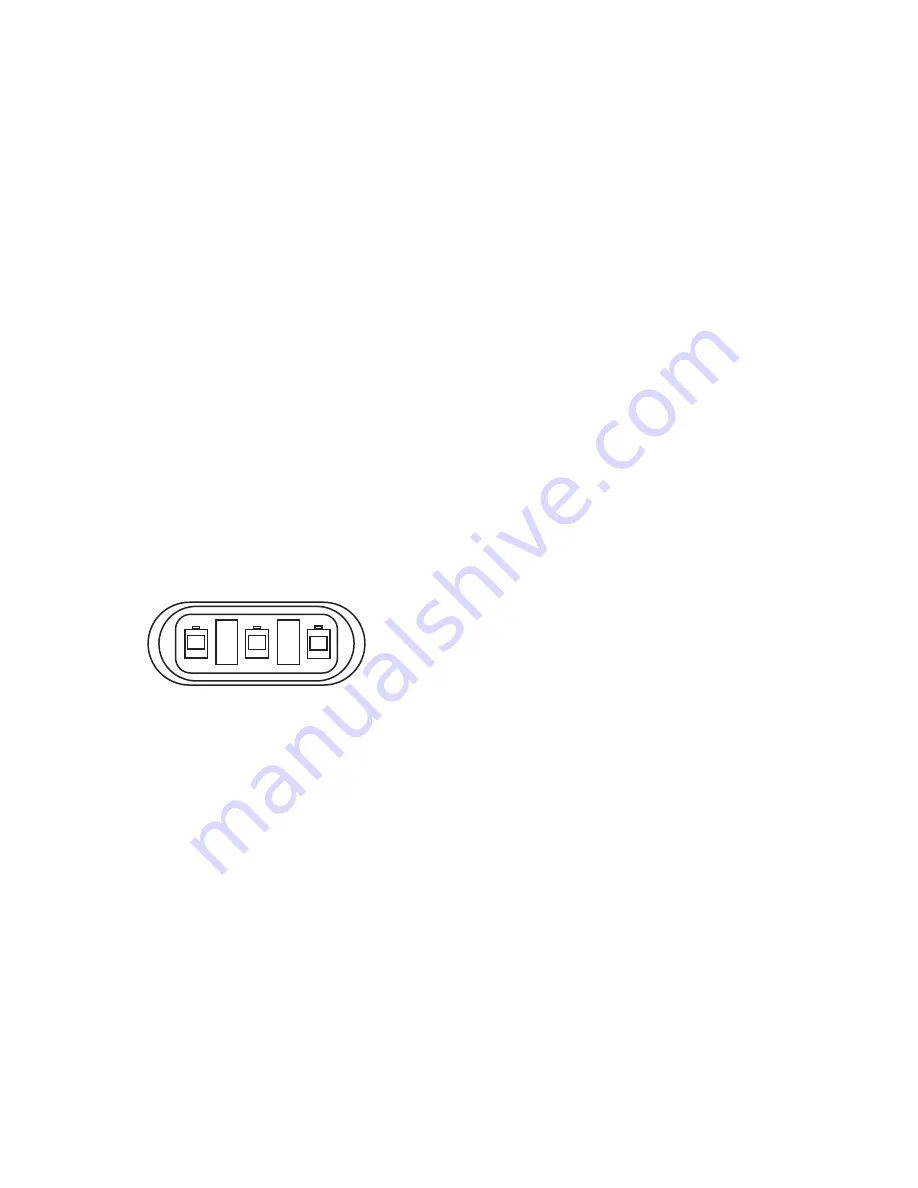
34
CONSOLE INPUTS
If there is no response from any of the following tests, refer to
the main wiring diagram to locate the next connector in line
to ward the con sole and repeat the test at that con nec tor. If there
is a response at that connector, the problem may be in the cable
between the two connectors (or the con nec tors themselves).
SPEED INPUT
Turn rotary switch to speed po si tion and dis con nect the
speed sensor (yel low tie) from the main harness. Check for
12 volts between pins B (white) and C (black) of the main
harness speed cable (yellow tie). Using a clip lead or other
jumper wire (such as a paper clip bent in a “U”), several times
rap id ly short to geth er pins A (red) and C (black) of the 3-pin
connector
(See Illustration 17).
The console should respond
with some speed read ing.
FLOW INPUT
Turn rotary switch to VOLUME/MINUTE and disconnect the
flow sen sor (green tie) from the main harness. Check for 12
volts be tween pins B (white) and C (black) of the main harness
flow cable (green tie). Using a clip lead or other jumper wire
(pa per clip bent in a “U”), several times rapidly short together
pins A (red) and C (black) of the 3-pin connector. The con sole
should re spond with some flow rate reading.
REMOTE RUN/HOLD INPUT
Disconnect the remote run/hold sensor (or jumper cover)
from the main harness.
Check for 12 volts between pins B (green) and C (violet) of
the main harness remote run/hold cable (grey tie). Placing a
clip lead or other jumper wire (such as a paper clip bent in a
“U”) between pins A (blue) and C (violet) of the main harness
run/hold connector (grey tie) should turn off the “HOLD”
icon on the console display. Removing the jumper should
turn on the “HOLD” icon on the console display.
FLOWMETER
Shaking the Flowmeter end to end should pro duce a “rattling”
sound (shaft end play). Blowing in the meter from either end
should spin the turbine freely. If the turbine spins freely but the
meter will not register flow with a known working sensor, the
turbine may be defective.
See Flow me ter Assembly and clean ing
on page 46 for details.
C
B
A
Three-Pin Connector
Illustration 17
SERVO VALVE CONTROL SIGNAL
With the console turned ON, put the console in MANUAL mode,
place the remote Run/Hold switch in the RUN position and turn
at least one boom switch to ON. Using a voltmeter or simple test
light, check from a good frame ground to each of the servo wires
on the main harness connector. You should get 0 volts on each
wire. Holding the “+” button should cause the RED wire to pulse
toward 12 volts (light will pulse). Holding the “-” button should
cause the BLACK wire to pulse toward 12 volts (light will pulse).
SERVO VALVE
The best way to test the servo valve is with a known working
console. Turn console ON, put the console in MANUAL mode,
place the remote Run/Hold in the RUN position, turn the
rotary switch to RATE and turn at least one boom switch to
ON. With the servo valve connected to the servo valve lead
on the main harness, holding the “+” button should close the
servo valve and holding the “-” button should open the servo
valve.
NOTE: Assuming you are in bypass configuration
(provided the console has passed the Servo Valve Control
Signal test). The servo valve should operate smoothly in
both directions, from fully open to fully closed.
You may also use a 9-volt transistor battery. Connecting the
battery to each terminal on the servo valve should cause the
servo valve to run in one direction. Reversing the battery
connections should cause the servo valve to run the other
direction. The servo valve should operate smoothly in both
directions, from fully open to fully closed.
PLUMBING
Proper plumbing is a very important factor in obtaining
optimal performance from your SprayMate II II system. The
chart on the next page will help you determine what area of
the plumbing may be causing your problem. At this point, it
is assumed that your plumbing basically matches that of the
system diagram and that the servo valve and flowmeter are
known to be installed correctly and functioning properly. In
addition, make certain that you have selected and installed
the correct spray tips for the application, speed and spray rate
that you intend to maintain. Don’t forget the obvious such as
leaky fittings and hoses, pinched hoses and plugged or worn
nozzles.
If you need more detail than the chart provides,
please refer to Plumbing Guidelines on pages 38 - 39.
Troubleshooting
(cont.)
Checking Console Inputs
Summary of Contents for 14869
Page 1: ...1 SprayMate II AUTOMATIC RATE CONTROLLER REFERENCE M A N U A L TM 1 1 1 1 1 1 1 1 1 1 1 1 1...
Page 7: ...7 SprayMateTM II System Overview P N 21778 P N 21963...
Page 8: ...8 P N 21963 P N 21779 P N 14313 P N 14316 SprayMateTM II Wiring Diagram...
Page 37: ...37 Appendices...
Page 45: ...45 P N 21779 P N 21778 Appendix F SprayMateTM II NH3 Specific Wiring Harness Diagram...