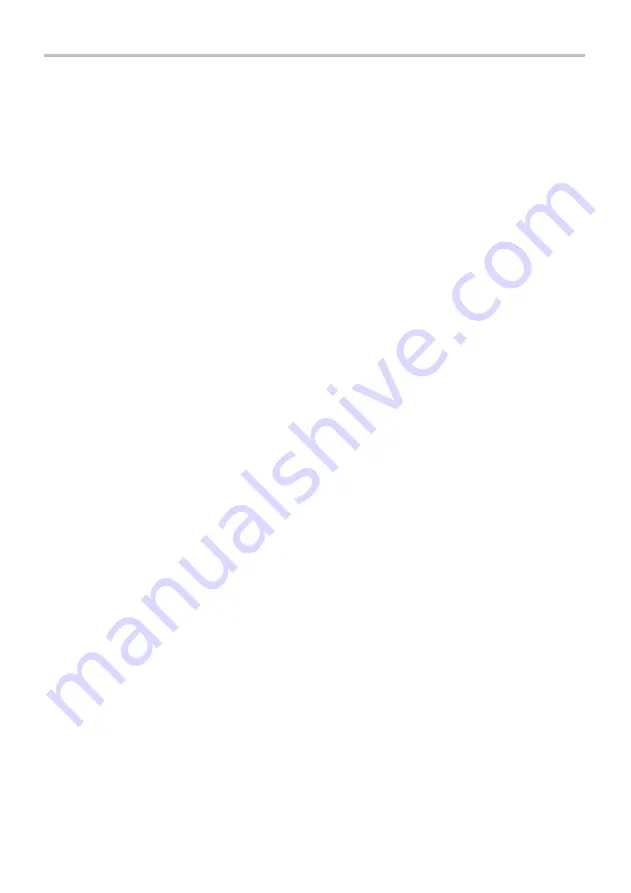
page 9
APPENDIX 2
GUIDE TO SAFE USE
Receiving & Unpacking
Upon receiving the Mecmesin test frame ensure adequate equipment and/or assistance is
available to lift safely the test frame and crosshead unit from the packaging. Trying to lift heavy
items without adequate assistance or the correct equipment may lead to accidental personal
injury.
We strongly recommend that all the packaging and fixings are retained for any future transit
requirements.
Once safely removed from the packaging, place the test base unit on a stable and level work
surface. Inspect this and the crosshead unit for any signs of obvious transit damage.
IF ANY DAMAGE IS DISCOVERED DO NOT GO ANY FURTHER WITH INSTALLATION,
AND DO NOT CONNECT TO MAINS SUPPLY UNDER ANY CIRCUMSTANCES
.
Immediately contact your local supplier who will decide the most appropriate action to rectify
the situation as quickly as possible.
Installing the Machine
After placing the machine base unit on a stable and level work surface, a crosshead may
need to be installed. It will be necessary to refer to the photograph in the ‘Adjusting Height
of Crosshead’ section of this manual.
• Slide the AFTI swivel mounting bracket (G) onto one of the pillars, and
• tighten the knurled adjuster to secure
• Slacken off the side adjuster knobs (B)
• ensure that the loading dish (A) is facing upwards and,
• the central adjuster knob (C) faces forward (as illustrated),
• align the holes in the crosshead with the pillars of the base unit, and,
• ensuring that the crosshead remains horizontal,
• gently slide the crosshead down onto the pillars.
• Tighten both side adjuster knobs.
• The system is now ready to install any extra components which have been purchased:
Using an appropriate Allen key, attach a ‘smart’ static torque transducer to the
transducer holding plate (D) using the four M6 bolts supplied.
Attach an AFTI to its swivel mounting bracket (G) using the two M5 bolts supplied.
Connect the static torque transducer cable to the AFTI (see illustration on front cover).
Slide the lower platen turntable spacer (F) onto the drive shaft (E), and secure with the
two M8 grub screws provided; attach the lower mounting plate to this using the 2
M4 countersunk screws supplied.
Slide the upper mounting plate onto the square drive of the torque transducer and
secure with the two grub screws located in the mounting plate.
(The illustration on the front cover shows a system with all these extra components fitted)