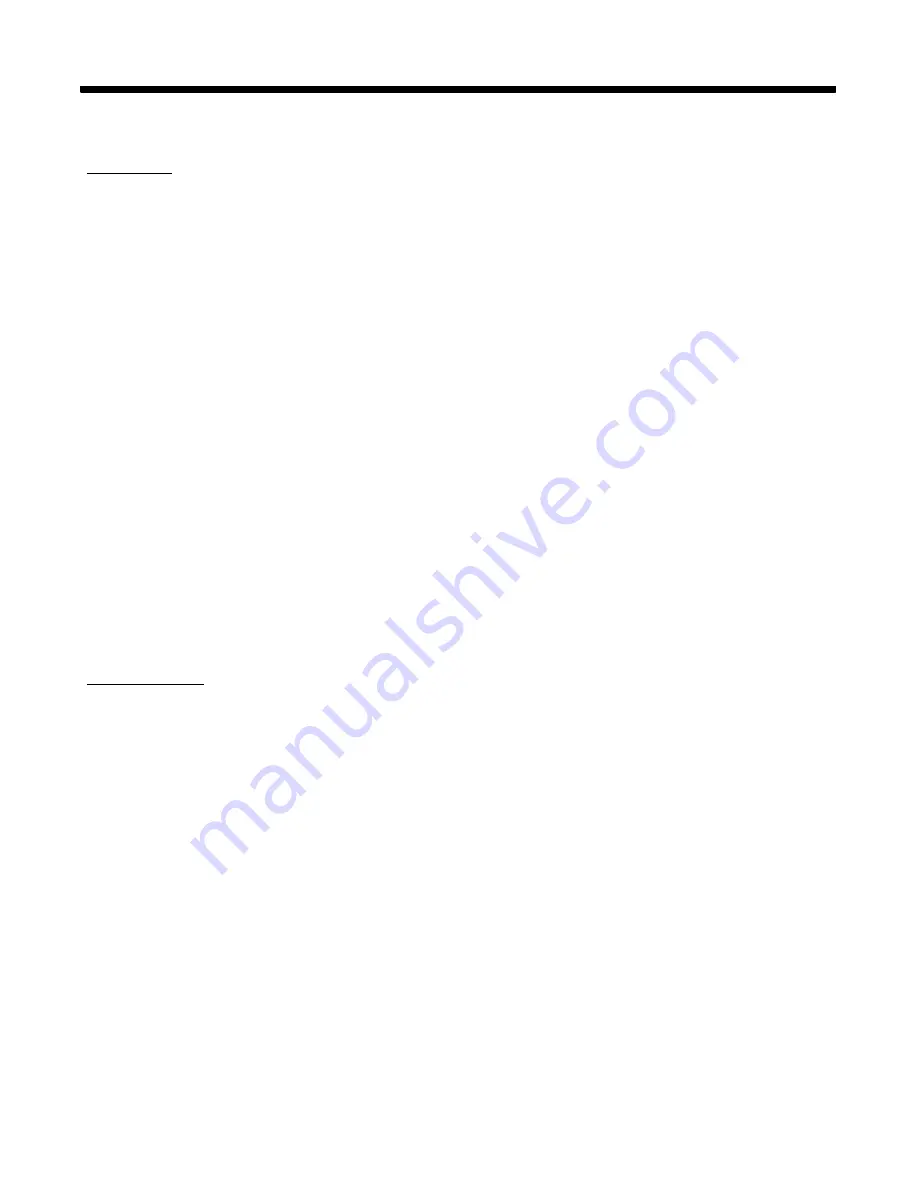
OM-196 188 Page 19
SECTION 4 – OPERATION
4-1.
Operational Terms
The following is a list of terms and their definitions as they apply to this interface unit:
General Terms:
Adaptive Pulse Welding
When the “adaptive pulse” welding process is selected, the unit will attempt to automatically regulate
pulse frequency in order to maintain a constant arc length, regardless of change in welding wire stick-
out.
Abk (Background Amperage)
Abk is the low weld current. Background current preheats welding wire and maintains the arc. When
background current is too low, the arc is unstable and hard to maintain.
Apk (Peak Amperage)
Apk is the high pulse of welding current. Peak current melts the welding wire and forms a droplet. The
droplet is forced into the weld puddle.
Vpk (Peak Voltage)
Arc voltage during peak current phase of the pulse waveform. This determines arc length during
adaptive pulse welding.
Inductance
In short circuit GMAW welding, an increase in inductance will decrease the number of short circuit
metal transfers per second (provided no other changes are made) and increase the arc-on time. The
increased arc-on time makes the pool more fluid.
PPS (Pulses Per Second)
PPS, pulse rate, and frequency (Hz) are used interchangeably. A PPS or pulse rate of 60 Hz means
60 pulses of current are produced each second.
PWms (Pulse Width in Milliseconds)
PWms is the time spent at peak current (1.2 ms is .0012 seconds). This time must be long enough to
form a droplet of welding wire. The stiffness or fluidity of the molten weld puddle is controlled by
PWms.
Synergic
Synergic refers to the unit’s ability to use preprogrammed pulse parameters to determine the actual
pulse settings of Peak Amperage, Background Amperage, Pulse Frequency and Pulse Width at any
specific wire feed speed setting.
Trim
Term used to represent arc length adjustments in pulse programs. Increasing trim increases the ac-
tual arc length. Likewise, decreasing trim shortens arc length. Trim is replaced by volts in MIG pro-
grams.
Setup Pendant Terms:
Card Mode
Is used to select use of the optional data card storage and retrieval capabilities.
Process Mode
Is used to select the type of process to be used, including Pulse, Adaptive Pulse, or Mig.
Sequence Mode
Is used to select and program the weld sequences which include preflow, run-in, weld, crater,
burnback, and postflow.
Setup Screen Terms:
Access Code
NOTE: The optional Data Card is required to activate this feature. With code off, access to the setup
displays is not restricted. With code on, the operator must know and enter the access code to access
or change any of the setup displays.
To use code, press Parameter Select button to enter access code. When the correct letter is entered,
the indicator automatically moves to the next character. When the final access code letter is entered,
the display automatically changes to the initial setup display.
Arc Start
NOTE: Do not use the Hot Start setting for .035 in (9 mm) or smaller wire. Use the Hot Start mode for
pulse welding with 450 Ampere Inverter Model when high initial weld current is necessary to start
large diameter welding wires. When in Hot Start, the 450 Ampere Inverter Model starts the arc in the
CV mode and switches to CC once the arc is started. Do not use Hot Start unless using 450 Ampere
Inverter Model.
Arc Time
Allows actual arc time up to 9,999.99 hours and weld cycles up to 999,999 to be accumulated and
displayed on the digital display, and can be reset to zero as required.
Mig Type (Voltage
Correction)
With DVC Voltage Correction On, the unit uses closed-loop control based on voltage feedback to
maintain set voltage parameters. With DVC Voltage Correction Off, feedback from the arc is not used
for closed-loop feedback to maintain voltage parameters. Feedback from the arc is still used for other
functions.
Name Feature
When using the optional Data Card and turning the name feature on, programs written to the card can
be identified by name, number, job number, etc.
Program Reset
By selecting program reset in the memory reset mode, the unit defaults to original factory program
settings for the program last active. All other program and setup information remains the same.
Range
The interface requires that the voltage and amperage range of the welding power source be entered.
Obtain this information from the welding power source Owner’s Manual.
Security
NOTE: The optional Data Card is required to activate this feature. Is used to limit what the operator
can control. This includes accessing the number of the program, 1 through 8, and the range of weld-
ing parameters within the program.
Software Screen
Selection of this function will display the software version of the unit. When talking with factory service
personnel, this number may be required.
Summary of Contents for Auto Invision 2
Page 87: ...OM 196 188 Page 81 Notes...
Page 89: ...OM 196 188 Page 83 203 505...
Page 90: ...OM 196 188 Page 84 Figure 14 2 Circuit Diagram For Control Board PC1 Part 1 of 3...
Page 91: ...OM 196 188 Page 85 188 814 1 of 3...
Page 92: ...OM 196 188 Page 86 Figure 14 3 Circuit Diagram For Control Board PC1 Part 2 of 3...
Page 93: ...OM 196 188 Page 87 188 814 2 of 3...
Page 94: ...OM 196 188 Page 88 Figure 14 4 Circuit Diagram For Control Board PC1 Part 3 of 3...
Page 95: ...OM 196 188 Page 89 188 814 3 of 3...
Page 96: ...OM 196 188 Page 90 Figure 14 5 Circuit Diagram For Function Meter Board PC3...
Page 97: ...OM 196 188 Page 91 190 696...
Page 99: ...OM 196 188 Page 93 Notes...
Page 100: ...OM 196 188 Page 94 Figure 13 8 Circuit Diagram For Interface Module...
Page 101: ...OM 196 188 Page 95 193 709...
Page 102: ...OM 196 188 Page 96 Figure 13 9 Circuit Diagram For Microprocessor Board PC11...
Page 103: ...OM 196 188 Page 97 191 838...
Page 104: ...OM 196 188 Page 98 Figure 13 10 Circuit Diagram For Motor Board PC13...
Page 105: ...OM 196 188 Page 99 177 289 A...
Page 106: ...OM 196 188 Page 100 Figure 13 11 Circuit Diagram For Switch Board PC15 182 996...
Page 107: ...OM 196 188 Page 101 200 739 Figure 13 12 Circuit Diagram For Junction Board PC16...
Page 108: ...OM 196 188 Page 102 Figure 13 13 Circuit Diagram For Interface Board PC12 Part 1 of 2...
Page 109: ...OM 196 188 Page 103 191 843 A Part 1 of 2...
Page 110: ...OM 196 188 Page 104 Figure 13 14 Circuit Diagram For Interface Board PC12 Part 2 of 2...
Page 111: ...OM 196 188 Page 105 191 843 A Part 2 of 2...
Page 112: ...OM 196 188 Page 106 Figure 13 15 Circuit Diagram For Customer Interface Board PC14 Part 1 of 3...
Page 113: ...OM 196 188 Page 107 Pensar 86147s03 Part 1 of 3...
Page 114: ...OM 196 188 Page 108 Figure 13 16 Circuit Diagram For Customer Interface Board PC14 Part 2 of 3...
Page 115: ...OM 196 188 Page 109 Pensar 86147s03 Part 2 of 3...
Page 116: ...OM 196 188 Page 110 Figure 13 17 Circuit Diagram For Customer Interface Board PC14 Part 3 of 3...
Page 117: ...OM 196 188 Page 111 Pensar 86147s03 Part 3 of 3...
Page 118: ...OM 196 188 Page 112 Figure 13 18 Circuit Diagram For Touch Sensor Board PC18 174 578 A...
Page 119: ...OM 196 188 Page 113 200 739 A Figure 13 19 Circuit Diagram For Setup Pendant...
Page 121: ...OM 196 188 Page 115 Notes...
Page 126: ...OM 196 188 Page 120 Notes...