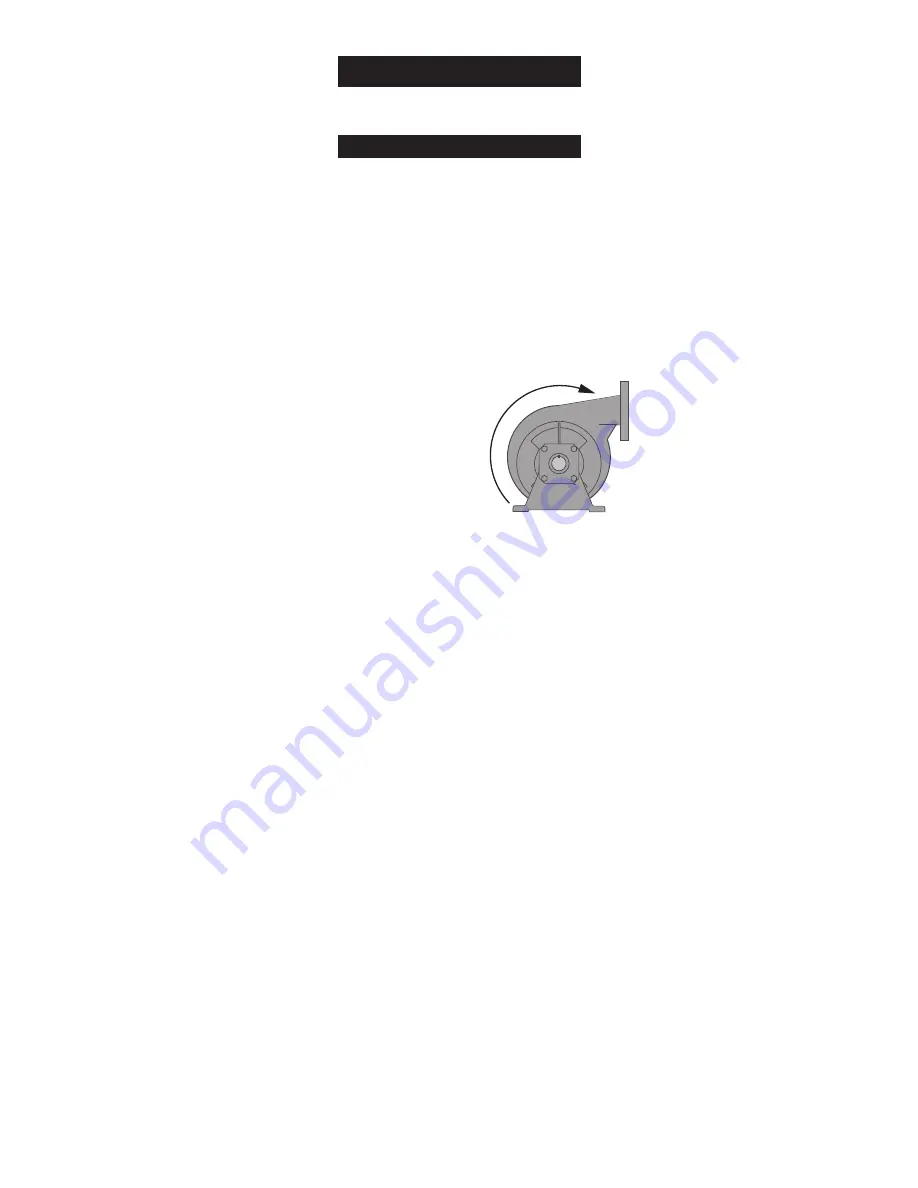
Page 8
General Information
Start-up
C
lo
ck
w
ise
ro
tatio
n
12
6
3
9
6588 0712
PIPING
System piping should be at least one commercial pipe
size larger than pump connections and flow velocity
should not exceed eight (8) feet per second. Suction and
discharge pipes must be naturally aligned with pump
connections.
NOTICE Misalignment of piping with pump case or
excessive pipe strain can cause distortion of pump
components resulting in rubbing, breakage and reduced
pump life.
Insure that piping is supported in a manner that prevents
the exertion of force on pump connections. This can be
checked by the following procedure. With the pump shut
down, remove pipe flange bolts. If the mating flanges
come apart or shift, misalignment is present and causing
pressure on the connections. Adjust pipe supports until
flanges mate without any force. This procedure can be
done throughout piping system.
LUBRICATION
LIQUID END of pump requires no lubrication. Wear
rings, packing rings, and models using a mechanical
shaft seal are lubricated by the liquid being pumped. Do
not run dry!
BEARING FRAME
General maintenance - add approximately 5.5 ounces
(150cc) of a lithium-based NGLI No. 2 extra pressure ball
bearing grease to the outboard bearing and 2.5 ounces
(75 cc) to the inboard bearing every 90 days.
NOTICE Excess grease will cause bearings to run hot.
The following are factory approved brands of grease for
use with Mega Pumps: Alvania EP2, Shell Oil;
Mobilith AW2, Mobil Oil, Ronex MP, Exxon, Litholine
EP2, Atlantic Richfield; and Amolith EP2, Amoco.
PRIMING
Pump priming is the displacement of air with water
in the pump and suction piping. Pump
MUST BE
completely filled with water when operating.
HYDRAULIC BALANCED PUMPS
Hydraulic balanced pumps operate with a very low
positive pressure across the stuffing box, permitting a
much looser fit of the packing rings around the shaft
sleeve to control the loss of water from the pump
through the stuffing box.
PUMP PRIMING
INSTALLATION WITH FLOODED SUCTION
• Open air vent (or pipe plug) in the highest tapped
opening in pump case.
• Open inlet isolation valve, allowing water to fill the
pump completely and force all air out through vent.
• Rotate shaft slowly allowing any air trapped in
impeller to escape.
• Close vent opening when water without air emerges.
CHECk ROTATION
Before pump is put into operation, rotational direction
must be checked to assure proper performance of
pump. Refer to
FIGURE 3.
STARTING
NOTICE Never run pump dry. Running pump without
water will overheat pump and damage internal parts.
Always make sure pump is primed prior to start-up.
NOTICE
Refer to maintenance section if pump has
packing for adjustment prior to start-up.
Set discharge valve to minimum flow. Turn on power to
pump. Slowly open discharge valve until desired flow
rate is achieved.
PACkING
Starting new pump. Before starting pump for the first
time, loosen gland nuts and retighten finger tight.
Proceed with pump start-up procedure. Allow packing to
leak liberally for a few moments. Then tighten gland nuts
one complete turn each until leakage is reduced to 40 to
60 drops per minute.
STOPPING
Pump will stop automatically when the flow to the driver
motor stops. If hydraulic shock occurs, the check valve
closure rate may need adjustment or additional controls
may be needed.
FIGURE 3