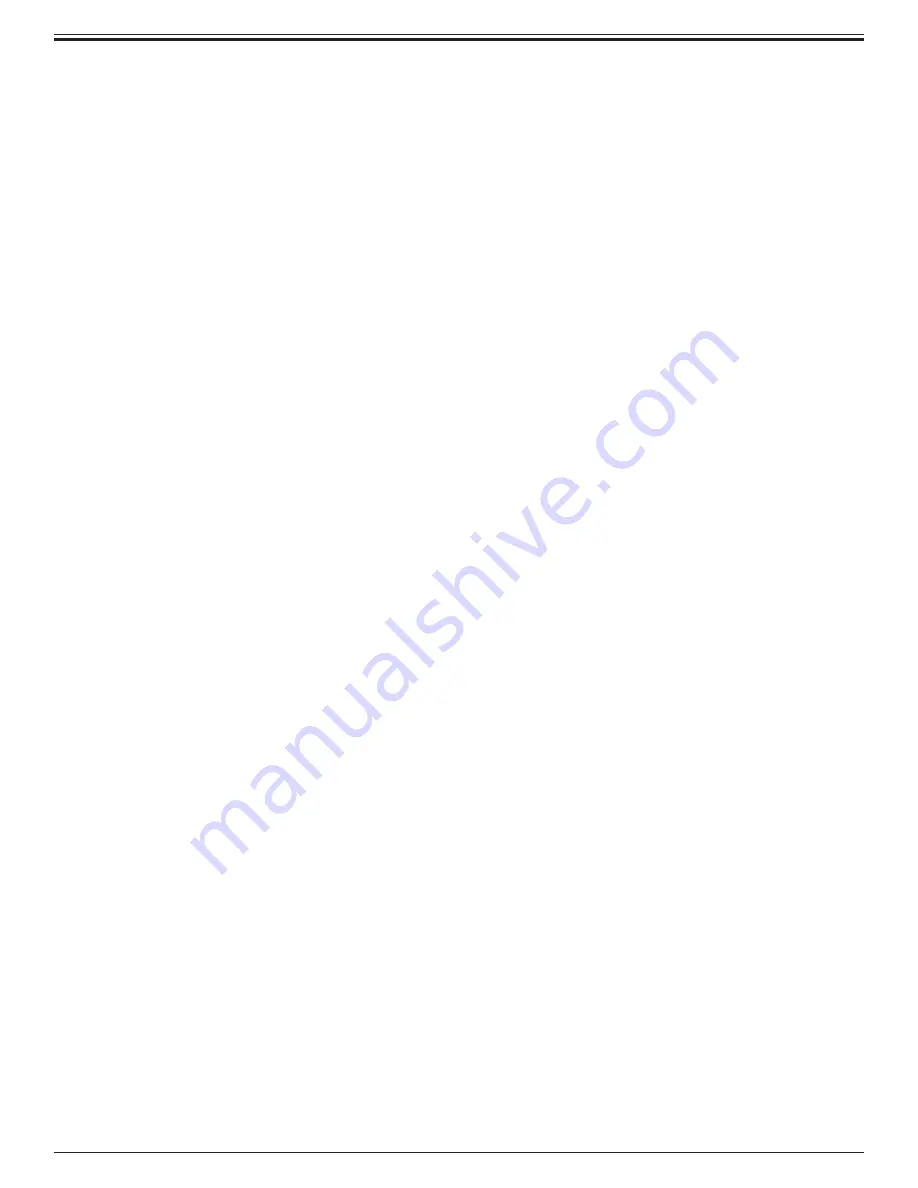
8
this may cause excessive noise as the reject
water is flowing to drain.
Firmly press one end of the tubing over the
3
/
8
"
drain outlet hose barb on the Dispensing
Faucet. Allow the tubing to relax, then press
firmly again to insure proper seating. No
connectors are required when attaching hose
to Hose Barbs. Route the tubing to the Drain
Clamp and trim to length.
•Refer to Fig. 4, page 7. To connect the Drain
Tubing, install the Compression Nut and the
Brass Insert.
•Insert the tubing into the Drain Clamp and
tighten the Compression Nut.
D. R.O. Manifold Assembly Installation
Locate the site per Sec. III, C.3, page 5. Various
installation sites will require different types of
mounting fasteners; be sure the fastener selected
will provide a firm, solid mounting. A support
panel may be necessary on thin cabinet walls or to
span between wall studs on particleboard or
drywall.
Do not drill through exterior cabinet walls or
leave sharp wood screw points exposed in readily
accessible cabinet interiors.
The close proximity of a dishwasher or a trash
compactor may require special fabrication of a
mounting plate.
1. The mounting bracket will accept either #10
or #12 (5mm) mounting screws spaced on 9½"
(24 cm) centers. Allow at least 4" (10 cm) of
clearance beneath the filter housings to
accommodate filter changes. Mark the two
locations (the bracket can be used as a
template). Install the screws and tighten them
until the heads are about
5
/
8
" from the wall.
2. Locate the ¼" Red Feed Water Tubing.
Remove the red plug from the fitting labelled
“In” on the manifold and insert the tubing.
Reference the special supplement sheet in the
carton for proper connection of all tubing and
removal of plugs. Run the tubing along its
course to the Feed Water Saddle Valve, trim to
length. (Refer to Fig. 1, page 1.)
Refer to Fig. 3, page 6. To the end of the red
polytube install the Compression Nut, the
Plastic Ferrule, and the Brass Insert. Connect
to the Feed Water Saddle Valve.
3. Locate the ¼" Black Drain Tubing. Remove
the black plug from the fitting labelled “Drain”
on the manifold and insert the tubing. Run the
tubing along its course to the ¼" Hose Barb on
the Dispensing Faucet, trim to length and
connect by firmly pressing over the barb.
Allow the tubing to relax, then press firmly
again to insure proper seating.
4. Locate the ¼" yellow tubing with the tee
attached to one end. Remove the yellow plug
from the fitting labelled "Out" on the manifold
and insert the tubing.
5. Locate the
3
/
8
" Blue Product Water Tubing.
Firmly press one end into the tee and the other
end into the faucet connector. (Refer to Fig. 1,
page 1.) The fittings will grab the tubing and
seal it in place. Make sure the tubing is pressed
all the way in to create a pressure tight
connection.
NOTE: If you want to pull the tubing out for
some reason, push the ring around the tubing
in and pull the tubing out.
6. Hang the Manifold Assembly on the mounting
screws and tighten. DO NOT
OVERTIGHTEN.
7. Remove the wrapping from the
In–Line Activated Carbon Post Filter. Slice
the
3
/
8
" Blue Polytube where it would be
convenient to install and change the In–Line
Filter. Make a clean straight cut to insure
proper connections. The “Out” port on the
In–Line Filter should be toward the faucet.
Firmly press in the tubing. The fittings will
grab the tubing and seal it in place. Make sure
the tubing is pressed all the way in to create a
pressure tight connection.
E. Position the Drinking Water Holding Tank and
Make the Final Hose Connections.
1. Check the tank precharge pressure. Make sure
it is between 5 to 7 psig. If not, use a bicycle
hand pump or other pump to bring the
pressure up to the 5 to 7 psig range.
2. Pull the cap/plug off the top of the tank where
the Tank Shut–Off should go. (Refer to Fig. 1,
page 1.)
3. Wrap the white teflon tape, included in the
box, three times around the ¼" male outlet
thread. Wrap in the direction of the threads
(clockwise when looking down on the Holding
Tank). The tape will act as a thread sealant.
Screw on the Holding Tank Shut–Off Valve.