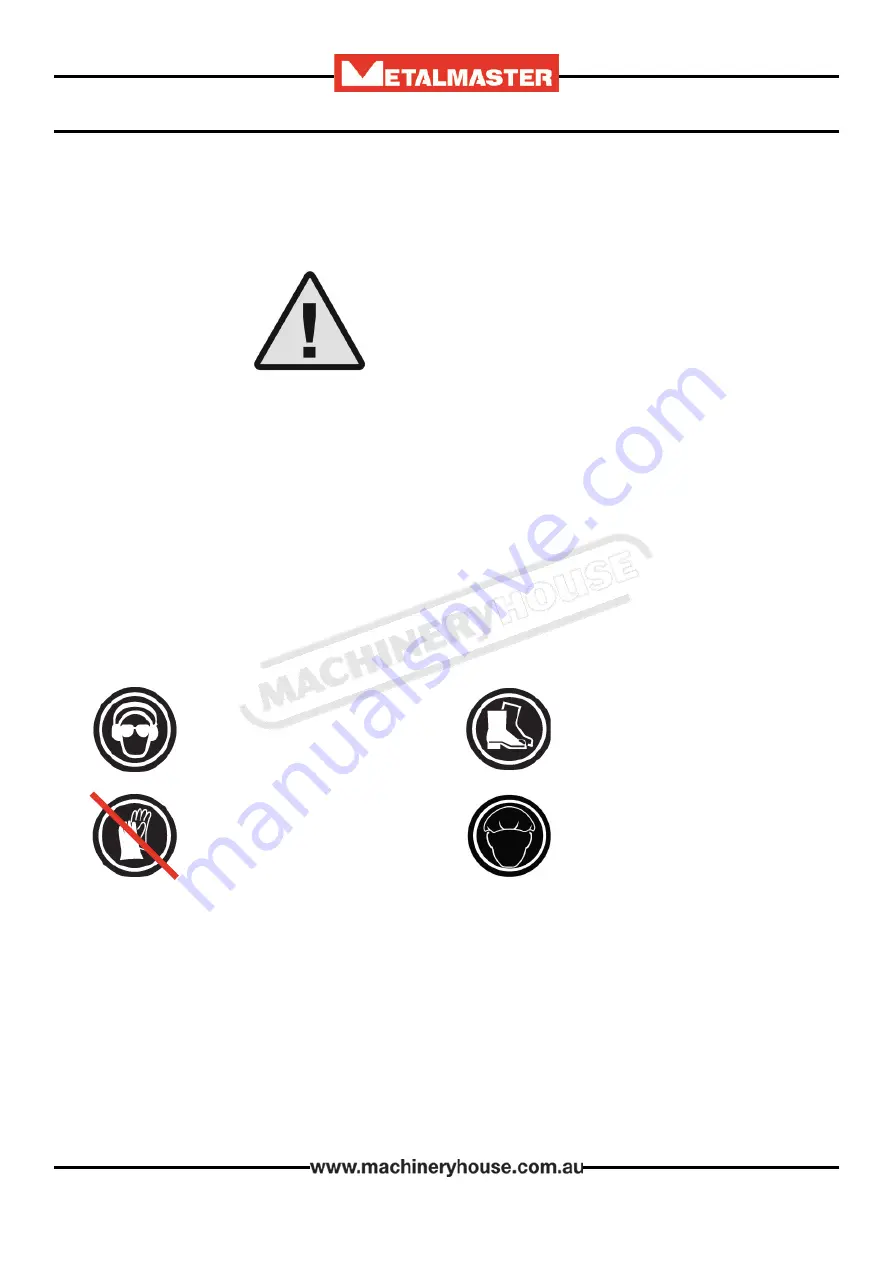
5
OPERATION MANUAL
2.1 SAFETY REQUIREMENTS
DO NOT use this machine unless you have read this manual or have been instructed in the use
of this machine in its safe use and operation
Safety glasses must be worn at
all times in work areas. Earmuffs
should be worn if the work area is
noisy.
Sturdy footwear must be worn
at all times in work areas.
Gloves should NOT be worn when
using this machine
Long and loose hair must be
contained with a net or under a
hat
This manual provides safety instructions on the proper setup, operation, maintenance, and
service of this machine. Save this manual, refer to it often, and use it to instruct other operators.
Failure to read, understand and follow the instructions in this manual may result in fire or
serious personal injury—including amputation, electrocution, or death.
The owner of this machine is solely responsible for its safe use. This responsibility includes, but
is not limited to proper installation in a safe environment, personnel training and authorization
to use, proper inspection and maintenance, manual availability and comprehension, of the
application of the safety devices, integrity, and the use of personal protective equipment.
The manufacturer will not be held liable for injury or property damage from negligence,
improper training, machine modifications or misuse.
WARNING
DISCONNECT POWER FIRST.
If using power,
always disconnect the machine from power sup-
ply before making adjustments, or servicing the
machine. This prevents any risk of injury from
unintended startup or contact with live
electrical equipment
OWNER’S MANUAL.
Read and understand this
owner’s manual before using the machine.
TRAINED OPERATORS ONLY.
Operators that
have not been trained have a higher risk of
being seriously injured. Only allow trained or
supervised people to use this machine. When
the machine is not being used, disconnect the
power, to the machine to prevent unautho-
rized use—especially around children. Make
the workshop safe.
06/01/2020
Instructions Manual for SJ-24D (S641)
5