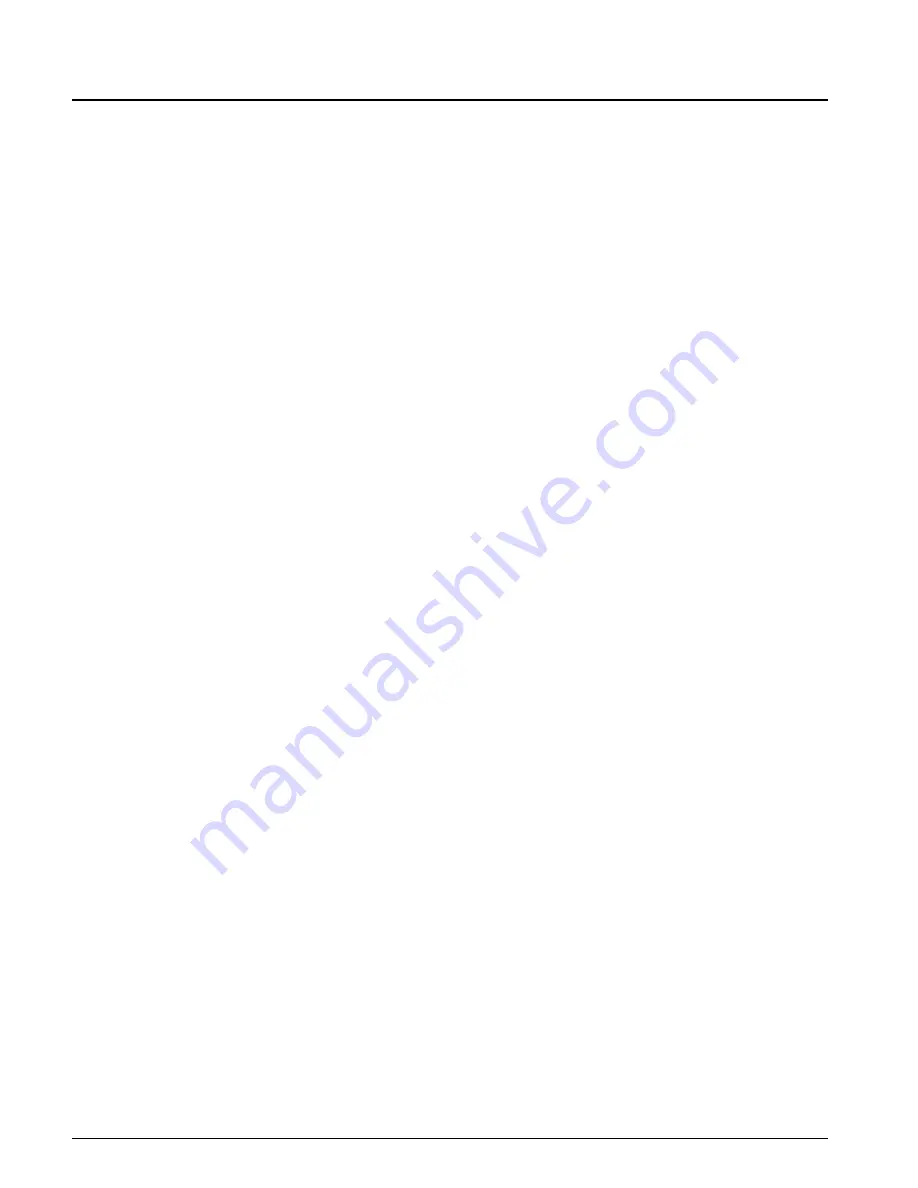
40
IM709
Service and Warranty Procedure
In Warranty Return Material
Procedure
Material may not be returned except by permission of autho-
rized factory service personnel of McQuay International at
Minneapolis, Minnesota.
A "return goods" tag will be sent to be included with the
returned material. Enter the information as called for on the
tag in order to expedite handling at our factories and prompt
issuance of credits. All parts shall be returned to the factory
designated on the return goods tag, transportation charges
prepaid.
The return of the part does not constitute an order for
replacement. A purchase order for the replacement part must
be entered through your nearest McQuay representative. The
order should include part number and description, and the
model and serial numbers of the unit involved.
Following inspection of the returned part by our personnel
and if it is determined that the failure is due to faulty material
or workmanship, credit will be issued on customer's pur-
chase order.
Replacement Parts
When writing to McQuay for service or replacement parts,
refer to the model number, serial number, and G.O. number
of the unit as stamped on the serial plate attached to the unit.
For questions regarding wiring diagrams, it will be necessary
to provide the number on the specific diagram. If replace-
ment parts are required, mention the date of installation of
the unit and the date of failure, along with an explanation of
the malfunction and a description of the replacement parts
required.
Product Warranty
McQuay International, hereinafter referred to as the "Com-
pany," warrants that it will provide, at the Company's option,
either free replacement parts or free repair of component
parts in the event any product manufactured by the Company
and used in the United States proves defective in material or
workmanship within twelve (12) months from initial start-up
or eighteen (18) months from the date shipped by the Com-
pany, whichever comes first. For additional consideration,
the Company warrants that for four (4) years following the
initial warranty period it will provide, at the Company's
option, free replacement parts for the motor-compressor, free
replacement for any integral component of the motor-com-
pressor which is defective in material or workmanship.
(Extended warranties for motor-compressors are not applica-
ble unless separately purchased.)
To obtain assistance under the parts warranty or extended
motor-compressor warranty, simply contact the selling
agency. To obtain information or to gain factory help, con-
tact McQuay International, Warranty Claims Department,
P.O. Box 1551, Minneapolis, MN 55440; telephone (763)
553-5330.
THIS WARRANTY CONSTITUTES THE BUYER'S
SOLE REMEDY. IT IS GIVEN IN LIEU OF ALL
OTHER WARRANTIES. THERE IS NO IMPLIED
WARRANTY OF MERCHANTABILITY OR FITNESS
FOR A PARTICULAR PURPOSE. IN NO EVENT AND
UNDER NO CIRCUMSTANCES SHALL THE COM-
PANY BE LIABLE FOR INCIDENTAL OR CONSE-
QUENTIAL DAMAGES, WHETHER THE THEORY
BE BREACH OF THIS OR ANY OTHER WARRANTY,
NEGLIGENCE OR STRICT LIABILITY.
This parts warranty and the optional extended warranties
extend only to the original user. Abuse, misuse, or alteration
of the product in any manner voids the Company's warranty
obligation. Neither the parts or extended warranty obligates
the Company to pay any labor or service costs for removing
or replacing parts, or any shipping charges. Refrigerant flu-
ids, oils, and expendable items such as filters are not covered
by this warranty.
The extended warranties apply only to integral components
of the motor-compressor or heat exchanger, not to refrigerant
controls, electrical controls, or mechanical controls, or to
failures caused by failure of those controls.
Attached to this warranty is a requirement for equipment
containing motor-compressors and/or furnaces to report
start-up information. The registration form accompanying
the product must be returned to McQuay International within
ten (10) days of original equipment start-up. If that is not
done, the date of shipment shall be presumed to be the date
of start-up and the warranty shall expire twelve (12) months
from that date.
No person (including any agent, salesman, dealer, or distrib-
utor) has authority to extend the Company's obligation
beyond the terms of this express warranty, or to state that the
performance of the product is other than that published by
the Company.
Summary of Contents for SWT C Series
Page 23: ...IM709 23 Typical Wiring Schematics Figure 19 Power Schematic...
Page 24: ...24 IM709 Figure 20 Input Schematic Discharge Air Control DAC...
Page 25: ...IM709 25 Figure 21 Input Schematic Zone or Space Comfort Control SCC...
Page 26: ...26 IM709 Figure 22 Output Schematic Actuator Control...
Page 27: ...IM709 27 Figure 23 Output Schematic Auxiliary Fan Start Stop Control...
Page 28: ...28 IM709 Figure 24 Output Schematic Actuator Control...
Page 29: ...IM709 29 Figure 25 Output Schematic Compressor Control 4 Compressors 4 5 or 6 Stage...
Page 44: ...13600 Industrial Park Boulevard Minneapolis MN 55441 USA 763 553 5330...