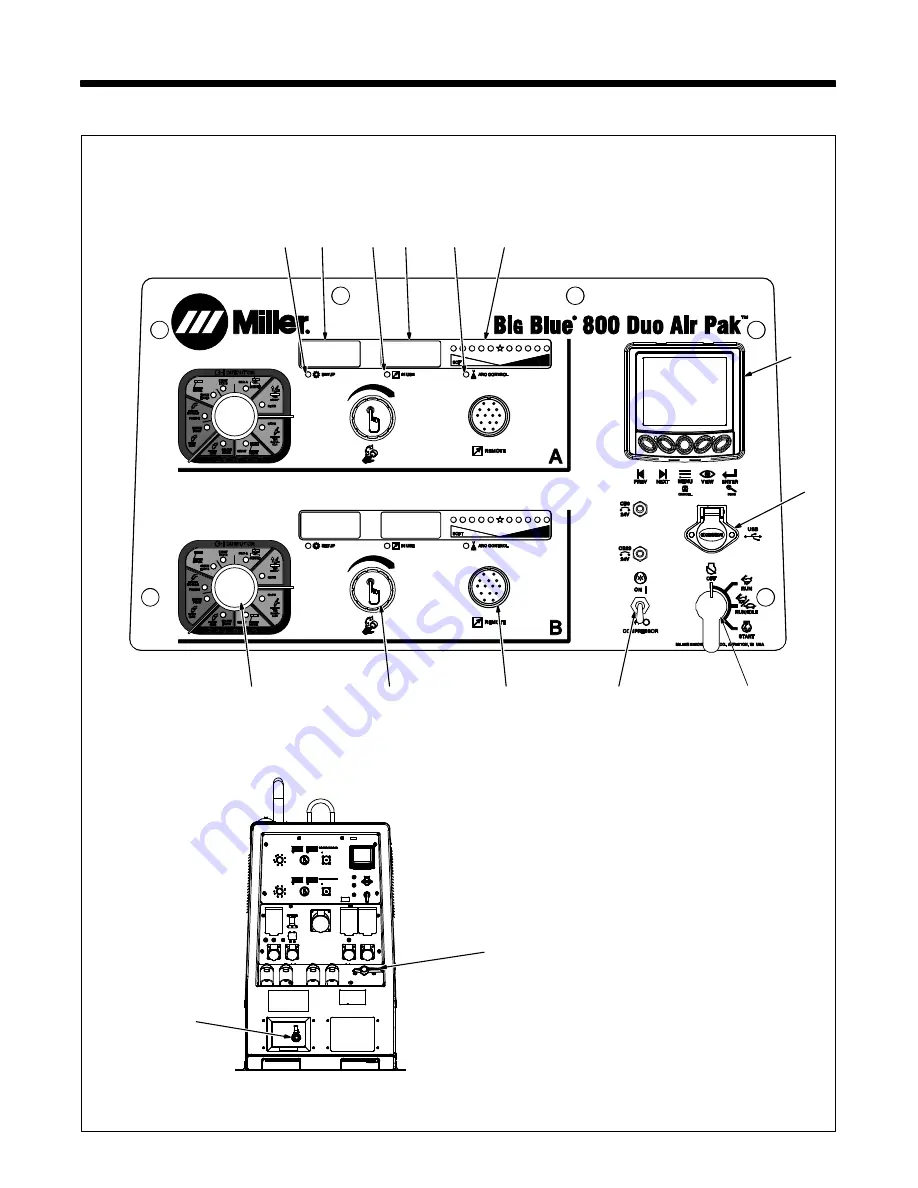
Complete Parts List available at www.MillerWelds.com
OM-282374 Page 38
SECTION 6
−
OPERATING WELDER/GENERATOR
6-1. Front Panel Controls (See Section 6-2)
13
15
907763 / 277078
1
2
5
4
6
7
8
9
3
11
12
10
14
Complete Parts List available at www.MillerWelds.com
OM-282374 Page 38
SECTION 6
−
OPERATING WELDER/GENERATOR
6-1. Front Panel Controls (See Section 6-2)
13
15
907763 / 277078
1
2
5
4
6
7
8
9
3
11
12
10
14