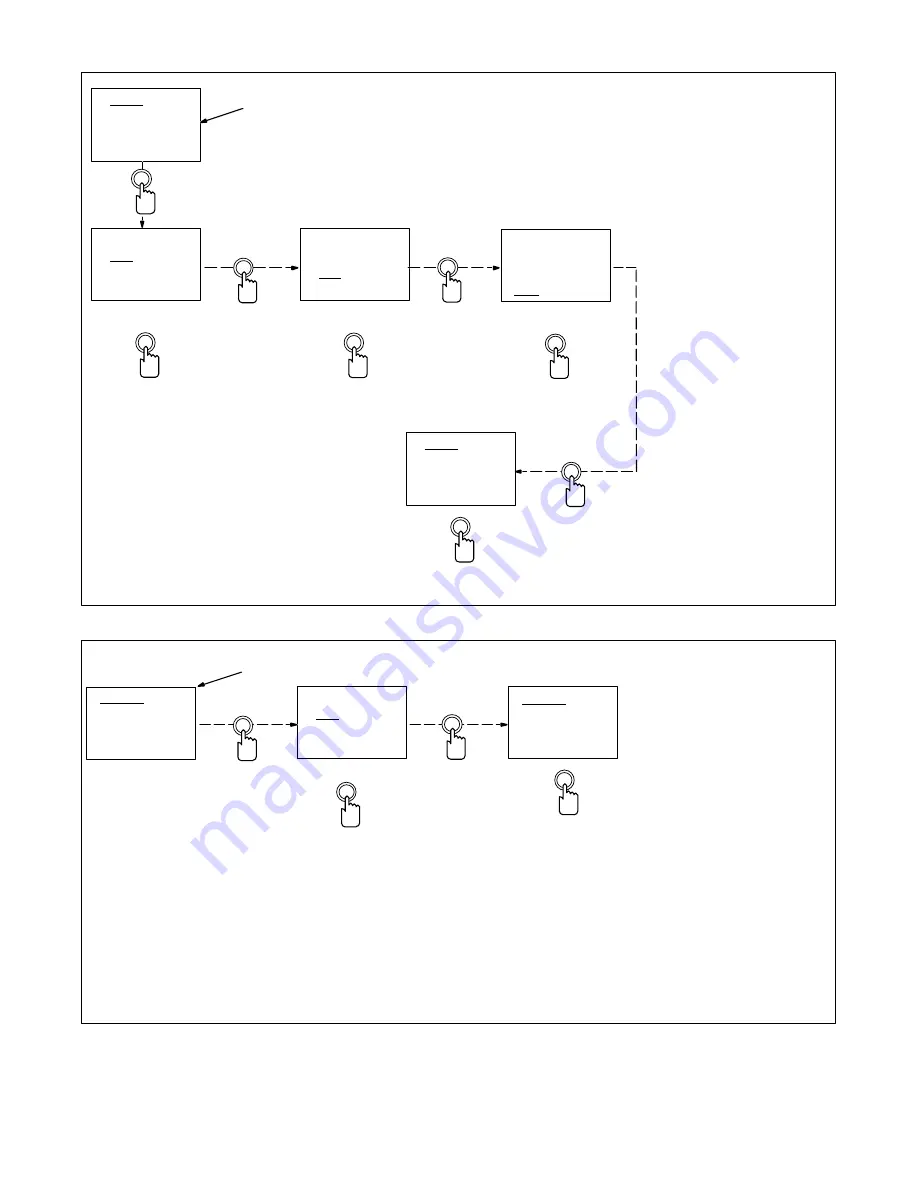
OM-196 188 Page 46
1
Crater Parameters Display
Parameter ranges are as follows:
Seconds, 0-2.50 Sec. If value set is
zero (0), there is no Crater
sequence.
Volts, 10.0-38.0 Volts.
Wire Feed Speed, 50 to 780 inches
per minute, IPM.
Go to Section 8-7.
> Crater
0.02 Sec
24.0 Volt
90 IPM
Crater
0.12 Sec
> 18.0 Volt
90 IPM
Crater
0.12 Sec
18.0 Volt
> 200 IPM
Crater
> 0.12 Sec
24.0 Volt
90 IPM
> Crater
0.12 Sec
18.0 Volt
200 IPM
1
8-6.
Setting Crater Sequence Display
Set Desired Time
Parameter
Select
Increase/
Decrease
Increase
Proceed to next Section.
Parameter
Select
Parameter
Select
Set Desired
Voltage
Increase/
Decrease
Parameter
Select
Set Desired Wire
Feed Speed
Increase/
Decrease
1
Retract Parameter Display
Parameter range is as follows:
Seconds, 0-1.00 seconds. If value
set is zero (0), there is no Burnback
sequence.
Go to Section 8-8.
1
> Retract
0.00 Sec
Retract
> 0.12 Sec
> Retract
0.12 Sec
8-7.
Setting Retract Sequence Display
Set Desired Time
Increase
Proceed to next Section.
Parameter
Select
Parameter
Select
Increase/
Decrease
Summary of Contents for Auto Invision 2
Page 87: ...OM 196 188 Page 81 Notes...
Page 89: ...OM 196 188 Page 83 203 505...
Page 90: ...OM 196 188 Page 84 Figure 14 2 Circuit Diagram For Control Board PC1 Part 1 of 3...
Page 91: ...OM 196 188 Page 85 188 814 1 of 3...
Page 92: ...OM 196 188 Page 86 Figure 14 3 Circuit Diagram For Control Board PC1 Part 2 of 3...
Page 93: ...OM 196 188 Page 87 188 814 2 of 3...
Page 94: ...OM 196 188 Page 88 Figure 14 4 Circuit Diagram For Control Board PC1 Part 3 of 3...
Page 95: ...OM 196 188 Page 89 188 814 3 of 3...
Page 96: ...OM 196 188 Page 90 Figure 14 5 Circuit Diagram For Function Meter Board PC3...
Page 97: ...OM 196 188 Page 91 190 696...
Page 99: ...OM 196 188 Page 93 Notes...
Page 100: ...OM 196 188 Page 94 Figure 13 8 Circuit Diagram For Interface Module...
Page 101: ...OM 196 188 Page 95 193 709...
Page 102: ...OM 196 188 Page 96 Figure 13 9 Circuit Diagram For Microprocessor Board PC11...
Page 103: ...OM 196 188 Page 97 191 838...
Page 104: ...OM 196 188 Page 98 Figure 13 10 Circuit Diagram For Motor Board PC13...
Page 105: ...OM 196 188 Page 99 177 289 A...
Page 106: ...OM 196 188 Page 100 Figure 13 11 Circuit Diagram For Switch Board PC15 182 996...
Page 107: ...OM 196 188 Page 101 200 739 Figure 13 12 Circuit Diagram For Junction Board PC16...
Page 108: ...OM 196 188 Page 102 Figure 13 13 Circuit Diagram For Interface Board PC12 Part 1 of 2...
Page 109: ...OM 196 188 Page 103 191 843 A Part 1 of 2...
Page 110: ...OM 196 188 Page 104 Figure 13 14 Circuit Diagram For Interface Board PC12 Part 2 of 2...
Page 111: ...OM 196 188 Page 105 191 843 A Part 2 of 2...
Page 112: ...OM 196 188 Page 106 Figure 13 15 Circuit Diagram For Customer Interface Board PC14 Part 1 of 3...
Page 113: ...OM 196 188 Page 107 Pensar 86147s03 Part 1 of 3...
Page 114: ...OM 196 188 Page 108 Figure 13 16 Circuit Diagram For Customer Interface Board PC14 Part 2 of 3...
Page 115: ...OM 196 188 Page 109 Pensar 86147s03 Part 2 of 3...
Page 116: ...OM 196 188 Page 110 Figure 13 17 Circuit Diagram For Customer Interface Board PC14 Part 3 of 3...
Page 117: ...OM 196 188 Page 111 Pensar 86147s03 Part 3 of 3...
Page 118: ...OM 196 188 Page 112 Figure 13 18 Circuit Diagram For Touch Sensor Board PC18 174 578 A...
Page 119: ...OM 196 188 Page 113 200 739 A Figure 13 19 Circuit Diagram For Setup Pendant...
Page 121: ...OM 196 188 Page 115 Notes...
Page 126: ...OM 196 188 Page 120 Notes...