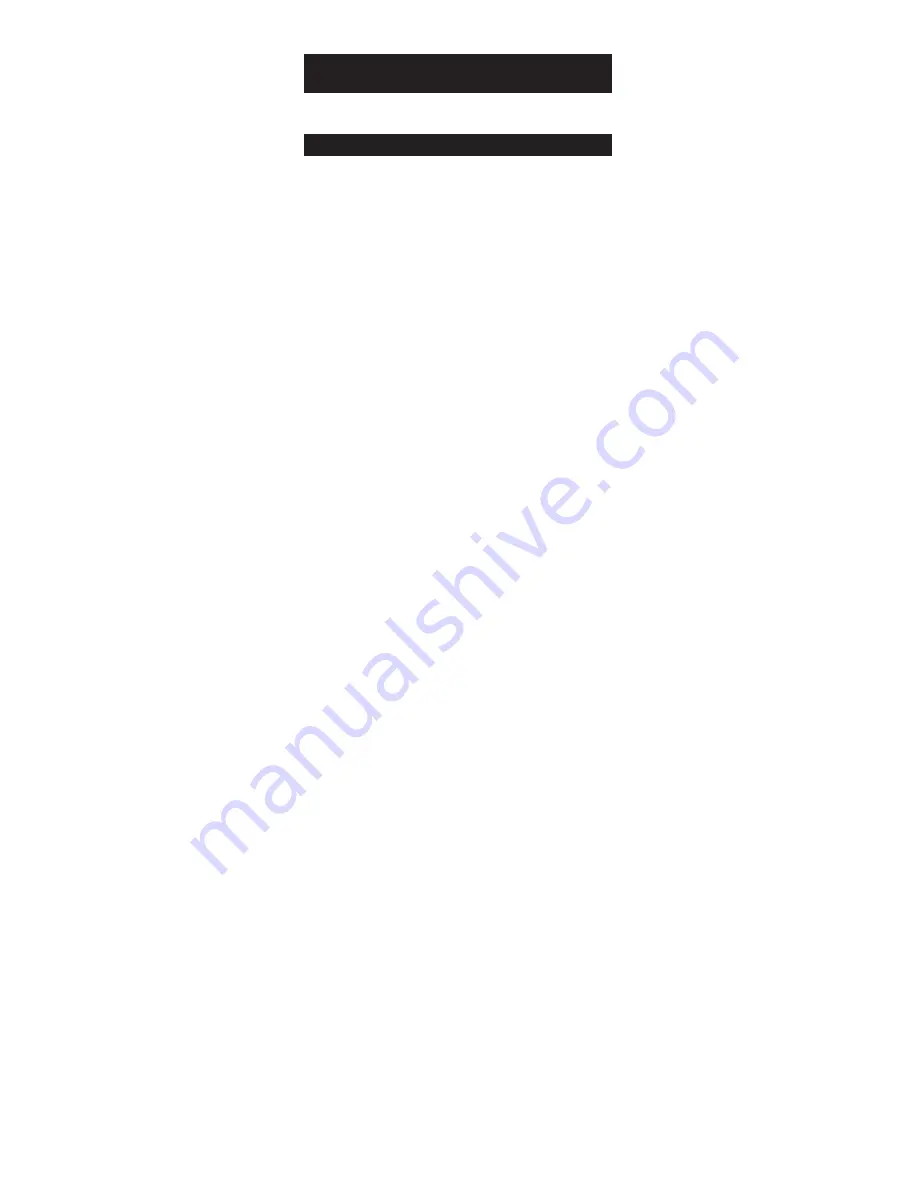
Page 4
F00637
General Information
Transport and Storage
TRANSPORT AND STORAGE
TRANSPORT AND HANDLING REqUIREMENTS The
pump has been prepared for shipment at the factory
in such a way as to minimize potential damage due to
handling and transport.
RIGGING AND LIFTING
The following instructions
are for the safe handling of the pump. When shipment
is received extreme care should be exercised during
unloading. Heavy parts should be skidded to the
ground if lifting equipment is not available. It is
recommended a forklift be used to unload equipment.
Bare pump: Using a nylon sling, chain, or wire rope,
hitch around both the inboard and outboard bearing
housings. Size the equipment for the load, and so the
lift angle will be less than 45° from the vertical.
RECEIPT, INSPECTION, AND DAMAGE
REPORTING
Immediately upon receipt of the pump
equipment, carefully check to see that all items have
been received and are in undamaged condition.
Report any shortage or damage to the transport
company handling the shipment and to the equipment
manufacturer, noting the extent of damage or shortage
on the freight bill and bill of lading. This should be done
at once. Do not unpack any more than required to
verify that the equipment is complete and undamaged
unless installation is to be done immediately. Do not
leave the pump unit or any accessories exposed to
weather or construction hazards, which may cause
damage to the equipment.
SHORT-TERM STORAGE
The pump and equipment,
as shipped, have adequate protection for short-term
(up to three months) storage in a covered, dry, and
ventilated location prior to installation.
LONG-TERM STORAGE
If the equipment will be
subject to extended (more than three months) storage
prior to installation and commissioning, then the
standard warranty of the equipment may be affected.
Periodic rotation of the pump and driver shaft is
recommended during long-term storage (consult the
equipment manufacturer as to the frequency), and
inspection of the equipment by a factory representative
prior to start-up is normally required to ensure
equipment integrity and compliance with warranty
requirements.
• Remove and discard stuffing-box packing. Fill the
stuffing box with a crusting grease (Rust-Ban 326
or equal), then pack the end of the stuffing box with
rolled vapor phase inhibitor paper and seal with
weatherproof tape.
• Dry pump internals and spray the liquid end with a
water-displacement rust inhibitor (Rust-Ban 392,
Crown 6011, Arma 245, Ensis fluid 254, Sunkote
1303, or equal).
• Enclose vapor inhibitor in pump internals (Shell VPI
260 or equal).
• Apply a film of compatible lube oil over the water-
displacement rust preventative. A compatible lube oil
is Rust-Ban 632 or equivalent.
• After the pump has been thoroughly drained, cover
the pump suction and discharge flanges with full
gasket material and blank off these openings with
metal blank flanges and a minimum of four full-
sized bolts. Cover the pump stuffing-box opening
with a nonhygroscopic tape. If packed-type pump,
the packing gland may be left on the pump shaft,
but should be wired or otherwise securely fastened
in position. If mechanical seals have been used,
then the annular opening between seal plate and
shaft should be closed by a nonhygroscopic tape to
exclude airborne dust.
• All exposed machined surfaces should be thoroughly
coated with a firm film rust-preventative material
(Rust-Ban 373, CRC-SP-350, Enis fluid 264, Protec
612801, or equal) that is readily removable with a
petroleum distillate product.
• All exposed painted surfaces should be dry, clean,
and free of grease and other contaminates.
• The pump should be covered with a weather-
resistant cover of waterproof paper or plastic to
prohibit the buildup of dirt and dust accumulations.
• The pump should be inspected at regular periods
during storage, and the pump shaft should be rotated
by hand at intervals of approximately four to six
weeks.
• To place the pump in operation, all protective
coverings and coatings should be properly removed.
If packed type pump, then repack with the proper
number of packing rings in each stuffing box in
accordance with normal repair and maintenance
instructions furnished with the pump.
• Rotate pump shaft several revolutions at least once
per week to coat the bearing with lubricant and
to retard oxidation and corrosion, flat spots, and
staining.
• Long-term storage procedures should be followed as
detailed by the OEM when the start-up of equipment
is made over three months from the date of shipment
from the factory.