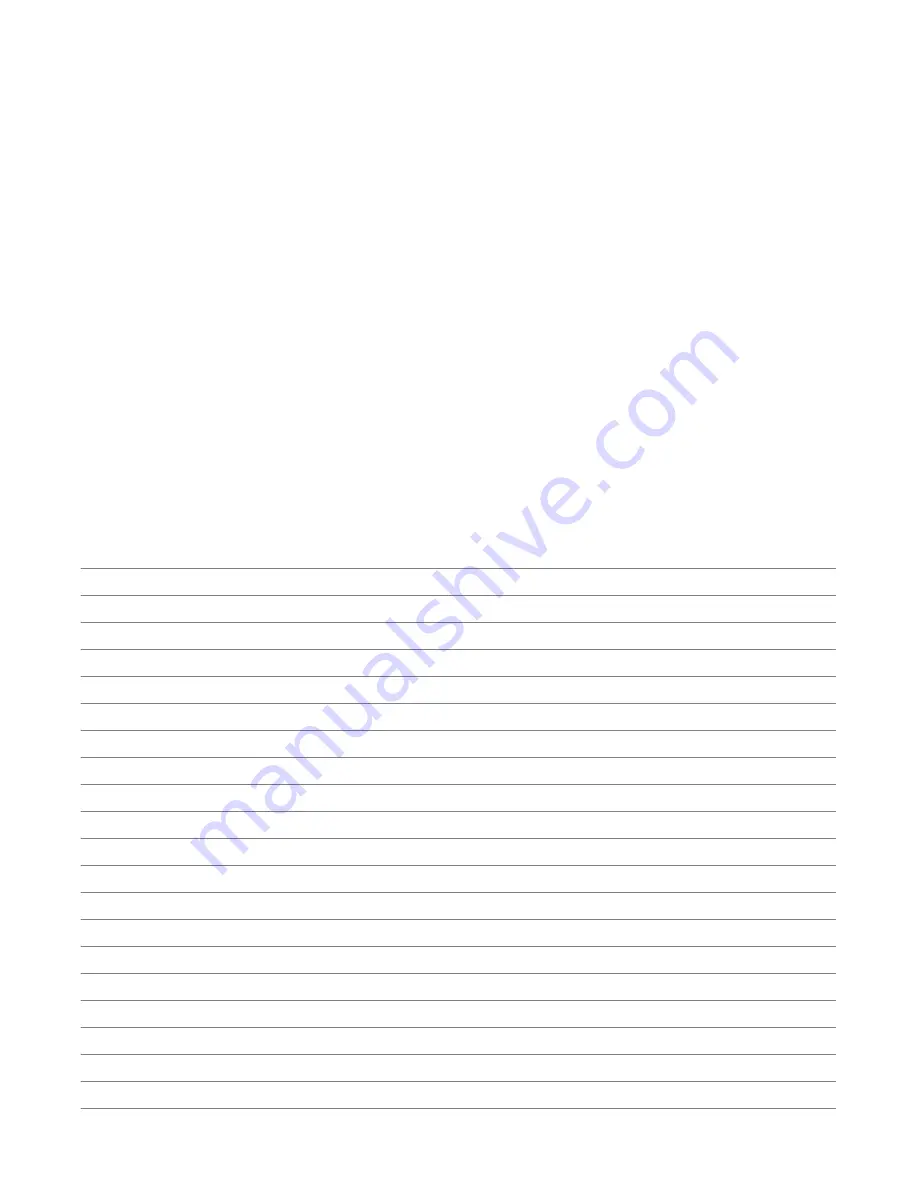
.
A complete Parts List is available at www.MillerWelds.com
OM-254915 Page 13
4-7. Millermatic 350P Aluminum Differences vs Standard Millermatic 350/350P
1.
Aluminum Only
−
The Millermatic 350P Aluminum has been optimized for Aluminum welding. Steel, Stainless Steel, and Metal Core wire types
are not intended to be used with the Millermatic 350P Aluminum.
2.
New .040” wire diameter
−
The .040” wire diameter has been added to all Aluminum programs to provide the user with more wire options.
3.
Torque motor vs. Constant Speed motor
−
One of the major improvements to the Millermatic 350P Aluminum is the new torque motor. The new
torque motor virtually eliminates all feeding problems, downtime related to aluminum shaving, birds nesting, and destroyed liners.
4.
Gun Calibration vs. Motor Calibration
−
The Millermatic 350P relied on precisely matching the speeds of the push motor and the pull motor.
Variations in each of the motors resulted in wire feeding issues. The new torque motor eliminates many of the feeding issues. However, for
optimum performance Miller has added a Gun calibration routine to the Millermatic 350P Aluminum. This new routine allows the welding machine
to learn the physical characteristics of the gun and adjust its operation to provide the most ideal feeding scenario. See Section 6-15 for
more detailed information on Gun Calibration.
5.
SUP is gone
−
The new torque motor eliminates the need for SUP value in the Millermatic 350P Aluminum.
6.
Jog/Purge Button
−
For increased ease of use the Millermatic 350P Aluminum has a Jog/Purge button. With the press of a button the user can Jog
wire or Purge gas. See section 6-7 for more information on the Jog feature. See Section 6-8 for more information on the Purge feature.
7.
Trigger Hold
−
The new Millermatic 350P Aluminum includes a Trigger Hold feature to reduce wear and tear on the user. Long continuous welds
can now be made without the need for constant trigger pressure. See section 6-10 for more information on the Trigger Hold feature.
8.
Trigger Schedule Select
−
The new Millermatic 350P Aluminum includes dual schedule which allows an operator to switch between two
pre-programmed weld settings by the quick tap of the trigger. For more information on this feature see Section 6-16.
9.
Synergic MIG
−
Synergic MIG gives the non-Pulse operators the ability to apply synergic control to the welding output based on the wire feed
speed.
10. Electronic Wire Spool Brake
−
Allows wire spool to free spool while welding which provides optimum wire free delivery. When the gun trigger is
released, the brake engages.
Notes
Summary of Contents for Millermatic 350P
Page 63: ...OM 254915 Page 59 Notes...
Page 65: ...OM 254915 Page 61 255730 J...