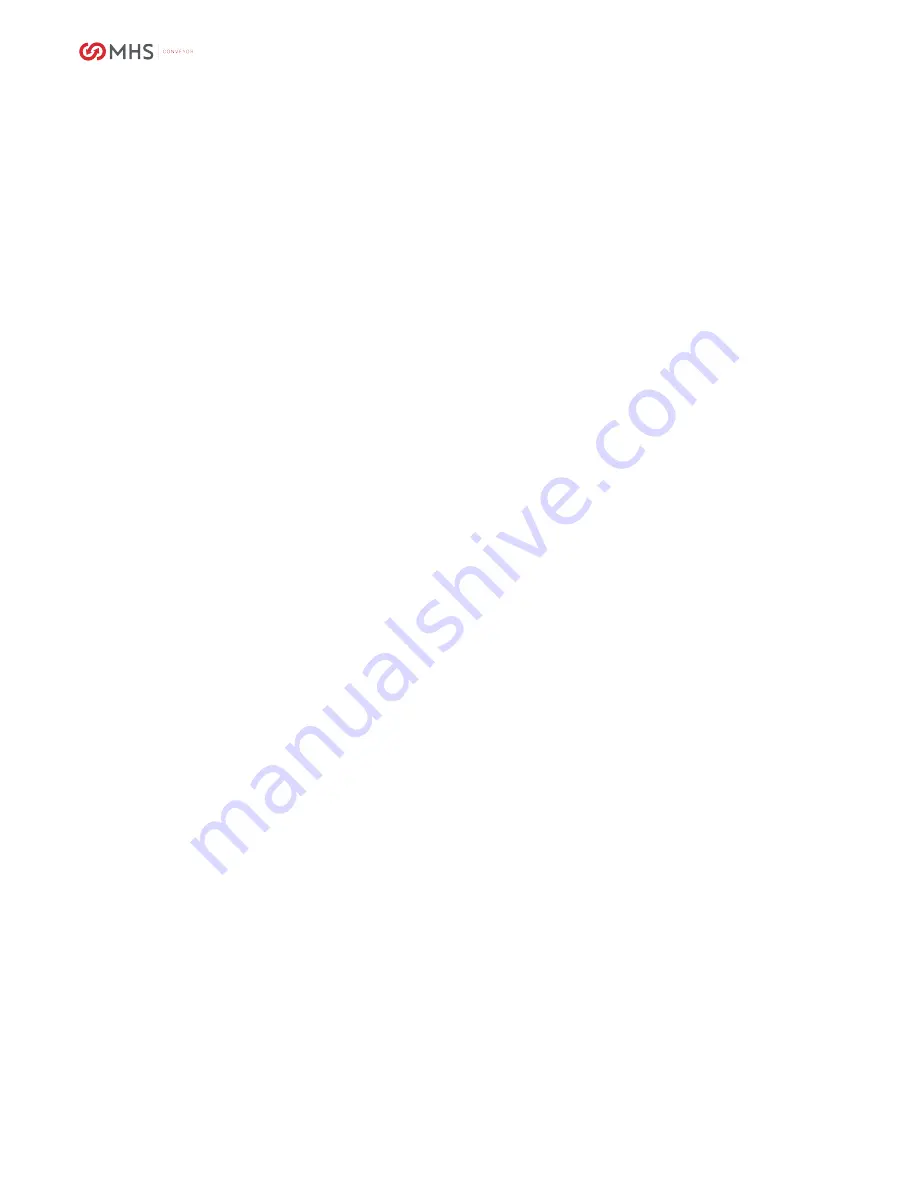
CRUZbelt
16
E0032544Rev090710
COMMISSIONING OF EQUIPMENT
GENERAL
Commissioning of the equipment can best be
defined as the final adjustments and test of the
installed equipment required for its proper operation.
The need for commissioning is inherent, since the
individual components of equipment are brought
together at the installation site to operate as a
system.
Mechanical and electrical commissioning is most
often carried out simultaneously. Commissioning
must simulate the actual operation of the system as
close as possible to demonstrate the ability to
perform reliably at the specified rate in the
prescribed operational sequence.
During the Commissioning Phase, it is necessary to
load the equipment with product to be conveyed,
which provides the means of detecting those areas
requiring adjustment. Personnel will be required to
support operational functions. This may serve as
part of operator training and familiarity with the
system. During the commissioning activity, special
attention should be directed toward personnel
safety. No unnecessary risks should be taken that
would endanger the safety of any personnel. All
personnel must familiarize themselves with all safety
features of the system such as emergency stops
and motor disconnects.
MECHANICAL STATIC CHECKOUT
(No power to the conveyor.)
1.
Follow the belt path through the entire conveyor.
2.
Visually inspect the installation. Is the conveyor
straight? Is the conveyor reasonably level from
side to side? From end to end?
3.
Check guard rail clearance to product.
4.
Eliminate all catch points.
5.
Check conveyor elevations.
6.
All bolts and set screws tight.
7.
Check product clearance to overhead structures.
8.
Simulate all operational functions with actual
product.
9.
All guards in place with proper clearance.
10. All OSHA required guards in place on walkways,
catwalks, ladder-ways, floor openings, etc.
11. All labels and warning signs in proper place,
unobstructed.
MECHANICAL DYNAMIC CHECKOUT
(Power to the conveyor, but no product on it.)
1.
Turn the motor ON. With the belt moving make
sure each belt has proper tension.
2.
Check the belt tracking.
Summary of Contents for CRUZ belt
Page 1: ...INSTALLATION OPERATION MAINTENANCE MANUAL CRUZ belt...
Page 2: ...CRUZbelt 2 E0032544Rev090710...
Page 7: ...CRUZbelt 7 E0032544Rev090710...
Page 26: ...CRUZbelt 26 E0032544Rev090710 REPLACEMENT PARTS...
Page 28: ...CRUZbelt 28 E0032544Rev090710 REPLACEMENT PARTS...
Page 30: ...CRUZbelt 30 E0032544Rev090710 REPLACEMENT PARTS...
Page 32: ...CRUZbelt 32 E0032544Rev090710 REPLACEMENT PARTS...
Page 37: ...CRUZbelt 37 E0032544Rev090710 REPLACEMENT PARTS...
Page 40: ...CRUZbelt 40 E0032544Rev090710 REPLACEMENT PARTS...
Page 42: ...CRUZbelt 42 E0032544Rev090710 REPLACEMENT PARTS...
Page 45: ...CRUZbelt 45 E0032544Rev090710...