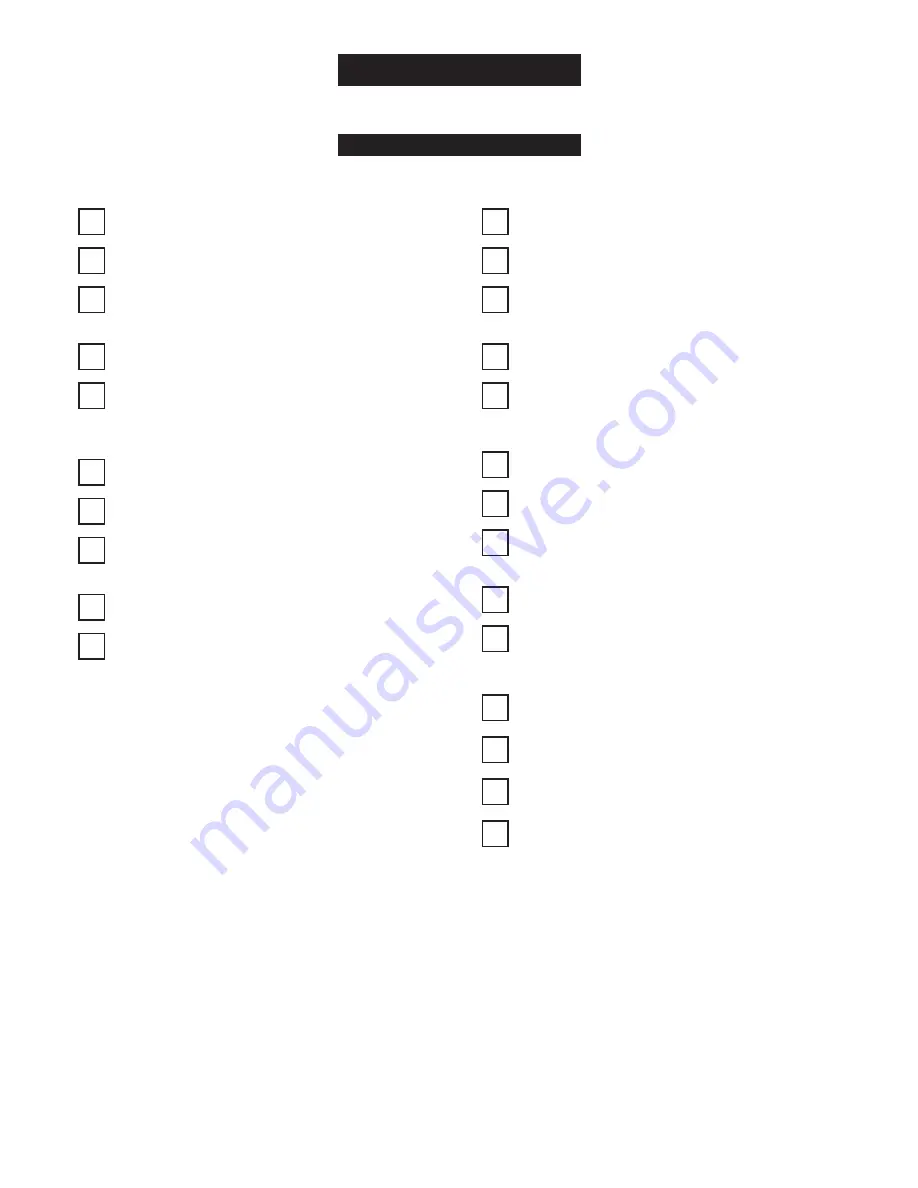
Page 10
1. qUARTERLY INSPECTION
Inspect all system piping connections for leakage
or possible misalignment.
Complete any lubrication requirements as
dictated by pump and driver owner’s manual.
Inspect packing or mechanical seal for possible
replacement. Examine shaft sleeve, if present, for
wear and replace if necessary.
Check pump and driver bearings for signs of
wear. Repack or replace as necessary.
_______________________________________
2. qUARTERLY INSPECTION
Inspect all system piping connections for leakage
or possible misalignment.
Complete any lubrication requirements as
dictated by pump and driver owner’s manual.
Inspect packing or mechanical seal for possible
replacement. Examine shaft sleeve, if present, for
wear and replace if necessary.
Check pump and driver bearings from signs of
wear. Repack or replace as necessary.
_______________________________________
NOTES:
3. qUARTERLY INSPECTION
Inspect all system piping connections for leakage
or possible misalignment.
Complete any lubrication requirements as
dictated by pump and driver owner’s manual.
Inspect packing or mechanical seal for possible
replacement. Examine shaft sleeve, if present, for
wear and replace if necessary.
Check pump and driver bearings for signs of
wear. Repack or replace as necessary.
_______________________________________
4. qUARTERLY INSPECTION
Inspect all system piping connections for leakage
or possible misalignment.
Complete any lubrication requirements as
dictated by pump and driver owner’s manual.
Inspect packing or mechanical seal for possible
replacement. Examine shaft sleeve, if present, for
wear and replace if necessary.
Check pump and driver bearings for signs of
wear. Repack or replace as necessary.
_______________________________________
5. ANNUAL INSPECTION
Inspect pump and entire pumping system for
signs of wear.
Inspect system valves, screens, etc.
Check pump impeller eye for clearance.
Inspect impeller, volute case, and seal chamber
for signs of excessive wear or corrosion.
Routine Inspection
Maintenance
Record