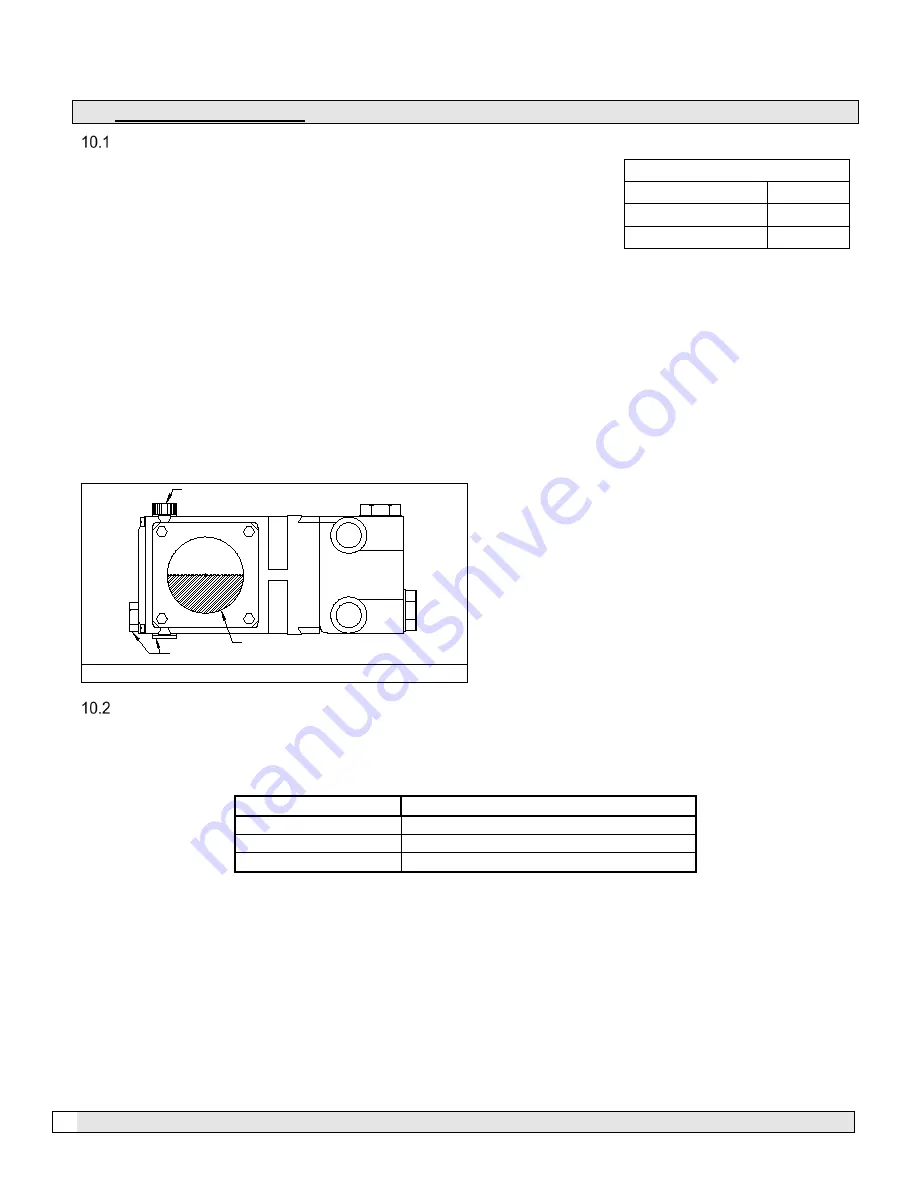
Master Rhino Manual_
March 2020.docx
March 20
Page 20 of 38
10.
SYSTEM MAINTENANCE
CRANKCASE OIL
The RHINO pump unit is equipped with an hour meter and an automatic
reminder to change pump oil; Red light, slow flash (does not affect
operation). See page 10 for instructions to reset light indicator.
Initially the Crankcase Oil must be changed after the first 50 operating
hours.
After that it should be changed after every 500 hours of operation.
Examples of 500 hours operation:
15 weeks of 5 hour operation per day
9 weeks of 8 hour operation per day
6 weeks of 12 hour operation per day
3 weeks of 24 hour operation per day
Chart to the right indicates oil capacity for each pump
SYNTHETIC 75w-90 GEAR OIL IS RECOMMENDED FOR ALL APPLICATIONS (Mobil One or Equal)
In the event that 75w-90 is not available, synthetic 15w-50 Motor oil may be substituted (Mobil One or
Equal)
Figure 20 – Crankcase Oil Levels
ELECTRICAL MOTOR SERVICE
Two types of electrical motors are used on the MicroCool
pump modules. Some small motors have sealed
rotor bearings and some require lubrication periodically. Refer to the motor nameplate for the type of motor. If
the motor is equipped with external grease nipples refer to the chart below for lubrication instructions.
Service Condition
Time Intervals
Standard
Every 3 Years
Severe
Every 1 Year
Seasonal
Lubricate at beginning of season
Electrical motors on the pump modules are pre-greased with a polyurea mineral oil NGLI grade 2-type grease
unless stated otherwise on the motor nameplate. Some compatible brands of polyurea mineral base type grease
are: Chevron SRI #2, Rykon Premium #2, Shell Oil Doilum R or Texaco Polystar RB. Motors are properly
lubricated at the time of manufacture and do not need to be lubricated at the time of installation.
NOTE: Over greasing bearings can cause premature bearing and/or motor failure. The amount of grease added
to the motor should be carefully controlled. One crank of the grease gun handle is usually sufficient.
Crankcase Oil Capacity
Giant P420A
30 fl oz.
Giant P470
30 fl oz.
Giant P536
68 fl oz.
FILL TO CENTER
OF SIGHT GLASS
OIL DRAIN
OIL FILL AND DIPSTICK
P400-P500 Giant Pump
Summary of Contents for RHINO 15
Page 28: ...Master Rhino Manual_March 2020 docx March 20 Page 28 of 38 RHINO BACK VIEW...
Page 29: ...Master Rhino Manual_March 2020 docx March 20 Page 29 of 38 RHINO RIGHT SIDE VIEW...
Page 30: ...Master Rhino Manual_March 2020 docx March 20 Page 30 of 38 RHINO LEFT SIDE VIEW...
Page 31: ...Master Rhino Manual_March 2020 docx March 20 Page 31 of 38 RHINO PLAN VIEW...
Page 32: ...Master Rhino Manual_March 2020 docx March 20 Page 32 of 38 RHINO FILTER AND BRACKET...
Page 33: ...Master Rhino Manual_March 2020 docx March 20 Page 33 of 38 CONTROL PANEL 1...
Page 34: ...Master Rhino Manual_March 2020 docx March 20 Page 34 of 38 CONTROL PANEL 2...
Page 35: ...Master Rhino Manual_March 2020 docx March 20 Page 35 of 38 CONTROL PANEL 3...
Page 36: ...Master Rhino Manual_March 2020 docx March 20 Page 36 of 38 CONTROL PANEL 4...
Page 37: ...Master Rhino Manual_March 2020 docx March 20 Page 37 of 38 RHINO SOLENOID...
Page 38: ...Master Rhino Manual_March 2020 docx March 20 Page 38 of 38 RHINO NOTES...