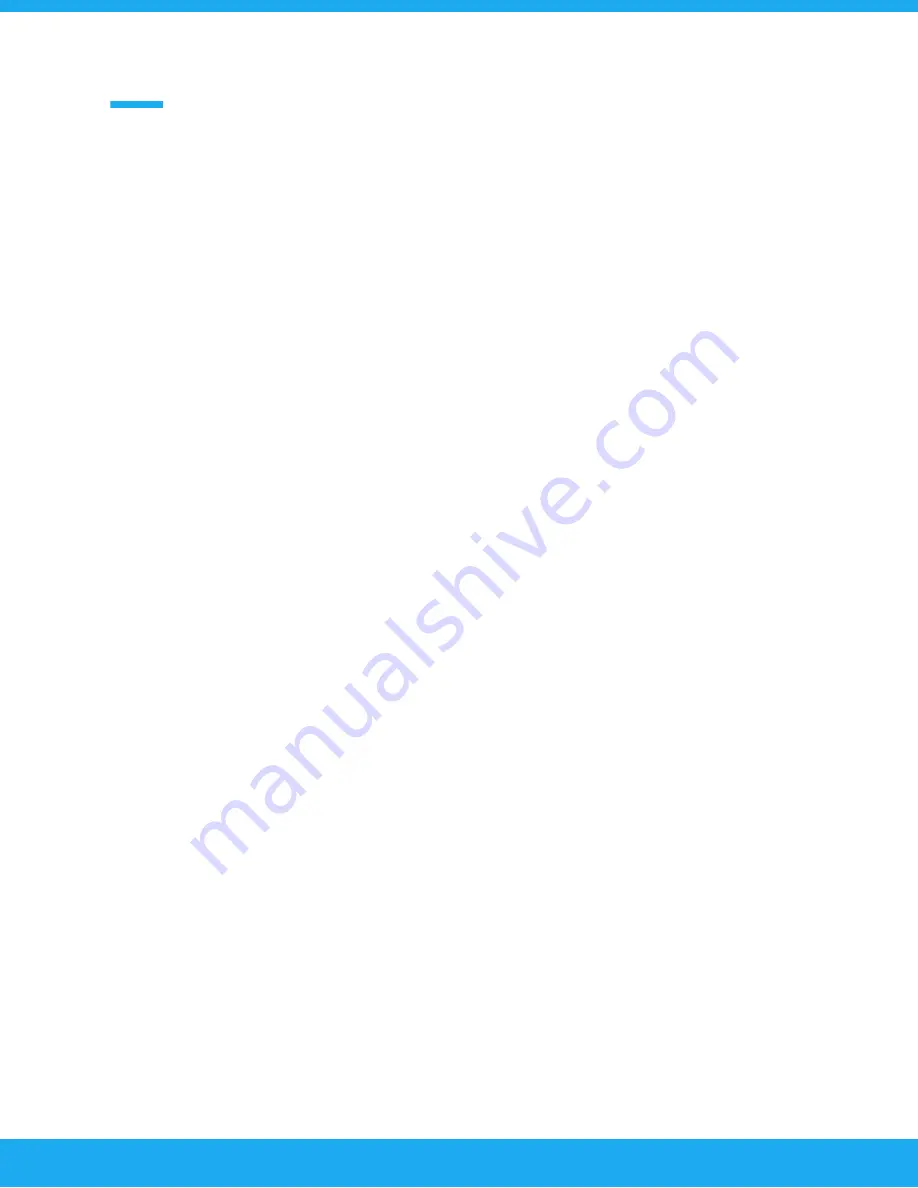
sensor difference will a fault be triggered. Default value is 4%
H-Bridge current sense enable: This setting enables the current sense circuitry in the H-Bride.
This circuitry is around 15% accuracy from full scale (30A). This means that it cannot be used for
precision measurement, but it can measure relative changes in current. Enabling this will enable
logging of the current and the current gauge. If this setting is disabled the current gauge will
display 0A.
Update I/D: This is the PID controller update frequency.
PID I MIN: Often referred as “deadband”. The PID integrator is paused when the position error is
smaller than what is set.
I MAX: To prevent PID controller integrator windup this setting can be used to reset the integrator
to 0 when position error is larger that set value. To disable this put in 100%.
PID clamp settings:
This setting can limit the maximum PID calculation outputs. The PID controllers internal register
are logged, and can be viewed from the logs. These values will clamp the calculated values to
the set values.
BIAS
The DBW controller also has a table that is called either “bias” or “feed forward” table. This is
basically an open loop of the control strategy. We have found that a well tuned PID control may
not need this table at all, but it is provided. The “bias” value is a duty cycle value that is given to
the DBW throttlebody for a given “target” opening. The dytycyle can be from -100 to +100.
Negative values driving the butterfly closed and vice versa.
Throttle body sensor calibration
The position sensors of the DBW throttlebody are calibrated automatically by the controller. User
needs to disable AVR protection from the AVR fault code menu. Then press “Calibrate” button
and the controller will drive the butterfly first fully open and the fully closed and records the
sensor readings. This works only for regular DBW throttlebodys that have linear sensors.
16