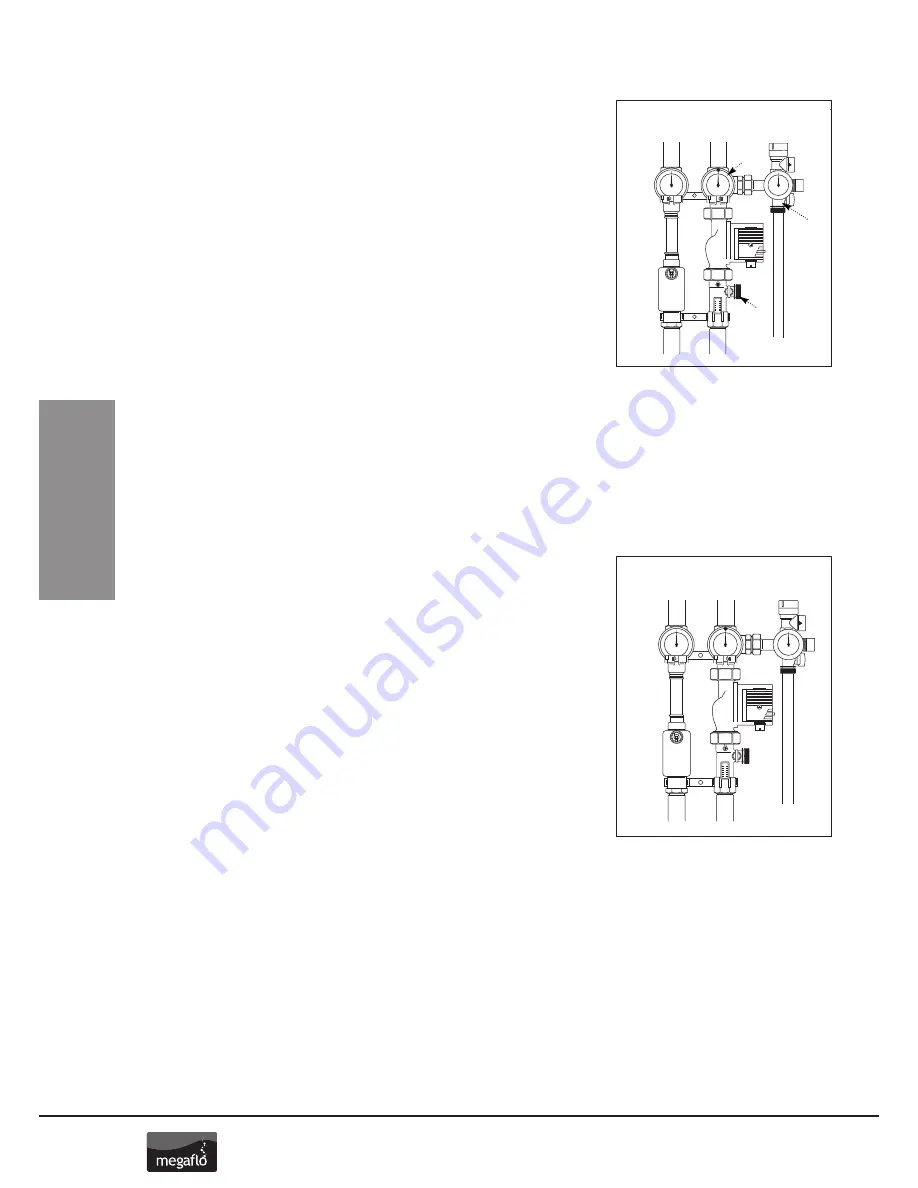
COMMISSIONING
24
Close the fill and drain valve - safety group (Fig. 19 Item 1)
and the fill and drain valve - flow meter (Fig. 19 Item 2) and pressurise the pump
slightly prior to filling the system. If an electric pump is being used follow the
instructions with the pump.
Fully open the fill and drain valve on the safety group (Fig 19, item 1) and pump
fluid into the system. Whilst pumping, open the flow meter drain valve (Fig 19,
item 2) slightly to allow the air to vent out of the system.
When the pump is down to approximately 1 litre isolate the fill and drain valves.
Vent the filling pump and refill with solar heat transfer fluid.
Re-pressurise the filling pump and repeat the steps above until fluid is seen
discharging from the drain valve on the flow meter. (Fig 19, item 2). Close the
drain valve.
Continue filling at the fill and drain valve on the safety group (Fig 19, item 1) until
the system pressure reaches 2 bar.
At this point the circulation pump should be vented. If the system pressure drops,
repressurise using the procedure above.
After venting the pump and checking that the system pressure is 2 bar, close the
fill and drain valve on the safety group (Fig. 19 Item 1), and check the system for
leaks.
Turn the left hand isolating valve (Fig 19, item 4) back 45° clockwise until the dot
on the bezel is back at 12 o’clock.
Turn the right hand isolating valve (Fig. 19 Item 5) back 90° clockwise until the dot
on the bezel is back at 12 o’clock.
Turn the slot of the adjusting screw (Fig. 19 Item 3) back to the horizontal position.
Commissioning of hydraulic station
Ensure the solar primary system is free from air
Switch on the power supply to the solar differential temperature controller.
Manually switch the circulation pump ON and OFF via the solar differential
temperature controller (see section 11.5) to pump fluid around the solar primary
system.
Turn the pump off and open the airbleed screw on the air separator
(Fig. 22 Item 1).
Bleed any air from the air separator.
If the system pressure drops top up by opening the fill and drain valve
(Fig. 27 Item 2) on the safety group and pumping in more solar fluid to restore
the pressure. This must be repeated until the pressure remains stable.
Setting the system pressure
During commissioning, the system pressure should be 0.7 bar above the static
pressure (1 metre height differential equals 0.1 bar). However, it must be at least
1.5 bar and no higher than 2.2 bar.
Determine the system pressure when the system is cold (20°C). This should be
recorded on the Commissioning Record Sheet.
If the pressure is too low you should pump additional heat transfer fluid into the
system; the fill & drain valve on the safety group (Fig. 22 Item 2) needs to be
opened for this purpose. When system pressure is correctly set, ensure the fill and
drain valve is closed and remove filling hose from safety group.
24
© Baxi Heating UK 2012
10.0
Commissioning of hydraulic station
10.1
Ensure the solar primary system is free from air
1. Switch on the power supply to the solar differential
temperature controller.
2. Manually switch the circulation pump ON and OFF via the
solar differential temperature controller (see section 11.5) to
pump fluid around the solar primary system.
3. Turn the pump off and open the airbleed screw on the air
separator (Fig. 27 Item 1). Bleed any air from the air separator.
If the system pressure drops top up by opening the fill and
drain valve (Fig. 27 Item 2) on the safety group and pumping in
more solar fluid to restore the pressure. This must be repeated
until the pressure remains stable.
10.2
Setting the system pressure
1. During commissioning, the system pressure should be 0.7
bar above the static pressure (1 metre height differential
equals 0.1 bar). However, it must be at least 1.5 bar and no
higher than 2.2 bar.
2. Determine the system pressure when the system is cold
(20°C). This should be recorded on the Commissioning
Record Sheet.
3. If the pressure is too low you should pump additional heat
transfer fluid into the system; the fill & drain valve on the safety
group (Fig. 27 Item 2) needs to be opened for this purpose.
When system pressure is correctly set, ensure the fill and drain
valve is closed and remove filling hose from safety group.
Fig. 27
1
2
17
© Baxi Heating UK 2012
8.0
Commissioning of system
8.1
Air Test
1. An air test may be used on the pipework to detect any gross
leakage prior to flushing and filling with solar heat transfer fluid.
Pressurise the system to a maximum of 1 bar to check for leaks.
2. Ensure that the solar expansion vessel pre-charge pressure
has been set prior to flushing and filling.
8.2
Flushing and Filling the pipework
1. Before the system is commissioned the pipework must be
flushed to remove any contaminants.
This must be done using
the solar heat transfer fluid as it will be impossible to fully
drain all parts of the system.
2. Connect the flushing pipes to the fill & drain valve on the
safety group (Fig. 19 Item 1) and to the fill & drain valve on the
flow meter (Fig. 19 Item 2).
3. Open the fill & drain valves.
4. Turn the slot of the adjusting screw (Fig. 19 Item 3) in the
return so the slot is vertical to open the non-return valve.
5. Turn the left hand isolating valve with integral thermometer in
the flow (Fig. 19 Item 4) in the direction indicated by the arrow
(to a 45° position) to open the non-return valve.
6. Ensure that the right hand isolating valve with integral
thermometer in the return (Fig. 19 Item 5) is open indicated by
the dot on the thermometer bezel being at the top.
7. Turn the slot of the flow meter adjusting screw (Fig. 19 Item
6) in the return vertically to open the flow limiter (Fig. 19 Item
7).
8. Flush the solar primary pump by pumping the fluid into the
system via the fill and drain valve on the safety group (Fig. 19
Item 1).
9. Close right hand isolating valve (dot on thermometer bezel at
9 o’clock position). Flush solar primary pipework and collector
via the fill and drain valve on the safety group.
If reusing flushed
fluid ensure this is filtered before re-introducing into the
system.
(see Fig. 20). Use a suitable container of a large enough
volume to collect the fluid.
10. When satisfied that all pipework and component parts have
been thoroughly flushed, the system can be filled.
4
5
3
6
7
Fig. 19
Fig. 20
Fig. 21
Solar fluid
Filling pump
Filter
1
2
1
3
2
45°
Read at top
of float
Figure 21
Figure 22
Summary of Contents for Eco SolaReady
Page 1: ...Hot Water Cylinders MEGAFLO Eco SolaReady Unvented MEGAFLO Eco SolaReady Product Guide...
Page 48: ...SERVICING 48...
Page 50: ...SERVICING 50...
Page 51: ...SERVICING 51 Notes...