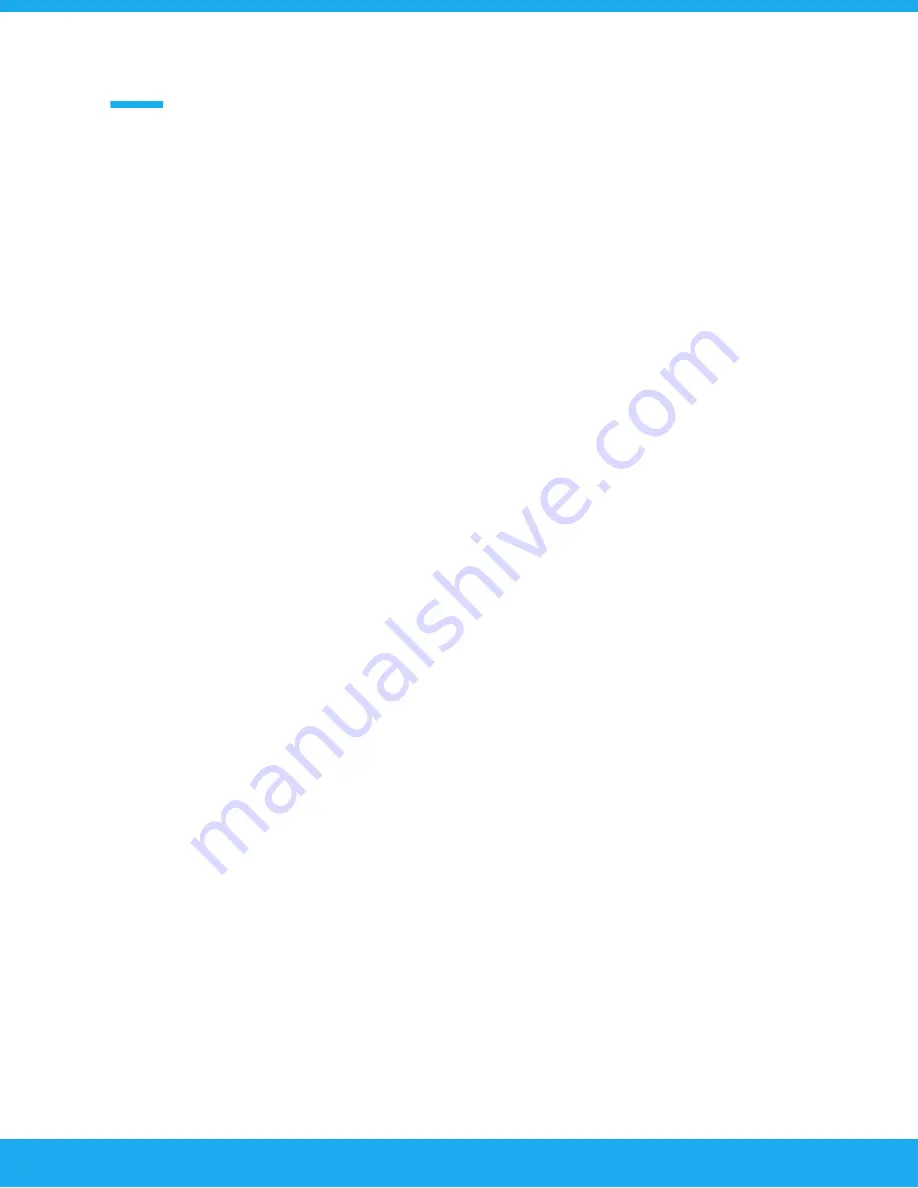
Table of contents
1. Introduction
2. I/O and pinout
3. Wiring
a. Crimping the connector pins
b. Assembling the connector
4. Wiring diagrams
a. Power and CAN-bus
b. Accelerator pedal
c. Throttlebody
5. Updating the controller
6. Understanding fault codes
a. ARM fault codes
b. AVR fault codes
7. PID Settings
a. Operating modes
b. Throttlebody specific settings
8. Configuring fault output
9. Step by step initial configuration guide
a. Setting up DBW throttle to MegaSquirt 3
Trademark Legal Notice
. All product names, trademarks and registered trademarks are property
of their respective owners. All company, product and service names used in this document are
for identification purposes only. Use of these names,trademarks and brands does not imply
endorsement.
1