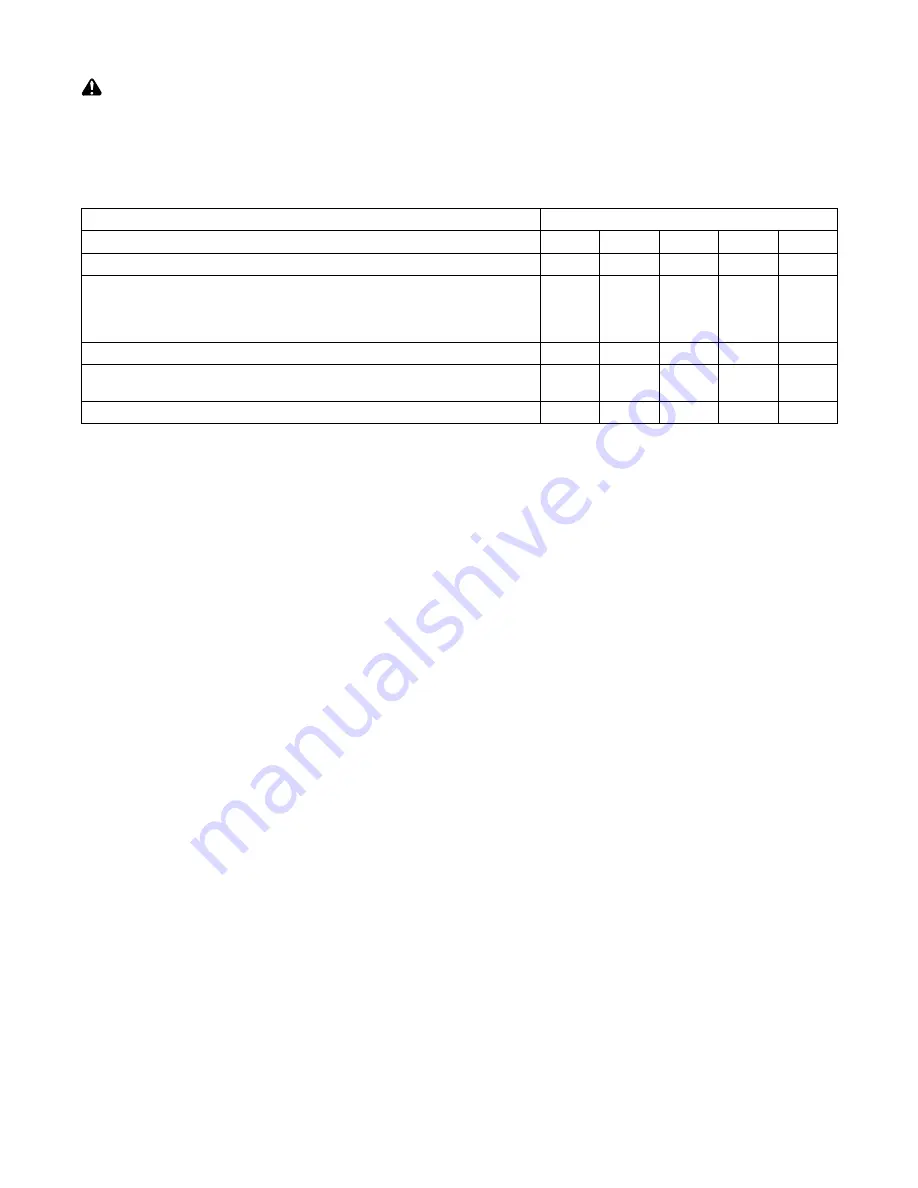
OM-210 540 Page 19
3-12. Electrical Service Guide
Failure to follow these electrical service guide recommendations could create an electric shock or fire hazard. These recommenda-
tions are for a dedicated branch circuit sized for the rated output and duty cycle of the welding power source.
NOTICE − INCORRECT INPUT POWER can damage this welding power source. This welding power source requires a CONTINUOUS supply of
input power at rated frequency
(+
10%) and voltage
(+
10%). Phase to ground voltage shall not 10% of rated input voltage. Do not use a genera-
tor with automatic idle device (that idles engine when no load is sensed) to supply input power to this welding power source.
.
Actual input voltage should not exceed
±
10% of indicated required input voltage. If actual input voltage is outside of this range, output may not
be available.
60 Hz Three Phase
Input Voltage
208
230
400
460
575
Input Amperes At Rated Output
67
59
34
29
23
Max Recommended Standard Fuse Rating In Amperes
Circuit Breaker
1
, Time-Delay
2
80
70
40
35
25
Normal Operating
3
100
90
50
45
35
Min Input Conductor Size In AWG
4
4
6
8
10
10
Max Recommended Input Conductor Length In Feet (Meters)
173
(53)
136
(42)
263
(80)
228
(69)
356
(108)
Min Grounding Conductor Size In AWG
4
8
8
8
10
10
Reference: 2005 National Electrical Code (NEC) (including article 630)
1 Choose a circuit breaker with time-current curves comparable to a Time Delay Fuse.
2 “Time-Delay” fuses are UL class “RK5” .
3 “Normal Operating” (general purpose - no intentional delay) fuses are UL class “K5” (up to and including 60 amp), and UL class “H” ( 65 amp and
above).
4 Conductor data in this section specifies conductor size (excluding flexible cord or cable) between the panelboard and the equipment per NEC Table
310.16. If a flexible cord or cable is used, minimum conductor size may increase. See NEC Table 400.5(A) for flexible cord and cable requirements.
Summary of Contents for Auto-Axcess 450
Page 14: ...OM 210 540 Page 10...
Page 51: ...OM 210 540 Page 47 Notes...
Page 53: ...OM 210 540 Page 49 207 903 G Part 1 Of 2...
Page 54: ...OM 210 540 Page 50 Figure 8 2 Circuit Diagram For Welding Power Source Part 2 Of 2...
Page 55: ...OM 210 540 Page 51 207 903 G Part 2 Of 2...
Page 56: ...OM 210 540 Page 52 Figure 8 3 Circuit Diagram For 72 Pin Robot Interface...
Page 57: ...OM 210 540 Page 53 219 266 C...
Page 58: ...OM 210 540 Page 54 Figure 8 4 Circuit Diagram For Peripheral Motor Interface...
Page 59: ...OM 210 540 Page 55 219 267 B...