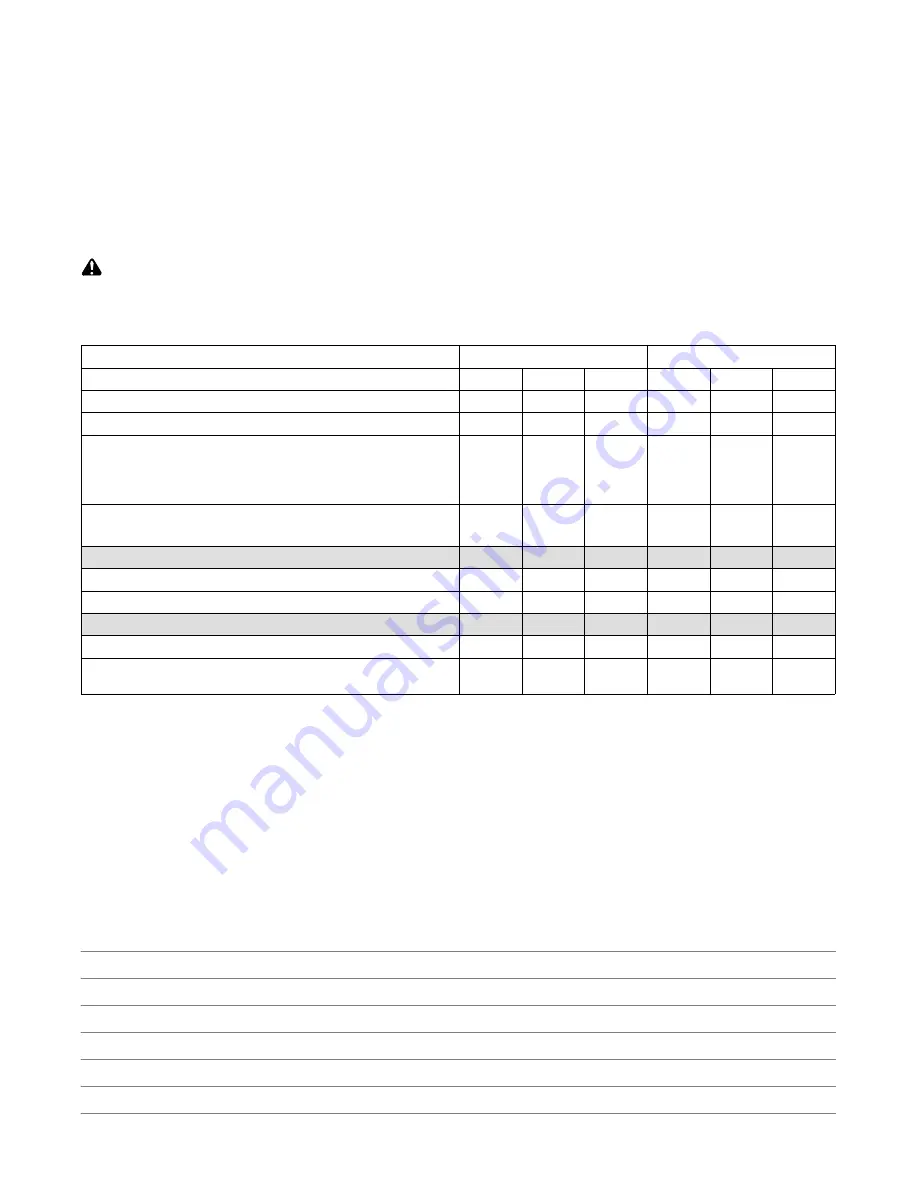
.
A complete Parts List is available at www.MillerWelds.com
OM-254915 Page 22
5-11. Electrical Service Guide
Elec Serv 2014
−
01
NOTICE
−
INCORRECT INPUT POWER can damage this welding power source. This welding power source requires a CONTINUOUS supply of
input power at rated frequency
(+
10%) and voltage
(+
10%). Phase to ground voltage shall not 10% of rated input voltage. Do not use a genera-
tor with automatic idle device (that idles engine when no load is sensed) to supply input power to this welding power source.
NOTICE
−
Actual input voltage should not be 10% less than minimum and/or 10% more than maximum input voltages listed in table. If actual input
voltage is outside this range, output may not be be available.
Failure to follow these electrical service guide recommendations could create an electric shock or fire hazard. These
recommendations are for a dedicated circuit sized for the rated output and duty cycle of the welding power source.
In dedicated circuit installations, the National Electrical Code (NEC) allows the receptacle or conductor rating to be less than the rating
of the circuit protection device. All components of the circuit must be physically compatible. See NEC articles 210.21, 630.11, and
630.12.
60 Hz 1-Phase
60 Hz 3-Phase
Rated Supply Voltage (V)
200
230
460
200
230
460
Rated Maximum Supply Current
I
1max
(A)
69.0
61.0
30.0
34.0
30.0
15.0
Maximum Effective Supply Current
I
1eff
(A)
53.5
47.3
23.2
26.3
23.2
11.6
Maximum Recommended Standard Fuse Rating In Amperes
1
70
90
35
45
Time-Delay Fuses
2
80
35
40
15
Normal Operating Fuses
3
100
45
50
20
Maximum Recommended Supply Conductor Length
In Feet (Meters)
4
96
(29)
81
(25)
217
(66)
85
(26)
111
(34)
172
(53)
Raceway Installation
Minimum Supply Conductor Size In AWG (mm
2
)
5
6 (16)
8 (10)
10 (6)
10 (6)
10 (6)
14 (2.5)
Minimum Grounding Conductor Size In AWG (mm
2)
5
8 (10)
8 (10)
10 (6)
10 (6)
10 (6)
14 (2.5)
Flexible Cord Installation
Minimum Supply Conductor Size In AWG (mm
2
)
6
6 (16)
6 (16)
12 (4)
8 (10)
10 (6)
14 (2.5)
Recommended Strain Relief
7
See
Parts List
See
Parts List
See
Parts List
See
Parts List
See
Parts List
See
Parts List
Reference: 2020 National Electrical Code (NEC) (including article 630)
1 If a circuit breaker is used in place of a fuse, choose a circuit breaker with time-current curves comparable to the recommended fuse.
2 “Time-Delay” fuses are UL class “RK5” . See UL 248.
3 “Normal Operating” (general purpose - no intentional delay) fuses are UL class “K5” (up to and including 60 amps), and UL class “H” ( 65 amps and
above).
4 Maximum total length of copper input conductors in entire installation, raceway and/or flexible cord.
5 Raceway conductor data in this section specifies conductor size (excluding flexible cord or cable) between the panelboard and the equipment per
NEC Table 310.15(B)(16) and is based on allowable ampacities of insulated copper conductors having a temperature rating of 75
°
C (167
°
F) with not
more than three single current
−
carrying conductors in a raceway.
6 Flexible cord conductor size is based on NEC Table 400.5(A)(1) for SOOW 600V 90
°
C (194
°
F) jacketed cable in a 30
°
C (86
°
F) ambient temperature.
See NEC Table 310.15(B)(2)(a) for ambient temperature correction factors. Flexible cord used for connection to the power supply system shall com-
ply with the requirements of CSA C22.2 No. 49.
7 If necessary, have a qualified person enlarge access hole in machine panel to accommodate strain relief.
Notes
Summary of Contents for Millermatic 350P
Page 63: ...OM 254915 Page 59 Notes...
Page 65: ...OM 254915 Page 61 255730 J...