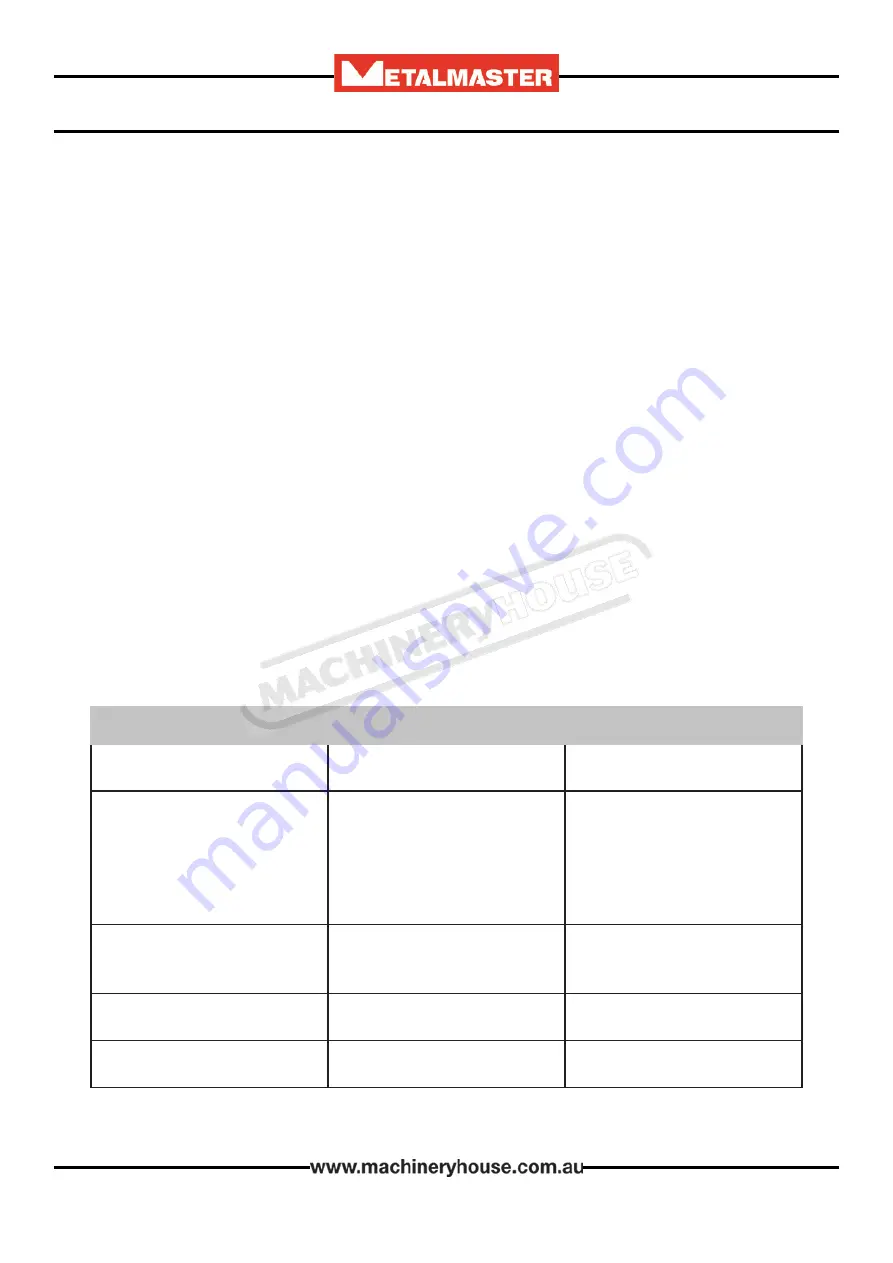
16
OPERATION MANUAL
5. MAINTENANCE
• A visual inspection must be made before each use of the press, checking for leaking
hydraulic fluid and damaged, loose, or missing parts.
• Owners and/or users should be aware that repair of this equipment requires specialized
knowledge and facilities. It is recommended that a thorough annual inspection of the press
be made and that any defective parts be replaced with genuine Metalmaster parts.
• Any press which appears to be damaged in any way, is found to be badly worn, or operates
abnormally SHOULD BE REMOVED FROM SERVICE until the necessary repairs are made.
• If the press is not to be used for any length of time, store it with the ram retracted and the
operating handle in the lowered position to protect the moving parts.
5.1 INSPECTION SCHEDULE
• Check the press frame to make sure all bolts are tight and inspect for cracked welds, bent,
loose or missing parts.
• Check the hydraulic connections for leaks. Replace or properly repair any damaged or
leaking hydraulic components before using. In the event of leaking seals, oil can be topped
up via the plug on the end of the pump. Oil should be level with the bottom of the hole. If
necessary top up with hydraulic oil, This task is carried out with the ram fully retracted.
• If any rust is apparent it must be removed completely and the paint restored
Problem
Probable Cause
Remedy
Pump unit will not work
Dirt on the valve seat/worn
seals
Bleed pump unit or have unit
overhauled with new seals
Pump will not produce
pressure. Pump feels hesitant
under load. Pump will not
lower completely
Air-lock
Open the release valve and
remove the oil filler plug.
Pump the handle a couple
of full strokes and close the
release valve.
Replace the filler plug.
Pump will not deliver
pressure
Reservoir could be overfilled
or have low oil level
Check oil level by removing
the filler plug and topping up
to the correct level.
Pump feels hesitant under
load
Pump cup seal could be worn
out
Have the cup seal replaced.
Pump will not lower
completely
Air-lock
Release air by removing the
filler plug
5.2 TROUBLESHOOTING