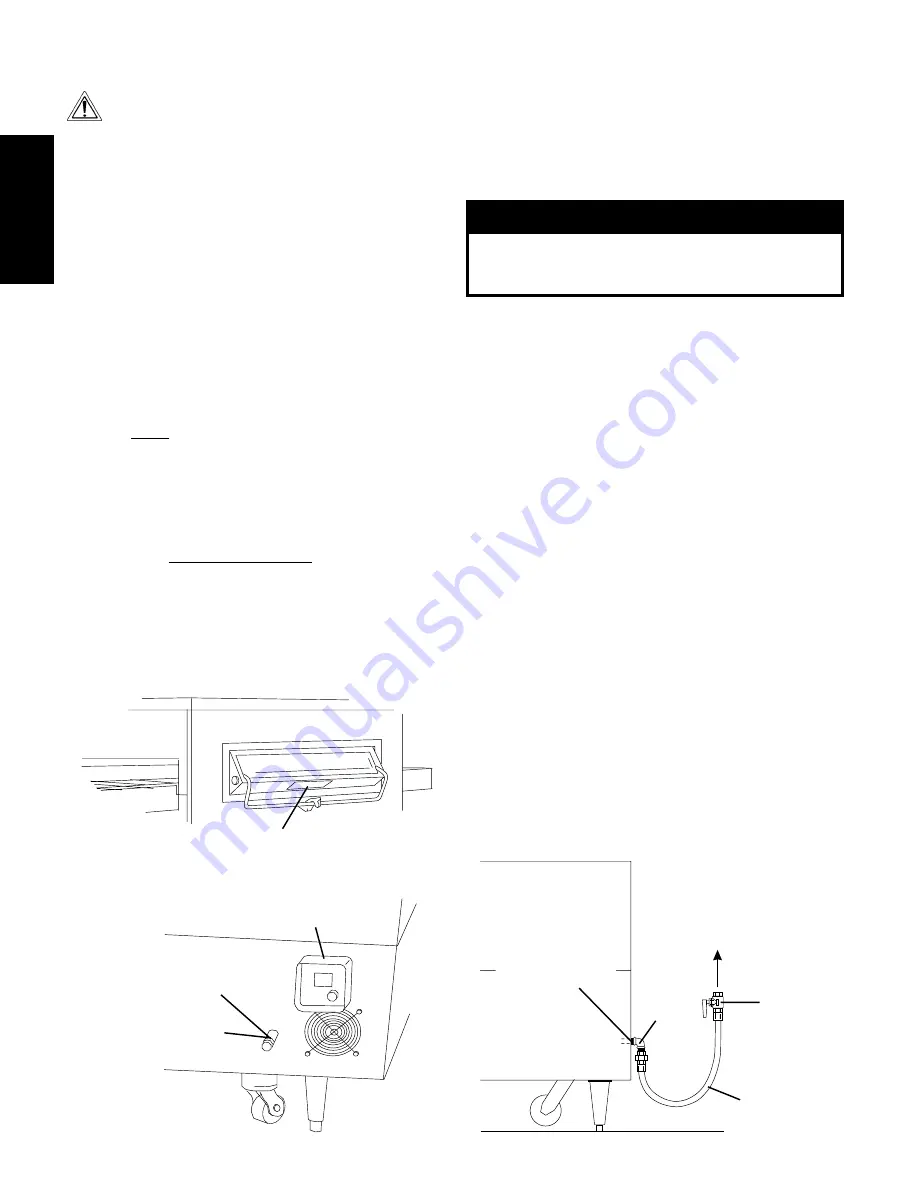
ENGLISH
14
Figure 2-24 - Utility Connection Locations
Electrical
Junction Box
Figure 2-23 - Oven Serial Plate
Gas oven:
3/4" (19mm) pipe for
gas utility connection
Electric oven:
1-1/2" (38mm) conduit for
electric utility connection
Figure 2-25 - Flexible Gas
Hose Installation
Appliance
Connection/Male
Nipple
Flexible
Gas Hose
Full-Flow Gas
Shutoff Valve
To Gas
Supply Pipe
90°
Elbow
SECTION 2 - INSTALLATION
Serial plate location
NOTE:
The location of these
components may vary slightly
depending on the oven model.
VIII. ELECTRICAL SUPPLY (all ovens)
WARNING
Authorized supplier personnel normally accomplish
the connections for the ventilation system, electric supply,
and gas supply, as arranged by the customer. Following these
connections, the factory-authorized installer can perform the
initial startup of the oven.
NOTE:
The electric supply installation must satisfy the
requirements of the appropriate statutory authority, such as the
National Electrical Code (NEC), ANSI/NFPA70, (U.S.A.); the
Canadian Electrical Code, CSA C22.2; the Australian Code
AG601; or other applicable regulations.
NOTE:
The electric supply connection must meet all national
and local electrical code requirements.
Check the oven serial plate before making any electric supply
connections. Electric supply connections must agree with data
on the oven serial plate. The location of the serial plate is shown
in Figure 2-23.
A fused disconnect switch or a main circuit breaker (customer
furnished) MUST be installed in the electric supply line for each
oven cavity. It is recommended that this switch/circuit breaker
have lockout/tagout capability.
The supply conductors must be of the size and material (copper)
recommended. Refer to the wiring diagram inside the machin-
ery compartment or control compartment of the oven. Electrical
specifications are also listed on the oven's serial plate (Figure
2-23) and in the Electrical Specifications table (on Page 5).
The oven requires a ground connection to the oven ground screw
located in the electrical junction box. (The box is shown in Figure
2-24.) If necessary, have the electrician supply the ground wire.
Do NOT use the wiring conduit or other piping for ground
connections!
CAUTION
Before connecting incoming power to the oven, measure the
voltage of each input leg to neutral. The expected voltage is
approximately 120V. ANY voltage reading exceeding 130V
indicates that the supply has a high leg. CONNECTING A
HIGH LEG TO THE OVEN VOIDS ALL OVEN WARRANTIES.
Connecting a high leg to the black lead of the oven can severely
damage the ovens electrical and electronic components.
CAUTION
DO NOT CONNECT BLACK WIRE TO HIGH LEG.
VOLTAGE OF THE BLACK AND WHITE WIRES MUST
BE NO HIGHER THAN 130 VAC.
A. Additional Information - Electric Ovens
For electric ovens, a 1-1/4" (32mm) dia. cutout in the back
wall of the machinery compartment provides access for the
electrical supply connections. Using flexible cables for the
electric power supply conductors requires a 1-1/4" (32mm)
strain-relief fitting (not furnished with the oven) to enable
safe access to the terminal block from which power is
distributed to the oven.
B. Additional Information - Gas Ovens
All gas oven electric supply connections are made via the
electrical junction box on the rear of the oven, shown in
Figure 2-24. The power lines then connect to the oven
circuits through the Machinery Compartment Access Panel
Safety Switch. This switch interrupts electric power to the
oven when the Machinery Compartment Access Panel is
opened.
C. Additional Information - Ovens with External Transform-
ers (export versions)
Position the transformer on the rear wall of the oven, on the
same side as the control compartment, as space permits.
Fasten it in place using the supplied mounting hardware.
D. Connection
Refer to the wiring diagram inside the machinery
compartment or control compartment of the oven to
determine the correct connections for the electrical supply
lines. Connect the supply as indicated on the wiring
diagram. Be sure to connect the electrical supply ground
wire to the oven ground screw located in the junction box
on the rear of the oven.