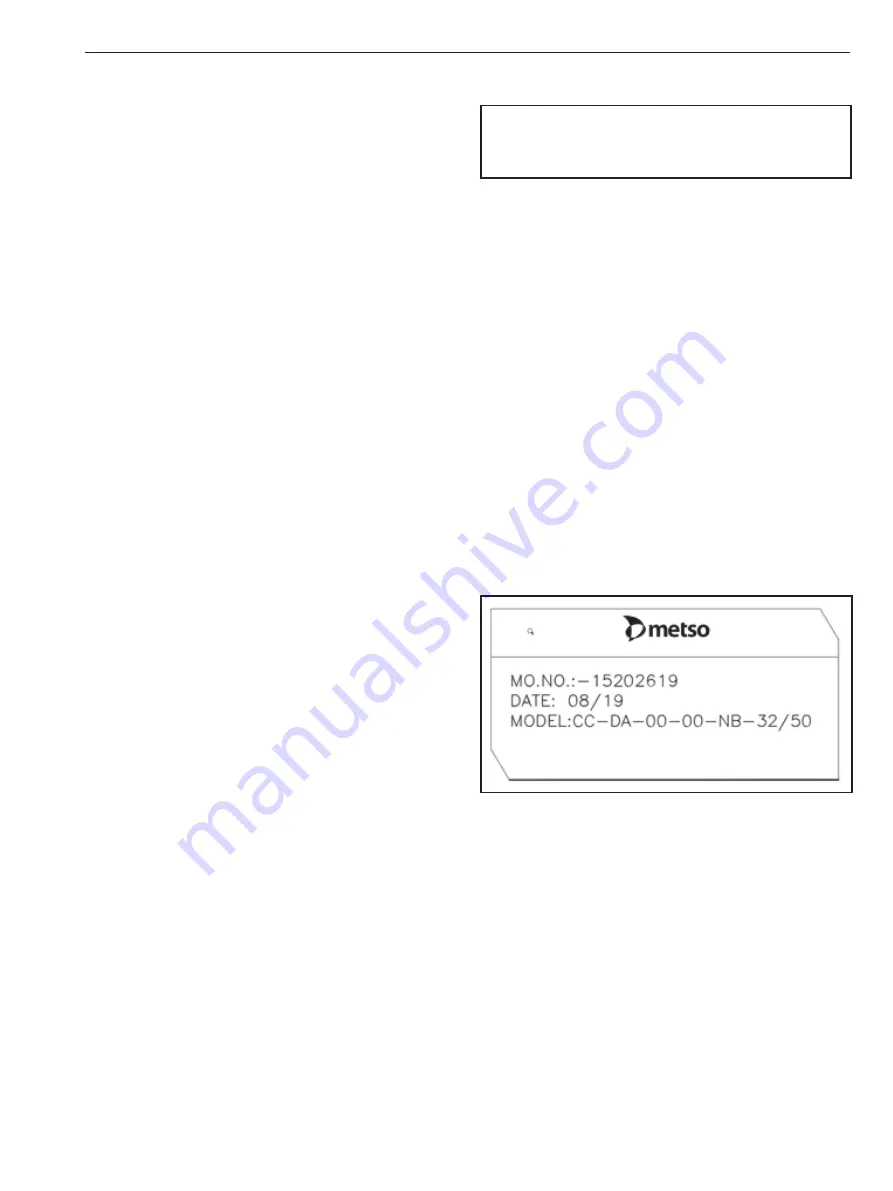
IMO 3/20
IMO-502 EN
3
1.
INTRODUCTION
Thank you for choosing METSO product. Each product
is fully inspected after the production to offer you the
highest quality. In order to fully utilize the product, we
strongly recommend users to read this manual carefully and
understood.
This manual provides information on installation, operation
and maintenance procedures and related instructions for
the RMEBS make pneumatic cylinder (CC series).
The aim of this literature is to support the use of products in
correct manner, and all the technical information provided
in the catalogue.
The manual should be given to the end user.
The manual can be changed or revised without any prior
notice. Any changes in product’s specification, structure,
and/or any components may not result immediate revised
version of the manual.
The manual should not be duplicated or reproduced for any
purpose without any consent of RMEBS Manufacturers &
Engineers Private Limited, INDIA.
Manufacturer Warranty
For the safety, it is vital to follow instructions in the manual.
It is not RMEBS’s liability for any damages which caused by
users’ negligence.
It is not RMEBS’s liability for any damages or accidents which
resulted by any alteration or modification of the product
and parts. If alteration or modification is necessary, please
contact the RMEBS directly.
RMEBS warrants the product from the date of original
retail purchase of the product for one (1) year, except as
otherwise stated.
RMEBS warranty will not cover the products that the
product have been subjected to abuse, accident, alteration,
modification, tampering, negligence, misuse, faulty
installation, lack of reasonable care, repair or service in any
way that is not contemplated in the documentation for the
product, or if the model or serial number has been altered,
tampered with, defaced or removed; damages that occurs
in shipment, failure due to power surge, and cosmetic
damage. Improper or incorrectly performed maintenance
or report voids this Limited Warranty.
For detailed warranty information, please contact :
RMEBS MANUFACTERURS & ENGINEERS PRIVATE LIMITED,
Manapada road, Dombivli (e), Maharashtra, India, Pin - 421204
1.1
Definitions
WARNING:
IF NOT OBSERVED, USER INCURS A HIGH RISK OF SEVERE DAMAGE
TO PRODUCT AND/OR FATAL INJURY TO PERSONNEL.
CAUTION: IF NOT OBSERVED, USER MAY INCUR DAMAGE
TO PRODUCT AND/OR INJURY TO PERSONNEL.
NOTE: Advisory and information comments provided to assist
maintenance personnel to carry out maintenance procedures.
2.
OPERATION PRINCIPAL
Pneumatic cylinder is a mechanical device which uses power
of compressed air/gas to produce a force in a reciprocating
linear motion.
The basic pneumatic cylinder consists of a cylindrical chamber
with a movable piston and intake and exhaust channels.
Compressed air or other gas is supplied into the cylindrical
chamber. This pressurized air/gas exerts force against the
base of the piston, which causes piston to move, providing
a way to move other mechanical elements.
3.
LABEL DESCRIPTION
Label of the cylinder defines the precise feature of that
particular cylinder. This description is written below the
METSO logo and is as follow.
M.O. NO.:
Manufacturing order number
DATE:
Date of manufacturing
Model no.: CC – Type
DA – Double acting cylinder
00 – standard MOC of piston rod
00 – Standard model
NB – Piston diameter 350 mm
32 – Stroke length 250 mm
50 – Stroke length 250 mm
Summary of Contents for JAMESBURY CC Series
Page 11: ...IMO 3 20 IMO 502 EN 11 ...