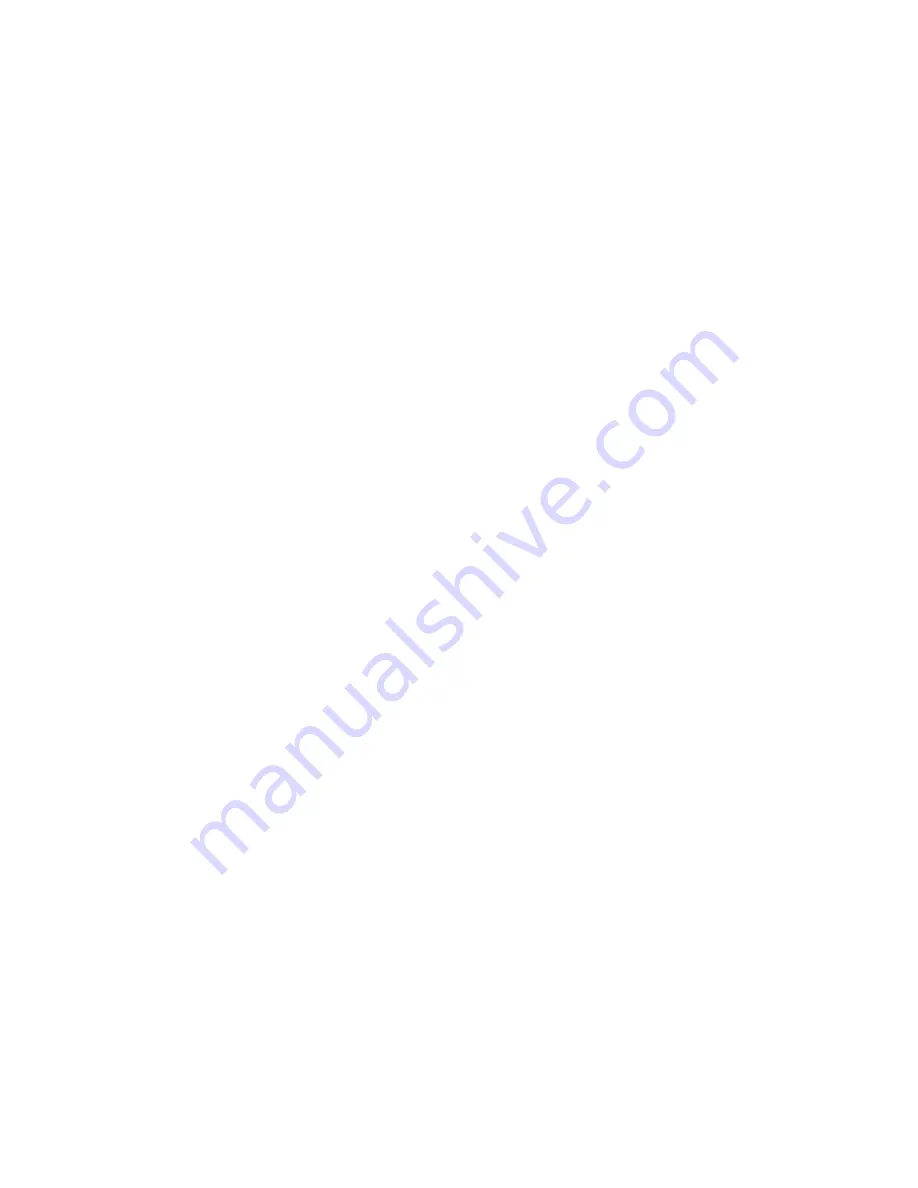
20
II. NORMAL OPERATION - STEP-BY-STEP-
A. Daily Startup Procedure
1.
Check that the circuit breaker/fused disconnect is in the On
position. Check that the window is closed. The touch panel
display should be lit.
2.
Adjust the conveyor to the desired bake time.
3.
Press the temperature button to display right and left hand
oven settings. Set temperatures as desired.
4.
Press the ON button to activate the oven. The conveyor will
not run, until the oven temperature has reached the set
points.
B. Daily Shutdown Procedure
1.
Make certain there are no products left on the conveyor in
the oven.
2.
Press the ON square to turn the oven off.
3.
Open the window to allow the oven to cool faster.
4.
After the oven has cooled and the blowers have turned off, the
circuit breaker/fused disconnect may be turned off.
Quick Reference – Touch Screen Controller
A. Main Screen
1.
On/Off button - Used to turn oven On and Off.
2.
Conveyor speed - Pressing on either the minutes or
seconds allows a new value to be input for the conveyor
speed. Split belt ovens have two inputs (front and rear
belts).
3.
Oven temperature - Pressing on the set temperature shifts
the user to the oven temperature set point/indicator screen.
4.
Energy level indicators - Indicators to either side of the
screen indicate the energy input to that side of the oven.
5.
Message bar - Indicates various messages pertaining to
current oven conditions.
B. Oven Temperature/Set Point/Indicator Screen
1.
Right actual temperature - Indicates current average tem-
perature of the right side of the oven.
2.
Left actual temperature - Indicates current average tem-
perature of the left side of the oven.
NOTE:
Right to Left temperature settings should not exceed
a differential of 20 °F.
3.
Right Set point temperature - Pressing on this value allows
the user to adjust the set point for the right side of the oven.
4.
Left Set point temperature - Pressing on this value allows
the user to adjust the set point for the left side of the oven.
5.
Exit - Returns to the main screen.
C. Energy Modes
Energy Mode One
- This mode is automatic, and starts (bake
time +1 minute) after the last product has entered the oven. In
this mode, the main oven blowers will lower to 1500 RPM, while
the oven maintains temperature and belt speed.
Energy Mode Two
- The oven lowers its set point by 100° F, and
stops the belt. Anytime that the oven is more than 10 degrees
over its set point, the ovens will completely shut off, allowing the
oven to cool. The main blowers will continue to run at 1500 RPM
in this mode. Placing any article on the input belt will cause
normal operation of the oven to resume, and bring the set point
back to its original level. The belt will resume operation once
both sides of the oven are within 5° F of the set point.
Energy Mode Three
- The oven will turn off completely and
shut off the circulation blowers once the oven temperature has
dropped below 200° F. Placing any article on the input belt will
cause normal operation of the oven to resume, and bring the set
point back to its original level. The belt will resume operation
once both sides of the over are within 5° F of the set point.
Energy Mode Four
- This is a complete oven shut down.
Placing anything on the belt will NOT return the oven to
Operation. The ON button on the main screen has to be pressed
to restart the oven.