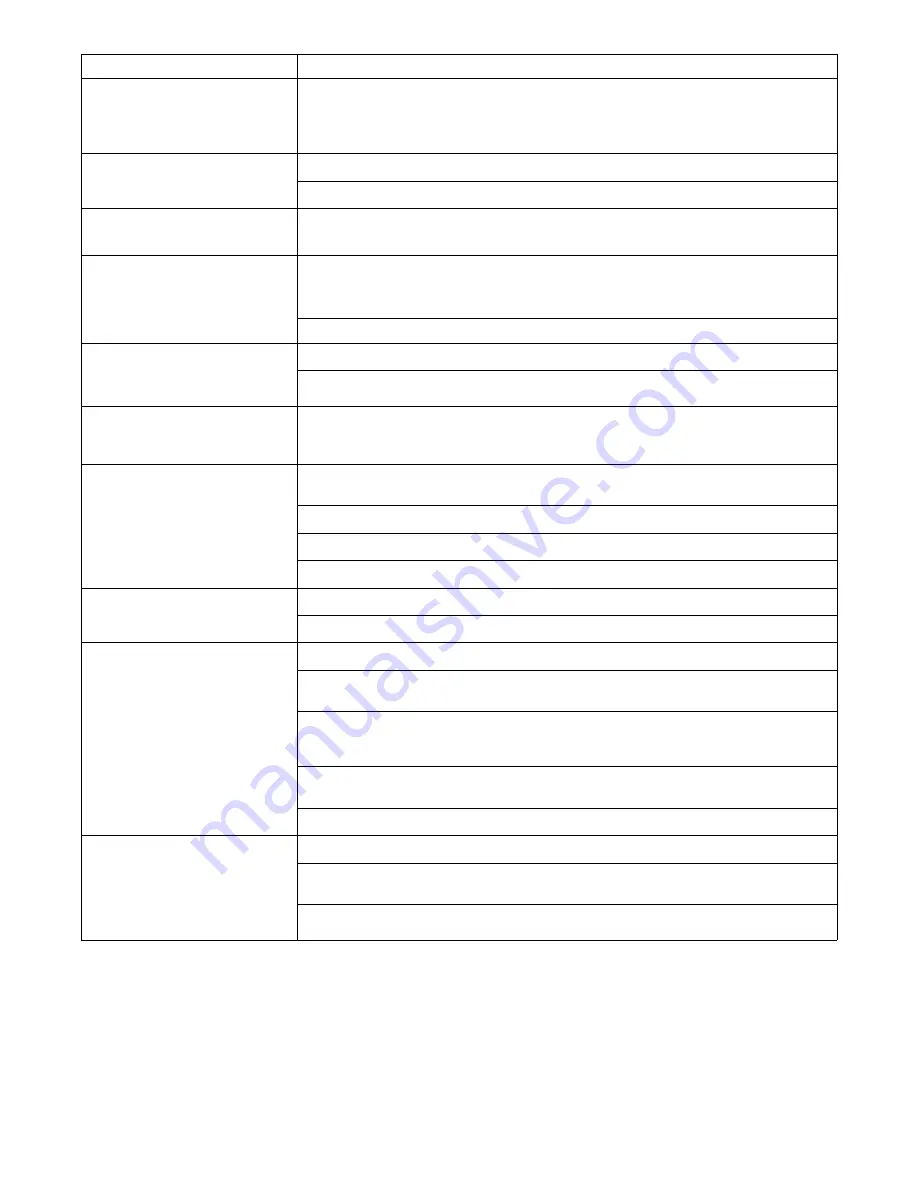
OM-267043 Page 27
Trouble
Remedy
Gun trigger is pressed, gas does not
flow, wire is not energized, wire feeds.
If a welding arc is not established in 3 seconds after the gun trigger is activated, the unit will feed wire
without energizing the contactor or gas valve. The unit will feed approximately 35 feet (10.7 meters) of
wire, then stop feeding. This is to prevent complete despoolling of the wire, as in the case of a damaged
gun.
Display on Meter Board PC22 does not
light.
Have Factory Authorized Service Agent check Control board PC1.
Replace Meter Board PC22.
Segments on Meter Board PC22 are
missing.
Replace Meter Board PC22.
Weld voltage on Meter Board PC22 is
not accurate.
Weld voltage on Meter Board PC22 will show weld voltage at the feeder. Due to voltage drops in the weld
cables, weld voltage at the feeder will not match weld voltage at the welding power source. Due to aver-
aging of weld voltage, if weld time is less than 8 seconds the displayed weld voltage at the feeder may
not be accurate.
Check Motor Control PC1 and connections, replace if necessary.
While not welding
−
Voltage display al-
ternates between three dashes and
open circuit voltage.
This is normal when unit is connected to a Non
−
WCC compatible power source (see Section 6-1).
Unit is connected to but not associated to a WCC control or WCC compatible power source
(see Section 5-3).
While not welding
−
Voltage display
alternates between CC and open circuit
voltage.
This is normal when the CC/CV switch is set to CC mode (see Section 6-1).
Weld amperage on Meter Board PC22 is
not accurate.
Amperage displayed at feeder is approximate. Refer to power source for actual amperage
(see Section 5-12)
Check DIP switch settings on Meter Board PC22 (see Section 5-12).
Check transducer HD1 and connections, and replace if necessary.
Check Motor Control PC1 and connections, replace if necessary.
Software and weld time information on
Meter Board PC22 is not accurate.
Check DIP switch settings on Meter Board PC22 (see Section 5-12).
Check Motor Control PC1 and connections, replace if necessary.
When associated to a WCC control or
WCC compatible power source
−
Voltage displayed on feeder does not
match voltage on power source.
Preset voltages between the feeder and welding power source should be within 0.5 volt of each other.
When associated to a WCC control, verify that the WCC control is configured properly
(see WCC control owner’s manual).
While welding the voltage displayed at the feeder is the weld voltage at the feeder. The voltage displayed
at the power source is the weld voltage at the power source. These two voltages will not match due to
voltage drops in the weld cables.
Due to averaging of the weld voltage, if weld time is less than 8 seconds the displayed weld voltage at
the feeder may not be accurate.
Check Motor Control PC1 and connections, replace if necessary.
Feeder will not associate to a WCC con-
trol or WCC compatible power source.
Follow equipment setup procedure (see Section 5-4).
CC/CV switch must be set to CV to associate to WCC control or WCC compatible power source
(see Section 6-1)
Ensure that the WCC compatible power source Mode Switch is set to V
−
SENSE FEEDER
(see Section 5-4).