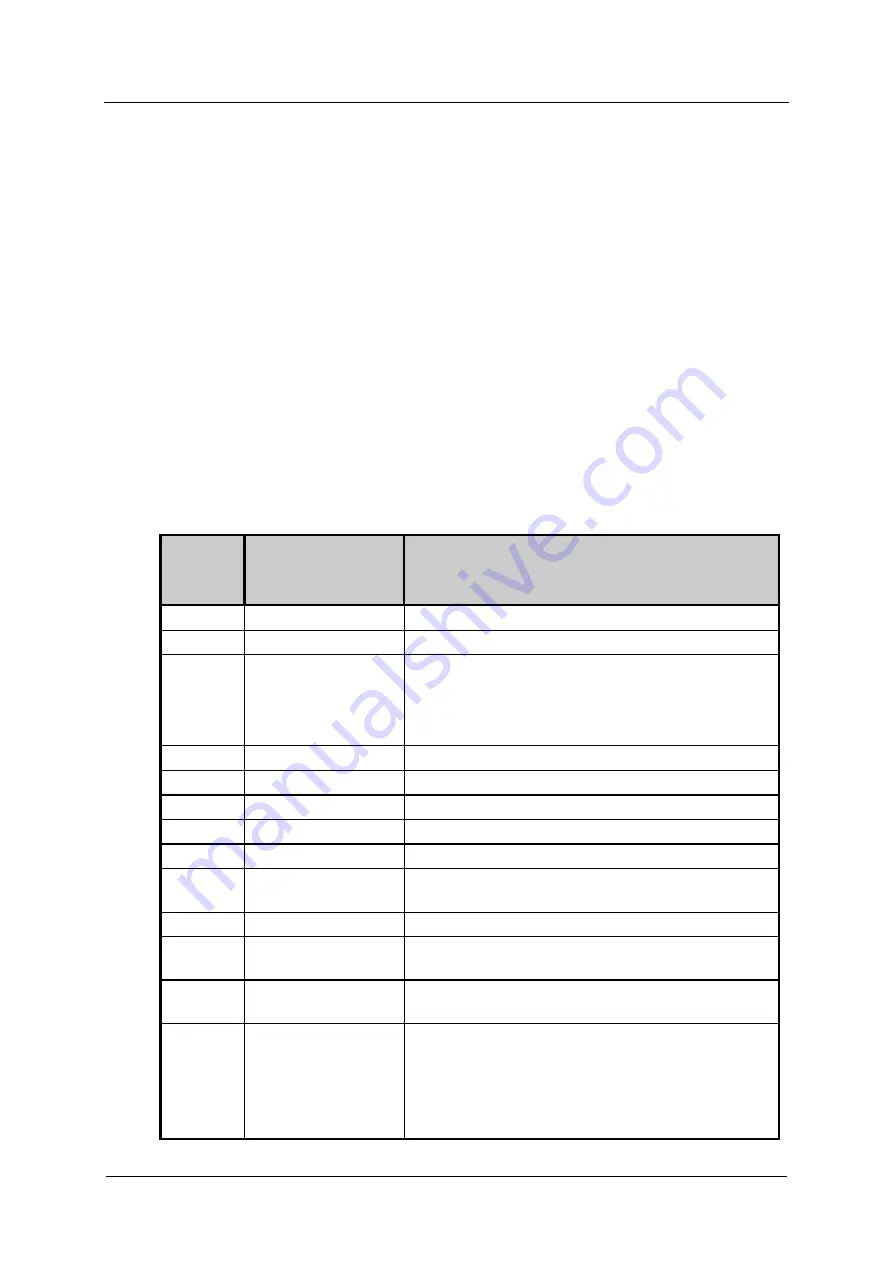
ALARMS AND EVENTS LIST
REV.0.03_COD.610078_A4
Page 42
12.
ALARMS AND EVENTS LIST
12.1
Description of alarm messages
During machine operation, the user is aided by
ALARMS
or
ALARM MESSAGES
which
make use of visual signals on the operator display panel to advise of possible anomalies in
progress and machine alarms which have intervened.
Intervention of an ALARM during operation of the system is signaled to the user by a
message on the operator panel.
The alarm which appears on the panel remains active until the cause of intervention is
removed.
The intervention of an alarm stops the wash cycle currently in progress.
12.2
List of alarm messages
Possible alarms which may intervene during a work cycle are shown on the control panel
display.
The message includes the number of the alarm that has intervened and its name.
A complete list of possible alarm messages follows.
ALARM
DISPLAY
MESSAGE
DESCRIPTION
E 2
open load. door
Door open and/or unlocked during cycle.
E 4
load.door fail.
Door blocked but open (discrepancy).
E 7
unblock.door 1
Door problems:
Overtime lock door.
During block door, the door has been
opened.
E 9
unlocking 1fail.
Overtime unlock door.
E11 no
cold
water Timeout
cold water filling level
E12
no hot water
Timeout hot water filling level
E13
no demin. water
Timeout demineralized water filling level
E23
drain problem
Timeout minimum water level during the drain.
E26 prewash
max°C
Chamber temperature exceeded selected value
during pre-wash.
E27
tank probe lim°C
Chamber temperature above maximum value.
E30 tank
probe
Temperature sensor defective - Operation sensor
(sensor 1)
E31
tank probe 2
Defective temperature sensor - Redundant sensor
(sensor 2)
E34 check
temp.
Appears when all the following conditions are met:
Chamber temperature above selected value.
Temperature difference between the two
probes is greater than 35.6°F (2°C).
Chamber heating failure.