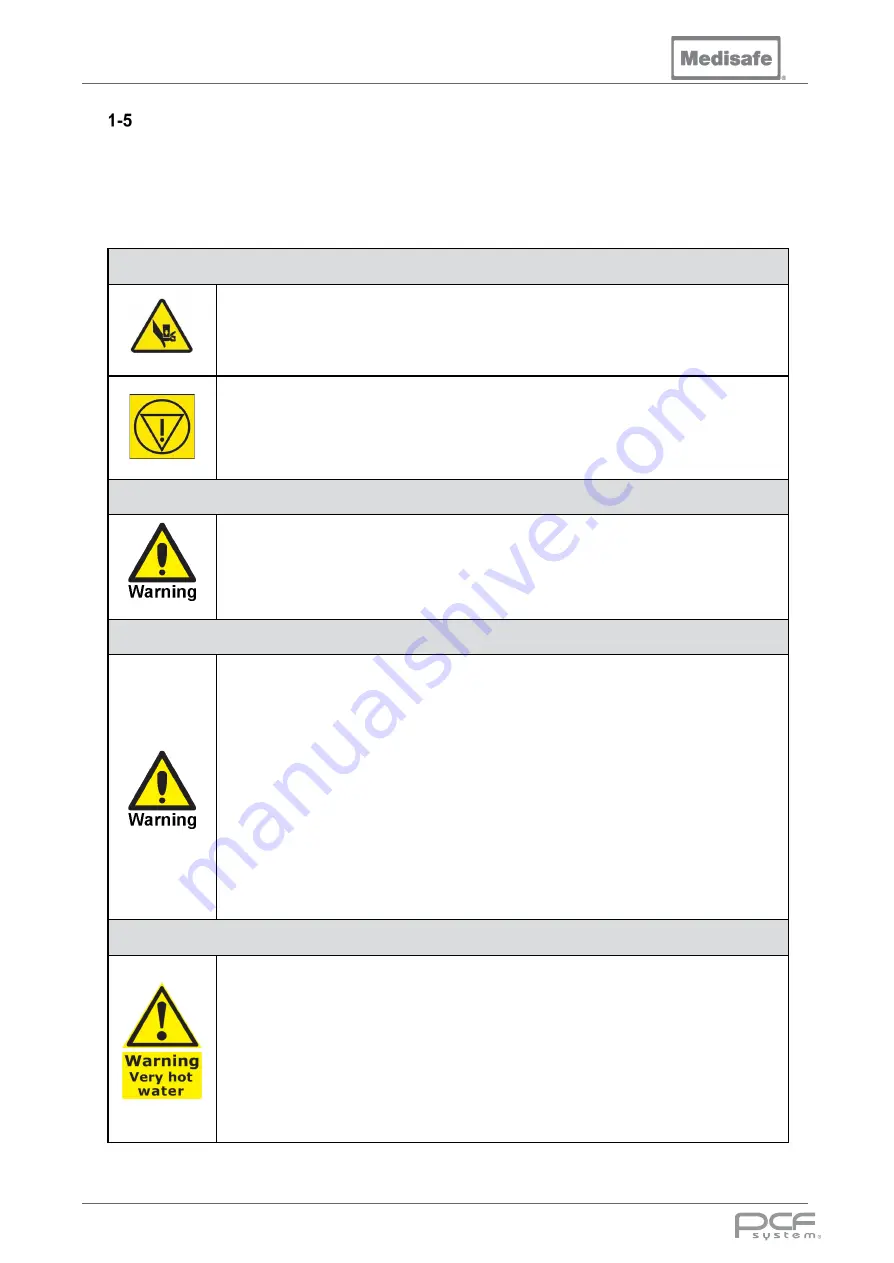
PCF Pro User Manual
DOC01851
Page 12 of 74
Safety Precautions
The following
Safety Precautions
must
be observed when operating or servicing the PCF Pro.
WARNING indicates the potential for personal injury and CAUTION indicates the potential for damage
to equipment. For emphasis, certain
Safety Precautions
are repeated throughout the manual.
It is
important to review ALL
Safety Precautions
before operating or servicing the unit
.
Warning – Pinching Hazard
Pinch points are created during lid articulation. Keep hands clear when opening or
closing the lid.
In the unlikely event of an uncontrolled fault, the emergency stop button can be
pushed to cut power for the Carrier Lift and other critical outputs.
Warning – Breathing Hazard
Some cleaning solutions emit harmful vapours. Only use cleaning solutions in well-
ventilated areas. Do not inhale vapours. Do not permit solution vapours to exceed
maximum allowable concentrations in the work area. Ensure adequate ventilation.
Warning – Chemical Burn and/or Eye Injury Hazard
•
Detergents are caustic and can cause adverse effects to exposed tissues. Do
not get in eyes, on skin or attempt to ingest by mouth.
•
Read and follow precautions and instructions on detergent label and in the
Material Safety Data Sheet (MSDS) prior to handling chemical, refilling chemical
containers or servicing chemical injection pumps and lines.
•
Wear appropriate Personal Protective Equipment (PPE) whenever handling
chemicals or servicing chemical injection pumps and lines. This should include
plastic gloves, goggles or full-face visor, and disposable plastic apron.
•
Wear appropriate Personal Protective Equipment (PPE) whenever removing
baskets or parts from cleaning chamber.
•
In case of body contact with chemical, always follow emergency procedure given
in that chemical’s MSDS or call emergency services.
•
Use a funnel when transferring any chemical from one container to another.
Warning – Burn Hazard
•
Since temperatures within the unit can reach 92°C (198°F) during and after
operation, take care when opening lid at the end of a cycle. Allow sufficient time
for items to cool before handling, cleaning or maintenance procedures.
•
Wear appropriate Personal Protective Equipment (PPE) whenever reaching into
Chamber after a thermal disinfection operation.
•
Under no circumstances attempt to forcibly open the lid during operation.
•
During reloading of instruments in the re-wash program the water temperature
within the unit can reach 60°C (140°F), when opening the lid and reloading the
instruments take care and wear appropriate PPE.
Summary of Contents for PCF Pro
Page 1: ...DOC01851 PCF Pro User Manual...
Page 7: ...DOC01851 Page 7 of 74 1 Introduction 1 Introduction User Manual...
Page 19: ...DOC01851 Page 19 of 74 2 Installation 2 Installation User Manual...
Page 26: ...PCF Pro User Manual DOC01851 Page 26 of 74 Installation Drawings Rear View Showing Services...
Page 27: ...PCF Pro User Manual DOC01851 Page 27 of 74 Front View...
Page 29: ...PCF Pro User Manual DOC01851 Page 29 of 74 Left Side View Lid Open...
Page 31: ...DOC01851 Page 31 of 74 3 Operation 3 Operation User Manual...
Page 55: ...DOC01851 Page 55 of 74 4 Troubleshooting 4 Troubleshooting User Manual...
Page 59: ...DOC01851 Page 59 of 74 5 Technical 5 Technical User Manual...
Page 65: ...DOC01851 Page 65 of 74 6 Appendices 6 Appendices User Manual...