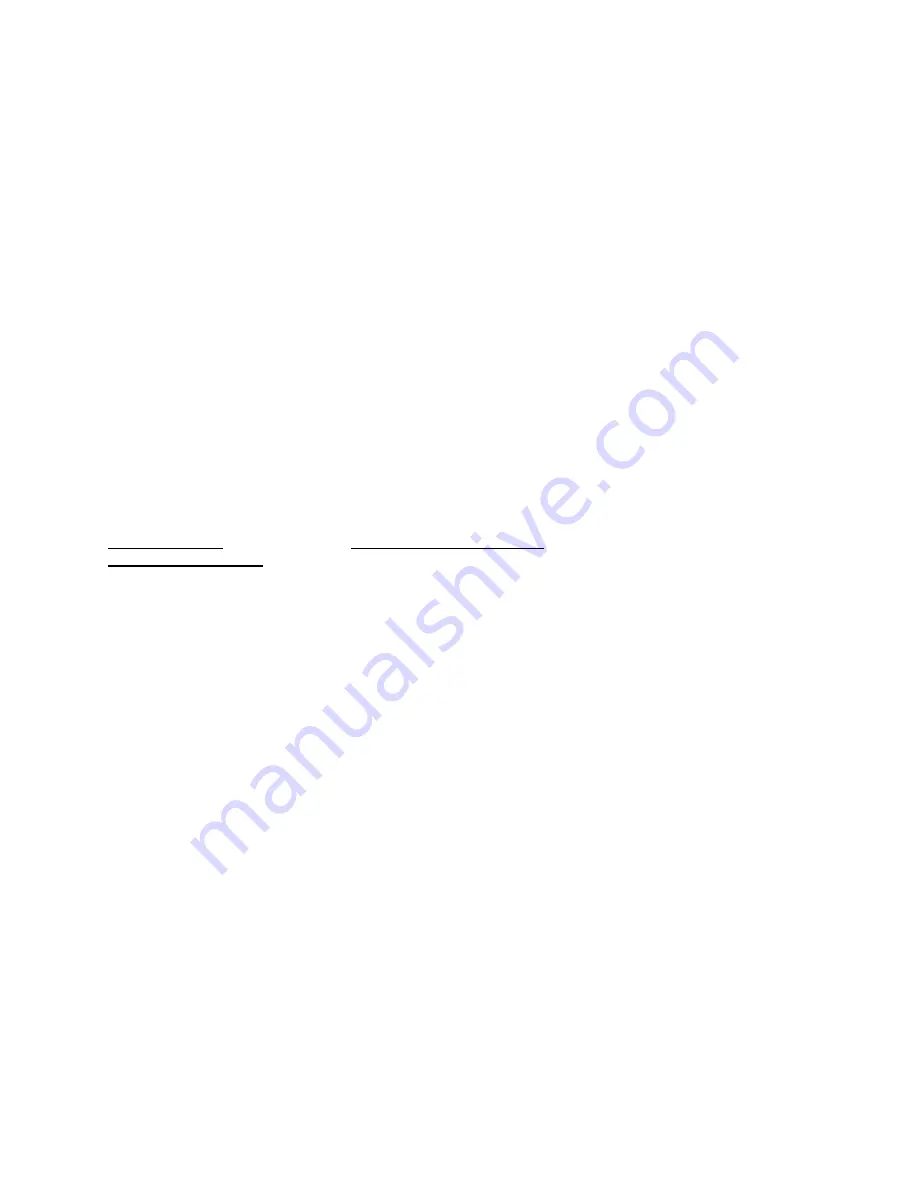
Page 6 of 34
File Name:
Doc#586p.docx
wire must be wired from the grounding lug in the controller to earth ground. In most cases, the engine manufacturer furnishes
the engines with all accessories installed and wired to the connection box. Therefore, it is only necessary to wire from the
engine connection box to like numbered terminals in the Controller. Note proper wire sizes. All wires must be stranded.
A drain valve is provided to relieve water pressure to the pressure switch, thus closing the pressure switch contacts and starting
the engine. This test simulates an actual start demand. Since the Controller operates the drain valve only momentarily, a small
amount of water is drained off. The water pressure sensing line to the Controller from the pump must be thoroughly flushed
before connection to the Controller in order to remove chips, particles, or other matter, that could enter the plumbing
components in the Controller.
Controllers configured with
"Automatic Stop"
enabled may be changed to
"Manual"
stop by disabling this feature in System
Config Screen 104. If deluge valve switches are to be used for starting, enable the Deluge Valve Option in Config Screen 121
and connect the remote normally closed switch to terminals 31 and 111.
B.
TEST PROCEDURE
All of the following tests should be made on each unit after installation. If each test is satisfactory, the operator may place the
control switch in
"Auto"
mode and depend upon the panel operating properly when required. Also, any one or all of these tests
may be carried out at any time after installation, if so desired.
NOTE: If 115 Volts A.C. is not connected to Controller, the
"Charger Failure" lights and “AC Power Loss” light and alarm will be activated and if the Power Failure Start feature
(System Config Screen 111) is enabled, the controller will start automatically. The 115VAC must be turned ON to
prevent the engine from starting.
ENGINE TERMINAL (terminals 1-12) STATUS INDICATOR LIGHTS
Light Emitting Diodes (L.E.D.) lights have been installed on the microprocessor module to indicate the status of each engine
terminal. Status indication is given below:
Terminal Number
L.E.D. (light) "ON" Indication
(Microprocessor Func #)
1 (Out 06)
Power available to fuel and water solenoids
2 (In 06)
Speed switch has operated into engine running mode
3 (In 07)
Speed switch has operated into overspeed mode
4 (In 08)
Oil Pressure switch contacts closed (Low Oil Pressure)
5 (In 09)
Water temperature switch contacts closed (High Engine Temp.)
6 (In 01)
Battery #1 voltage present
8 (In 02)
Battery #2 voltage present
9 (Out 02)
Crank #1 voltage present (while cranking on Battery #1)
10 (Out 03)
Crank #2 voltage present (while cranking on Battery #2)
12 (Out 07)
Energize to stop voltage present
a.
BATTERY LOCKOUT TEST:
1.
Turn on Battery #1 switch and Battery #2 switch.
2.
Press the
"Reset"
button. Battery #1 and Battery #2 Healthy lights should be on.
3.
Turn Battery #1 switch off for a couple of seconds and back on. Battery #1 light should go off and remain off.
4.
Press
"Reset"
button. Battery #1 light should come on.
5.
Repeat for Battery #2.
b.
CRANKING CYCLE TEST:
This test simulates a condition where the engine refuses to start.
1.
Disconnect Terminal No.1 on Controller panel.
NOTE: Disconnecting Terminal No.1 is for the purpose of
removing power from the fuel solenoid so engine will not start. On engines where the fuel solenoid is not used
(Caterpillar), or is connected other than through Terminal #1 (Clarke-G.M.), other means must be used to
stop fuel flow to the engine to prevent starting.
2.
Press the
"Test"
mode button to start cranking the engine. Time the crank and rest periods, and count the number of
cranks. There should be six (6) crank periods separated by five (5) rest periods each of approximately 15-seconds