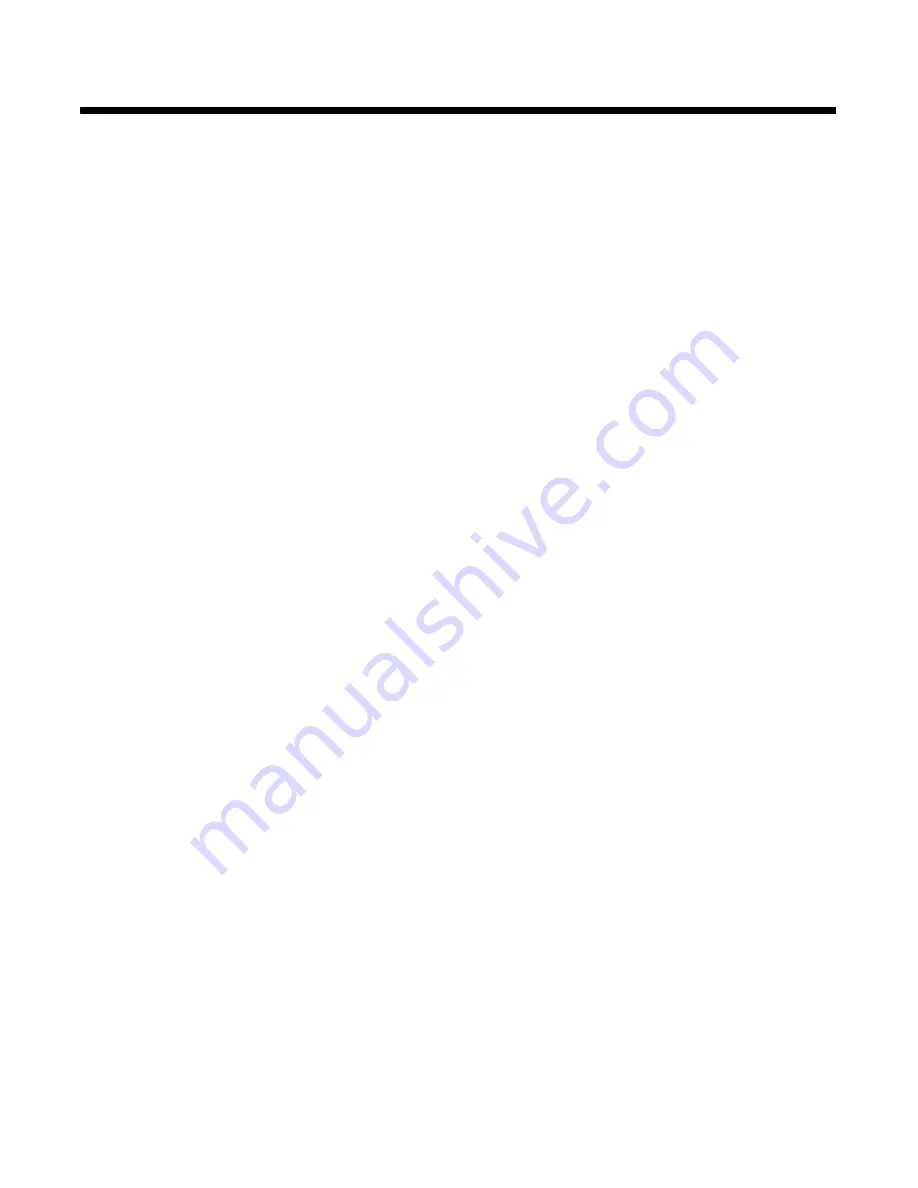
OM-240 113 Page 41
SECTION 11
−
HYDRAULIC SYSTEM PREPARATION
(MODELS WITH HYDRAULIC POWER SOURCE)
11-1. Hydraulic System Integration
A. General Information
−
Minimum Requirements
The system recommendations are intended for operating a crane of a low duty cycle, such as used on a mechanics truck. The system recommenda-
tions are based on intermittent use. Auxiliary tools or operations that need continuous or high duty cycle operation will require additional cooling
capacity.
For use with a mechanics truck crane, the system should at a minimum include the following items:
1
Reservoir of 20 gal (76 L) or more capacity
2
Pressure relief valve
3
Properly sized hoses and fittings, restrained and protected
4
Return line filter to maintain an ISO 4406:1999 Cleanliness Code of 18/16/13.
B. Reservoir
Minimum reservoir size is 20 gal (76 L) with a minimum fluid height of 24 in. ( 610 mm) above base of unit. To accommodate changes in volume due to
cylinder displacement, a filtered breather must be used and vented to atmosphere. This filter should be 10 micron.
The design of the reservoir must allow for adequate oil circulation to disperse entrapped air and to maintain sufficient cooling through the use of baffles.
Changes in oil volume due to cylinder displacement also needs to be accounted for by allowing adequate air space inside the reservoir. The unit must
operate properly at up to a 15
°
angle.
Place reservoir as near as possible to the unit, see Section 10-2. Suction line length greater than 72 in. (1829 mm) is NOT recommended.
The suction port should be at least 3 in. (76 mm) above the bottom of the reservoir to prevent any debris on the bottom of the reservoir from being drawn
into the suction line. Also, the suction port should be at least 6 in. (152 mm) below the top level of the fluid to prevent vortexing. Oil volume changes
during operation and the 15
°
maximum operating angle must be considered.
A suction strainer is not recommended by the hydraulic pump manufacturer. If a suction strainer is used, diligent preventive maintenance is required to
prevent the strainer from clogging.
System return lines and drain lines should terminate below the minimum fluid level to prevent aeration of the oil. Return lines should be located away
from the suction line to prevent interaction.
Allowance for a properly sized immersion heater may be necessary in some climates.
C. Pressure Relief Valve
.
With the use of a pressure compensated pump, the use of a relief valve is recommended in the main circuit to suppress hydraulic shock loads
and add additional system protection.
Open
−
Centered Systems:
The system relief valve should be set according to the crane manufacturer’s recommendations. The maximum pressure of the pump should be set 200
psi (1.38 MPa) above the system relief valve to prevent interaction. For settings above 3800 psi (26.2 MPa), consult the factory.
In this configuration, the system relief valve is the primary relief and the pump maximum pressure setting is secondary.
Closed
−
Centered Systems:
For most closed
−
centered systems, the pump maximum pressure setting is the primary relief and the system relief valve is secondary. Therefore, the
pump maximum pressure setting should be set at a level recommended by the crane manufacturer. The system relief valve should also be set accord-
ing to the crane manufacturer’s recommendations. In general, this will be approximately 200 psi (1.38 MPa) greater than the pump maximum pressure
setting.
D. Hoses And Fittings
All hoses should be sized appropriately according to flow capacity and pressure loss. See Table 11-1 as a guide. Higher system pressures may require
higher pressure hoses.
For the suction line, use sweep elbows to prevent fluid turbulence and reduce the possibility of cavitation at the pump inlet.
Use of quick disconnects in any line is not recommended. Using quick disconnects will cause higher system losses, result in elevated fluid temperature,
and reduced system performance.