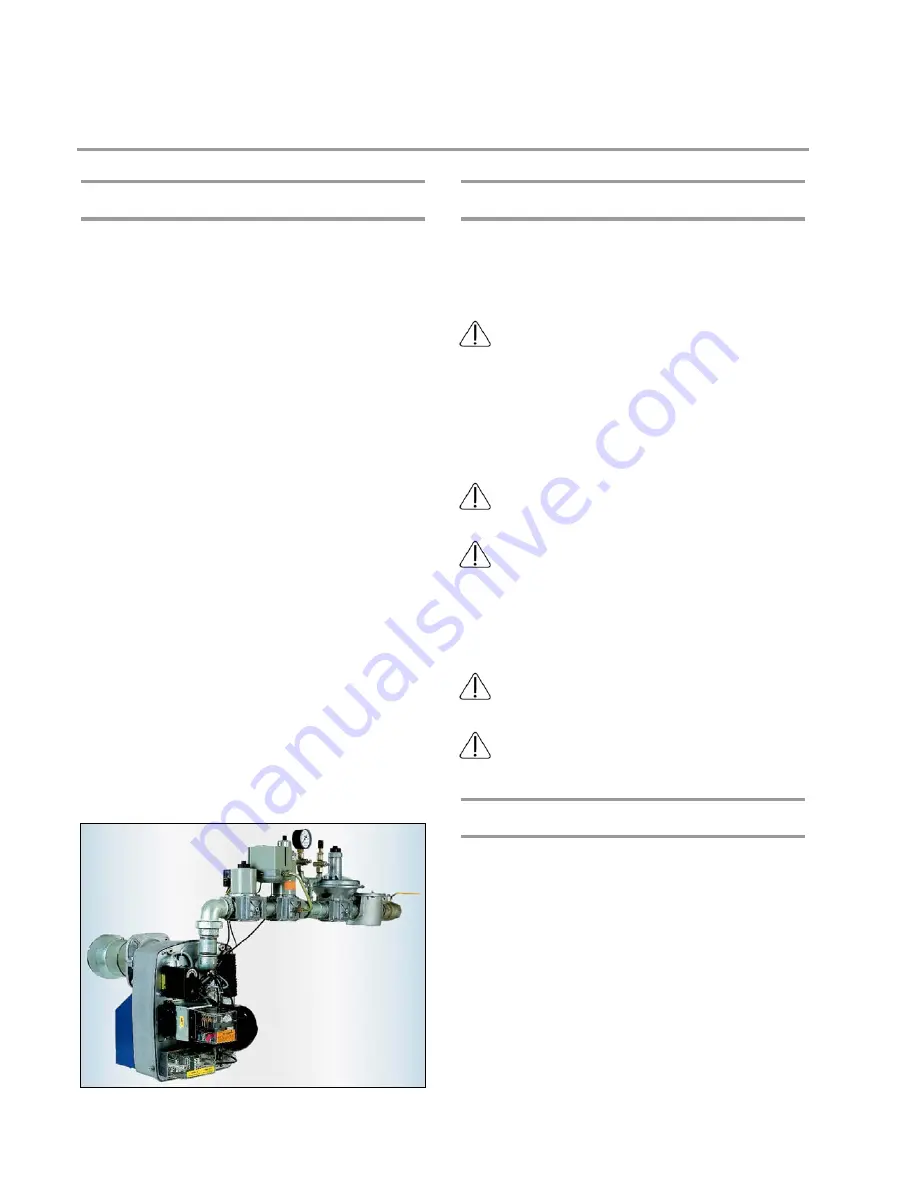
Installation-Operation-Maintenance
GZ 2 - GZ 4 / 100 - 1450 kW
6
Easy Installation
The burner comes complete, including power dependent
equipment, and every component is clearly designed so that a
qualified heating engineer will have no problems with Installa-
tion, starting, and servicing.
Screws and gaskets for the burner installation are included. The
burner is electrically connected by a 7-pole plug according to
DIN 4791.
The burners are pre-tested and pre-set. The burner performance
is changed by adjusting the gas-flow throttle and the settings
(dimension B and air damper position).
In Germany, the heating engineer has to consider the existing
regulations of the DVGW (e.g. TRGI or TRF) and the local utility
companies.
General note as per DIN EN 676:
This burner must be installed
in compliance with the valid specifications and must only be
operated in well aired rooms. The instructions before installing
and operating the burner must be observed.
The engineer must ensure that the heating room is suitably ven-
tilated with an air exchange rate of at least 100 m³/h. The gas
pipes must be installed and connected by an authorised heating
engineer. The weight of the gas compact ramps or assembly
must be supported by a suitable bracket.
The length of pipe between the gas ramps and the gas burner
must not exceed max. 800 mm (for GZ 2 and max. 500 mm for
GZ 3.0).
The VDE and EVU specifications must be observed when install-
ing the electrical connections.
The burner must be connected with a flexible cable. Do not in-
terchange the phase (live!) and neutral wires
As a result of the new master firing ordinance, some German
states stipulate the installation of thermally influenced gas stop
valves.
Fig. 4:
Gas-Gebläsebrenner GZ 3
Instructions for using the burner
The burners GZ 2 – GZ 4 are basically suitable for use in com-
mercially available heating boilers (intermittent operation) for
heating residential buildings and for service water. Product de-
velopment and the test procedures have been geared to the
operating conditions of these systems.
The areas of application listed below make particular
requirements with special operating conditions for
the burner, so that MHG Heiztechnik reserves the right to is-
sue explicit approval in these cases:
y
dark radiators
y
baking ovens
y
annealing furnaces
y
drying chambers
y
industrial applications
MHG Heiztechnik should also be consulted for instal-
lations with above average firing chamber or tem-
perature loads.
In the case of rooms where the air must be expected
to be contaminated by halogenated hydrocarbons,
e.g. hairdressers, printers, chemical dry cleaners, laborato-
ries etc., the burners must only be operated if suitable
measures are taken to ensure that there is an adequate sup-
ply of uncontaminated combustion air.
Always consult MHG Heiztechnik if in any doubt.
The burners must not be operated in rooms with high
dust levels or high humidity (e.g. laundries). The heat-
ing room must be protected from frost and well aired.
Failure to comply with these instructions renders the
warranty null and void for any damage resulting from
one of these causes.
Leak test
A programme-controlled leak detector which checks the sole-
noids for leaks can be installed simply and retroactively. An ad-
ditional electrical connection at gas compact ramps is not nec-
essary. The leak lest provides additional security for the users of
gas firing systems. This feature is generally recommended, and
is a stipulated-requirement for burner outputs of 1200 kW and
more.