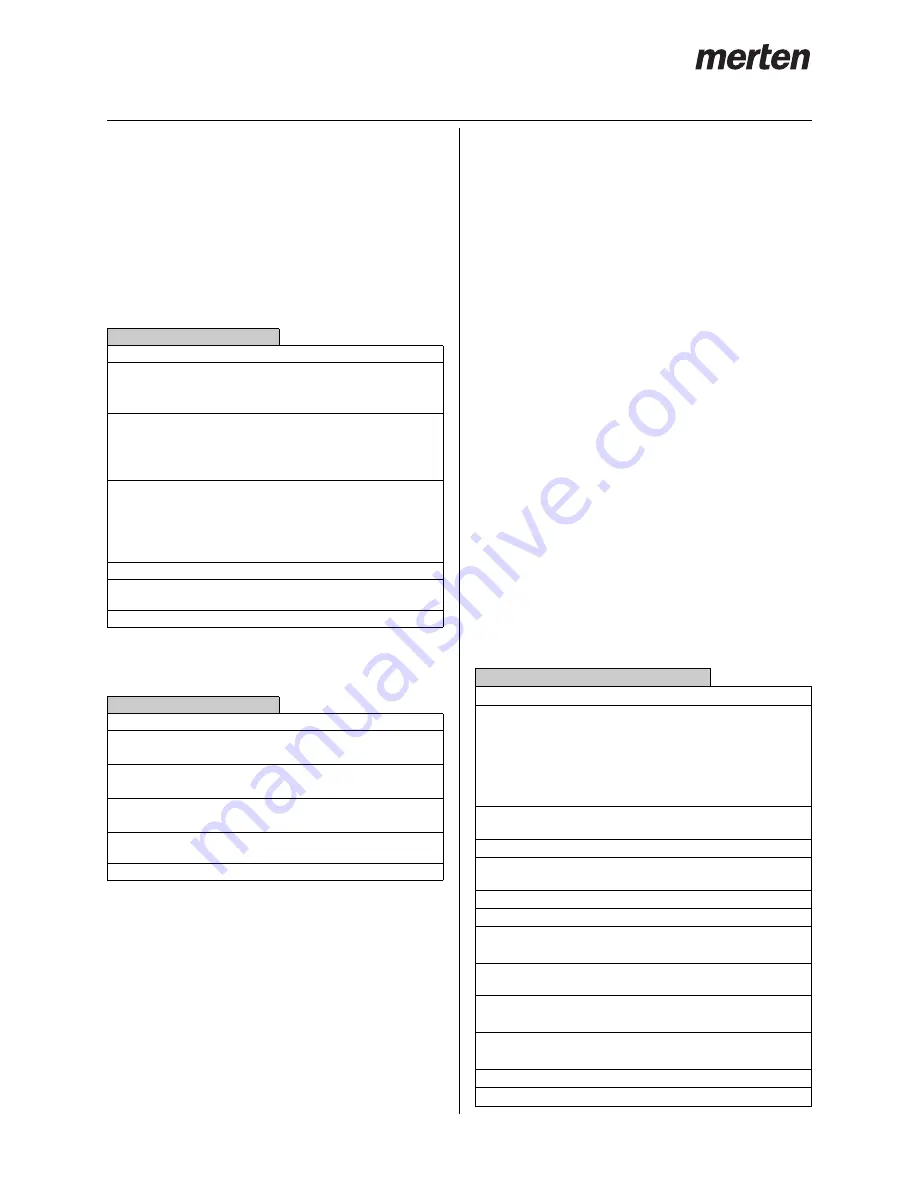
44
© 2009 Merten by Schneider Electric
Push-button, 4-gang plus with room temperature control unit and IR receiver
Multifunction with RTCU and FanCoil 1817/1.0
Getting to know and parameterising the room temperature control unit
Set control cooling and additional level
This tab only appears if you set the "cooling" or "heating
and cooling" control type in the "Control general" tab.
Here, you can set which cooling control type should be
activated. For PI controls, you can select between three
standard system types, for which the recommended
parameters have already been preconfigured. Howev-
er, if you have sufficient specialised knowledge, you
can also set the control parameters as required.
For 2-step control, set the hysteresis here.
Here, specify the settings for the second cooling level.
Set correcting variables and valve protection
Note that you need to set different parameters for
2-step control than you do for a PI control.
For "Cycle time of switching correcting variable", set the
duration for the PI control. The calculated correcting
variable is always transmitted at the start of a cycle time.
If the valve drive has not received a value (e.g. during
commissioning), the room could continuously heat up
or cool down. To prevent this, set the "Cycle time for au-
tomatic sending of correcting variable". The correcting
variable is transmitted again within the set time (as a
precaution).
|
The minimum correcting variable must always be
smaller than the maximum correcting variable! If
not, the message "Er 4" appears on the display.
Valve protection
Valve protection prevents the valves on the heaters be-
coming stuck due to deposits in the heating water when
the heating is switched off for a longer period of time
(e.g. over the summer). When the valve protection is
switched on, the valves are opened for a preset dura-
tion (100% on the controller output) after a preset
number of days, and are then closed again (0% on the
controller output).
The following settings apply for the "Heating" and
"Cooling" controller types:
Control cooling
Parameter
Setting
Basic level
Direction of the controller
Normal
Inverted
Correcting variable output
PI control (switching)
PI control (continuous)
2-step control (switching)
2-step control (continuous)
Select cooling system
Adjustment via control parame-
ter
Air convector (4 K/90 min)
Split unit (4 K/90 min)
Cooling ceiling (5 K/240 min)
Hysteresis
0.3 K - 2.0 K,
0.5 K
Proportional range for cooling in
0.1 K (10-255)
10 - 255,
40
Reset time for cooling (1-255 min)
No
, 1 - 255
Control heating
Parameter
Setting
Use additional level
Yes
No
Direction of the controller
Normal
Inverted
Correcting variable output
2-step control (switching)
2-step control (continuous)
Interval
Factor (10 ... 100) * 0.1 K
10 ... 100,
20
Hysteresis
0.3 K - 2.0 K,
0.5 K
Correcting variables
Parameter
Setting
Basic level
Select a minimum correcting variable that is
smaller than the maximum correcting variable.
Cycle time of switching correcting variable
(2-60 min)
2-60,
15
Range of minimum correcting variable from
0 % to ... %
0 % - 100 %,
30 %
Minimum correcting variable (0 % - 100 %)
0 % - 100 %,
30 %
Range of maximum correcting variable from
100 % to ... %
0 % - 100 %,
70 %
Maximum correcting variable (100 % - 0%)
0 % - 100 %,
70 %
Change for which correcting variable is sent
2 % - 10 %,
3 %
Send correcting variable cyclically
Yes
No
Cycle time for automatic sending of correcting
variable in min (1-60)
1-60,
30
Send inactive correcting variable cyclically
Yes
No
Use valve protection
Yes
No
Activate valve protection every ... days (1 - 30) 1-30,
15
Approach end position for ... min (1-30)
1-30,
4