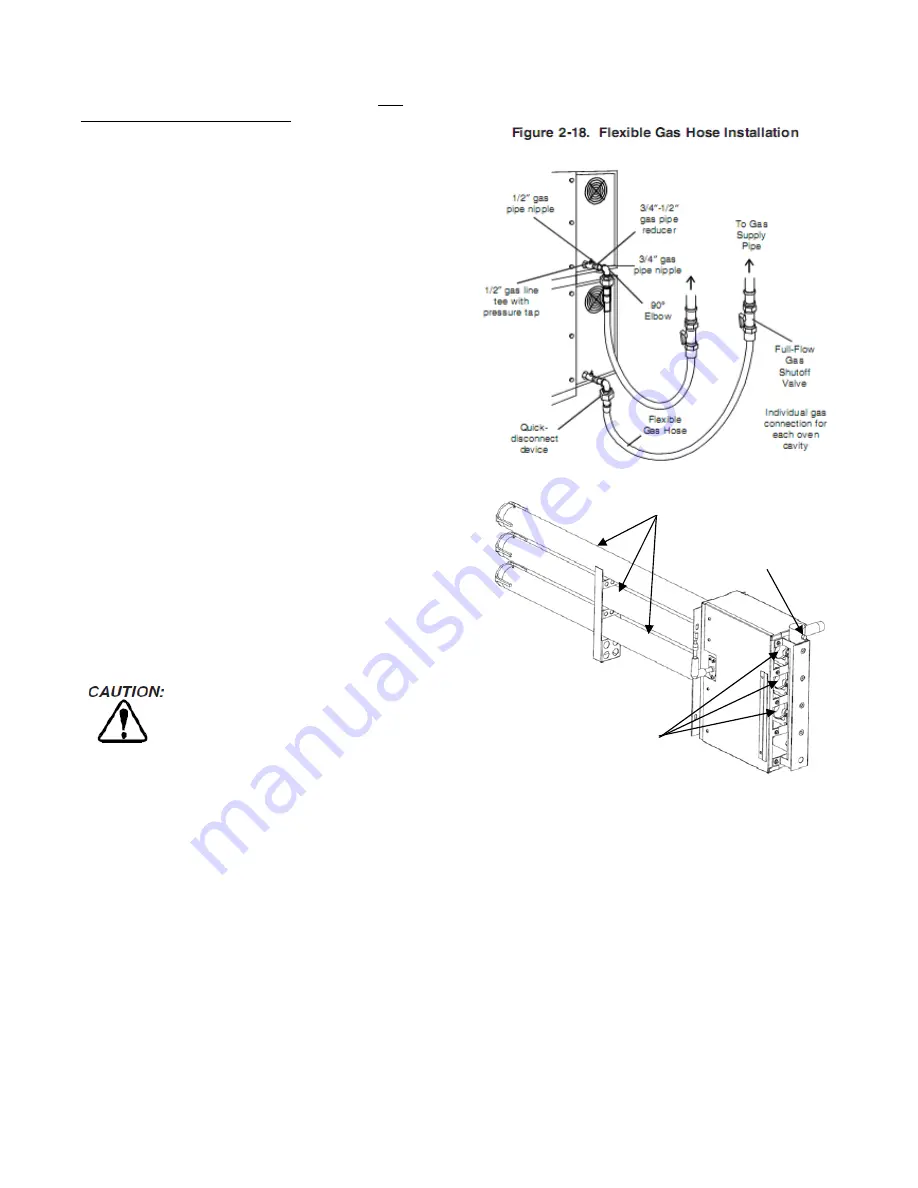
16
B.
Connection
Check the oven’s gas supply requirements before making
the gas utility connections. Gas supply requirements are
listed on the oven’s serial plate and in Table 1-4. Gas
Orifice and Pressure Specifications (in Section 1,
Description).
Check the serial plate to determine the type of gas (Propane
or Natural) to be used with the oven.
Refer to the instructions in the gas hose package (included
in the Installation Kit) before connecting the gas line. One
gas line connection method is shown in Figure 2-18;
however, compliance with the applicable standards and
regulations is mandatory.
Inlet, regulated, and pilot gas pressure readings can be
taken using a digital tube manometer at the tap location
shown in Figure 2-19. Figure 2-19 shows the burner
assembly and Figure 2-21 shows the gas valve.
NOTE:
The installation must conform with local codes or in
the absence of local codes, to the National Fuel
Gas Code, ANSI Z223.1-latest edition.
Certain safety code requirements exist for the installation of
gas ovens; refer to the beginning of Section 2 for a list of the
installation standards. In addition, because the oven is
equipped with casters, the gas line connection shall be made
with a connector that complies with the Standard for
Connectors for Movable Gas Appliances, ANSI Z21.69 (in
U.S.A.), as well as a quick-disconnect device that complies
with the Standard for Quick-Disconnect Devices for Use With
Gas Fuel, ANSI Z21.41 (in U.S.A.).
C. Gas Conversion
Where
permitted
by local and national codes, it is possible to
convert ovens from natural gas to propane or from propane
to natural gas. Use the appropriate Middleby Gas
Conversion Kit for the specific oven model.
The terms of the oven’s warranty require all
startups, conversions and service work to be
performed by a Middleby Authorized Service
Agent.
D. PS360G Propane Conversion
Three items must be changed to change the oven to operate
on LP: (See Addendum for Propane Conversion Kit # 72870)
1. Replace main orifices.
2. Adjust main gas regulator.
3. Adjust the ModuPlus Valve per instructions below.
Disconnect the manifold union closest to the main burner,
and remove the manifold assembly (four screws). Slide out
the manifold assembly (leaving the ignition and sense wires
connected). Replace the main orifices.
Replace the main orifices on the manifold assemblies with
the LP orifices, and replace the manifold assembly.
Reconnect the union.
Remove the seal cap on the regulator and rotate the
adjustment screw in the clockwise direction to increase the
regulated pressure.
E. Adjusting the Maximum Pressure Setting
1. Disconnect pressure feedback connection (if applicable).
2. Connect a suitable pressure gauge to pipe line or to outlet
pressure tap of gas control concerned, to measure burner
pressure (measuring point must be as near to burner as
possible).
Figure 2-19. Gas Burner Assembly
3. Make sure that the appliance is in operation and the
Moduplus
®
coil is energized with maximum current.
4. If maximum rate pressure needs adjustment, use an 8 mm
wrench to turn adjustment screw for maximum pressure
setting (clockwise to increase or counter-clockwise to
decrease pressure), until the desired maximum outlet
pressure is obtained. The correct value to adjust the
manifold pressure is shown in Table 1-4.
5. Disconnect electrical connection of the Moduplus
®
.
6. Check minimum pressure setting and readjust if
necessary. (See Adjusting Minimum Pressure Setting for
proper adjusting procedure.)
7. Reconnect pressure feedback connection (if applicable).
8. If minimum and maximum pressures are set, wire the
Moduplus
®
in circuit.
9. Close pressure tap screw.
FLAME TUBES
MANIFOLD
PRESSURE TAP
GAS BURNERS
Summary of Contents for PS360G Gas
Page 10: ...5 A PN 69669 SINGLE OVEN BASE TOP KIT...
Page 11: ...6 B PN 70274 DOUBLE OVEN BASE TOP KIT...
Page 12: ...7 C PN 70275 TRIPLE OVEN BASE TOP KIT...
Page 13: ...8...
Page 14: ...9...
Page 35: ...30 SECTION 5 WIRING DIAGRAMS...
Page 36: ...31...
Page 37: ...32...
Page 38: ...33...
Page 39: ...34 ADDENDUM PS360GWB Propane Conversion Kit 72870 Instructions Part Number 72869 Revision B...
Page 40: ...35 NOTES...
Page 41: ...36 NOTES...
Page 42: ......