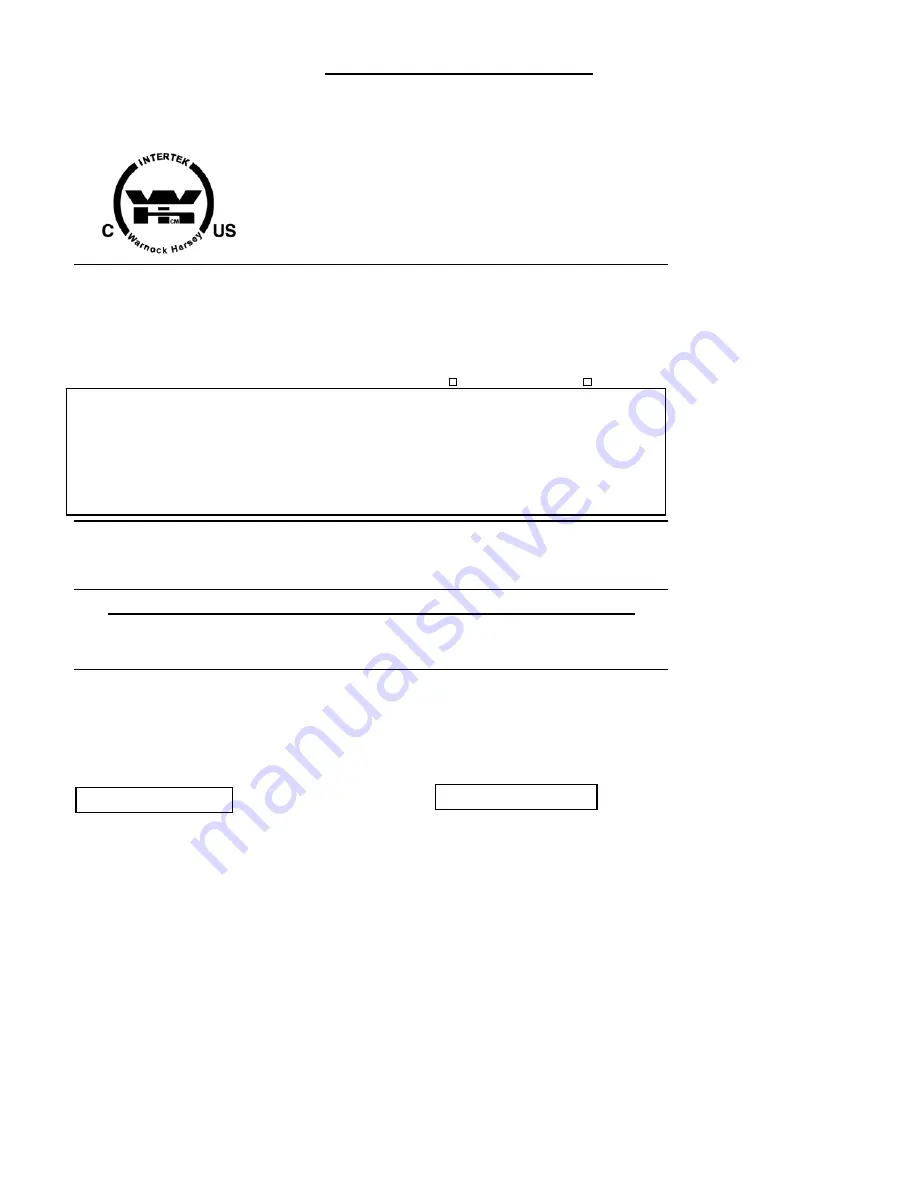
- 60 -
LISTING LABEL INFORMATION
The model information regarding your specific appliance can be found on the rating plate, which is located inside the right
side controls access door. When contacting your dealer for any cleaning service or warranty service, always provide the
Model Number, Serial Number and Manufactured Date. This information will expedite the warranty verification process.
WARNING: IMPROPER INSTALLATION, ADJUSTMENT, ALTERATION, SERVICE OR MAINTENANCE CAN CAUSE PROPERTY DAMAGE,
PERSONAL INJURY, OR LOSS OF LIFE. REFER TO THE OWNER’S INFORMATION MANUAL PROVIDED WITH THIS APPLIANCE.
INSTALLATION AND SERVICE MUST BE PERFORMED BY A QUALIFIED INSTALLER. DO NOT OPERATE WITH GLASS DOOR REMOVED,
CRACKED, OR BROKEN. THIS VENTED GAS FIREPLACE HEATER IS NOT FOR USE WITH AIR FILTERS. REGISTER KIT MAY BE USED.
MISE EN GARDE: INSTALLATION, RÉGLAGE, MODIFICATION, ENTRETIEN OU DÉPANNAGE NON APPROPRIÉS POURRONT CAUSER
DES BLESSURES OU DES DOMMAGES MATÉRIELS. RÉFÉREZ-VOUS AU MANUEL DU PROPRIÉTAIRE FOURNI AVAC CET APPARIEL. POUR
ASSISTANCE OU RENSEIGNEMENTS COMPLÉMENTAIRES, VEUILLEZ CONSULTER UN INSTALLATEUR EXPÉRIMENTÉ, UNE AGENCE DÉ
DÉPANNAGE/ENTRETIEN OU COTRE COMPAGNIE GAZIERE, POUR UTILISATION AVEC LES PORTES EN VERRE CERTIFIÉE L’APPAREIL
LISTED DIRECT VENT GAS FIREPLACE HEATER
(POELE AU GAZ HOMOLOGUÉ, À AÉRATION DIRECTE)
NOT FOR USE WITH SOLID FUEL
(NE DOIT PASÉ UTILISÉ AVEC UN COMBUSIBLE SOLIDE)
MANUFACTURED BY (FABRIQUÉ PAR):
JOHNSON GAS APPLIANCE CO. CEDAR RAPIDS, IOWA
CERTIFIED FOR CANADA HOMOLOGUE POUR LE CANADA
TESTED TO (TESTÉ AUX NORMES)
ANSI Z21.88-2002 * CSA 2.33-2002
MINIMUM CLEARANCES TO COMBUSTIBLE CONSTRUCTION
UNIT TO FLOOR
0in. (0 mm)
GLASS EDGE TO ADJACENT SIDEWALL
18in. (457 mm)
UNIT TO ENCLOSURE SIDEWALL
0in. (0 mm)
VENT PIPE TOP TO COMBUSTIBLES
2in. (51 mm)
UNIT TO ENCLOSURE BACK WALL
1in. (25 mm)
VENT PIPE SIDES TO COMBUSTIBLES
1in. (0 mm)
UNIT BOTTOM TO ENCLOSURE CEILING
47-9/16 in. (121 mm)
VENT PIPE BOTTOM TO COMBUSTIBLES
1in. (0 mm)
UNIT BOTTOM TO ROOM CEILING
72in. (1829 mm)
7-1/2” MANTLE ABOVE DISCHARGE AIR OPENING
15in. (368 mm)
THIS APPLIANCE IS ONLY FOR USE WITH THE TYPE OF GAS INDICATED ON THE RATING PLATE AND MAY BE INSTALLED IN AN
AFTERMARKET, PERMANENTLY LOCATED MANUFACTURED (MOBILE) HOME WHERE NOT PROHIBITED BY LOCAL CODES. SEE OWNER’S
MANUAL FOR DETAILS. THIS APPLIANCE IS SUPPLIED WITH A CONVERSION KIT.
CET APPAREIL SERA INSTALLÉ CONFORMÉMÉNT AVEC LES CODES LOCAUX, LE CAS ÉCHÉANT. SI AUCUN CODE
N’EXISTÉ, SUIVEZ LA NORME ANSI Z223.1 OULA NORME CAN/CGA (ACNOR)-B149.
NATURAL GAS
LP GAS
(GAZ NATUREL)
(GAS DE PÉTROLE)
LIQUÉFIÉ
(GPL))
INPUT RATING (BTR/HR) 0-610m (ENTREÉ NOMINALE)
50,000
50,000
MIN. INPUT RATING (BTU/HR) 0-610m (MINIMALE ENTRÉE NOMINALE)
15,800
16,200
ORIFICE 0-610m (ORIFICE)
FRONT #35 REAR #43
FRONT #51 REAR #54
ORIFICE 610-1370m (ORIFICE)
FRONT #36 REAR #44
FRONT #52 REAR #55
INPUT RATING (BTU/HR) 610-1370m
26,200
23,800
MAXIMUM OUTPUT (BTU/HR) (SORTIE MAXIMALE)
21,060
19,500
MANIFOLD PRESSURE (in. w.c./kPa) (PRESSION AU COLLECTEUR)
3.5
10.0
MANIFOLD PRESSURE, LOW (in. w.c./kPa) (PRESSION D’ENTRÉE MINIMALE)
1.3
3.3
MINIMUM INLET PRESSURE (in. w.c./kPa) (PRESSION D’ENTRÉE MINIMALE)
5.0
11.0
CAUTION: HOT WHILE IN OPERATION. DO NOT TOUCH. KEEP CHILDREN, CLOTHING, FURNITURE, AND FLAMMABLE LIQUIDS OR VAPORS
AWAY.
ATTENTION: L’APPAREIL EST CHAUD LORSQU’IL FONCTIONNE. NE PASS TOUCHER L’APPAREIL. SURVIELLER LES ENFANTS. GARDER LES
VÊTEMENTS, LES MEUBLES, L’ESSENCE OU AUTRES LIQUIDES À VAPEUR INFLAMMABLES LOIN DE L’APPAREIL.
ELECTRICAL RATING (COURANT NOMINAL): 120 VOLTS 60 HERTZ LESS THAN 1.5 AMPERES
65-01-000310
DO NOT REMOVE OR COVER THIS LABEL
VEILLEZ A NE JAMES ENLEVER NI DISSIMULER CETTE ÉTIQUETTE
MODEL: M-50
SERIAL NO.
MFG. DATE:
Summary of Contents for GREENBRIAR M-50
Page 52: ...52 BURNER FLAMES GENERAL HEIGHT DIAGRAM...
Page 58: ...58 SCALE 3 4 DETAIL A Figure 43 VALVE ASSEMBLY...
Page 63: ...63 NOTES...
Page 64: ...64 NOTES...
Page 65: ...65 NOTES...
Page 66: ...66 NOTES...