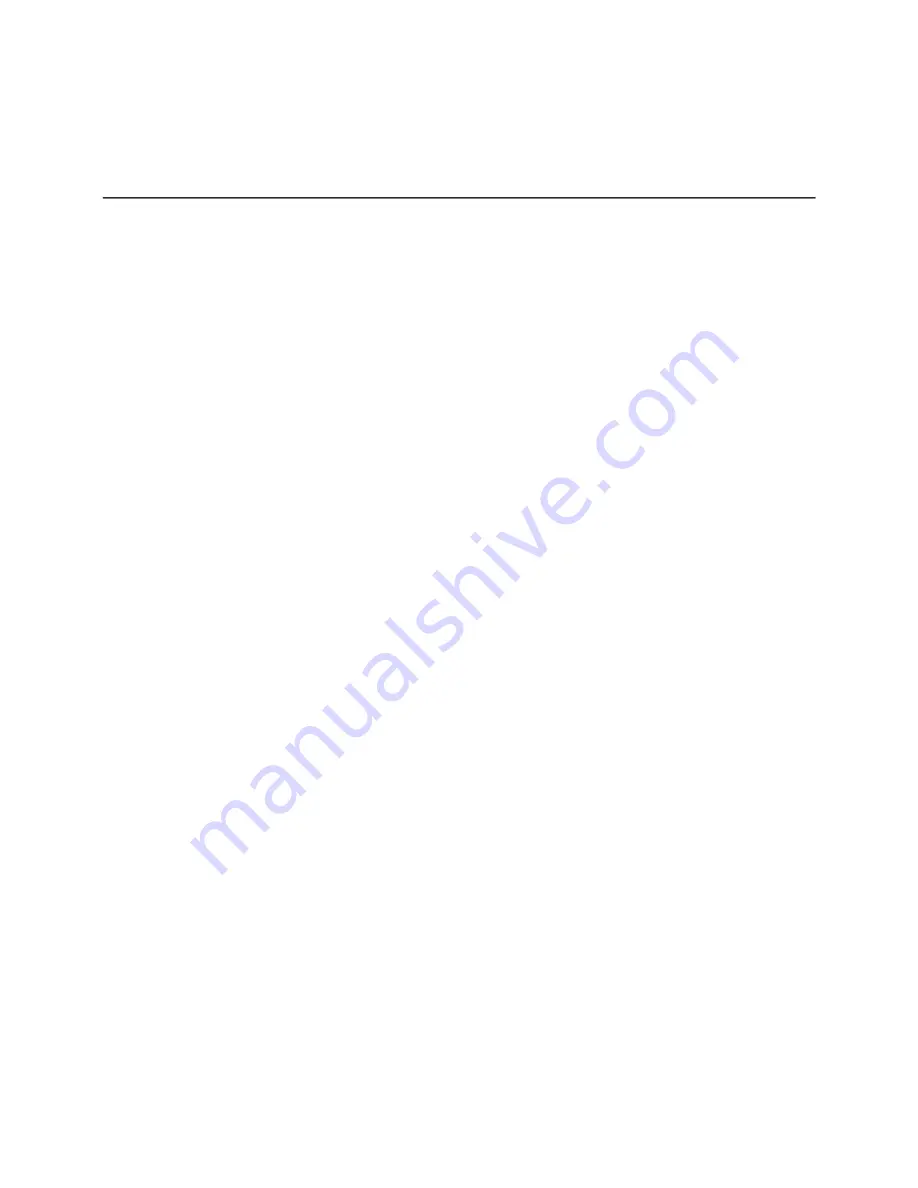
33 of 49
Service and maintenance
Monitoring and checking
Maintenance is fundamentally
essential for the safe and correct
operation and long life of the boiler.
It is recommended, that
combustion analysis be carried out
at regular intervals, in order to
monitor the load and pollutant
emissions of the boiler.
If the boiler is decommissioned in an
area where the room temperature in
winter can fall below 0°C, it is advised
to mix the water of the boiler with
antifreeze, to avoid frequent
evacuation.
Check carefully when using antifreeze
if this is suitable for stainless steel,
from which the inner part of the
heating appliance is made.
The manufacturer is not liable for
damage to the appliance or the
equipment caused by use of
unsuitable antifreeze or additives
Before starting servicing
Before performing any servicing and
cleaning, the appliance must be
disconnected from the mains.
Gas supply isolator and Water
Isolation valves closed for both
heating and Hot water