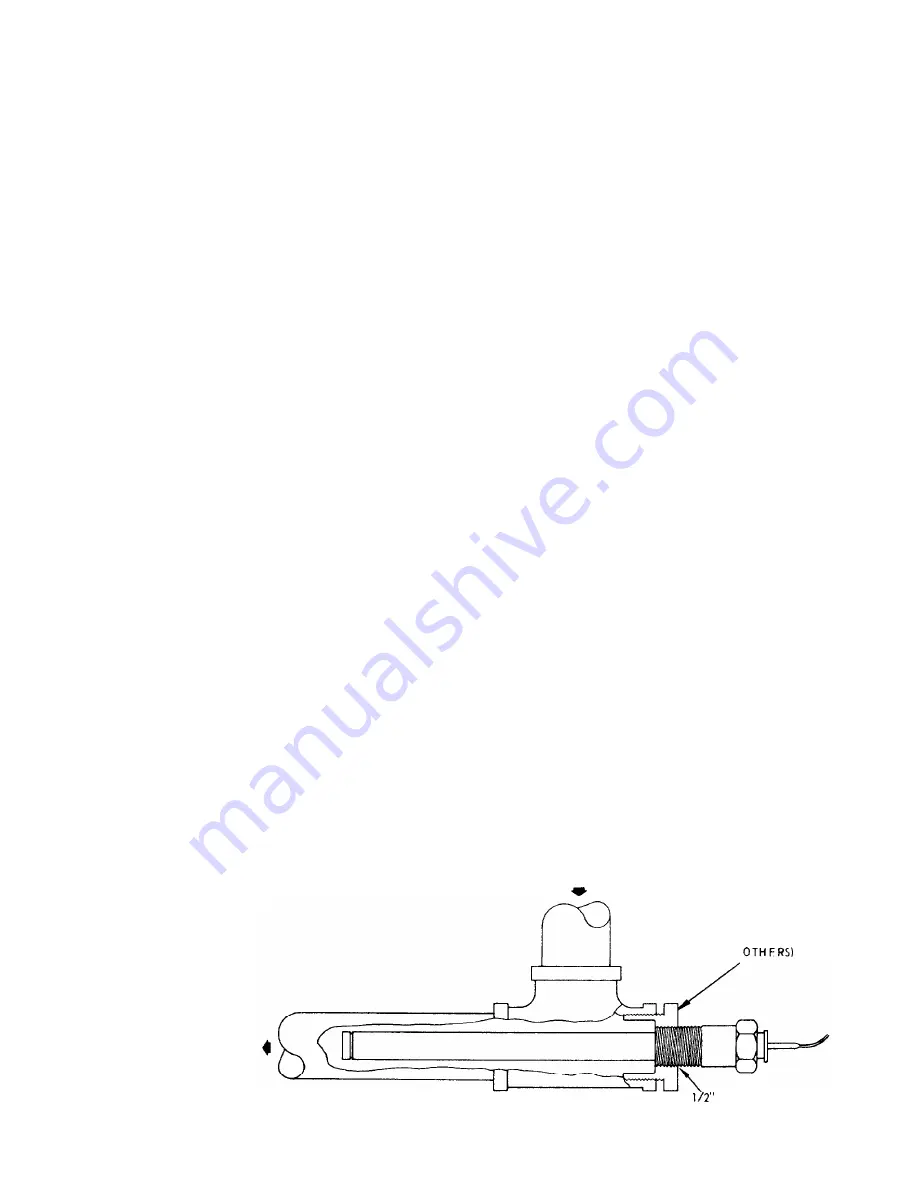
WATER PIPING
GENERAL
A.
B.
C.
D.
E.
Piping practices vary considerably. In most cases C.
codes, local ordinances and established practices
govern the selection and installation of piping.
Local building and safety codes and ordinances
should be studied and complied with.
Shut off valves should be provided at the unit so
that normal servicing can be accomplished without
draining the system.
D.
It is recommended that temperature and pressure
indicators be installed at the inlet and outlet of
the shells to aid in the normal checking and ser-
vicing of the unit. Also, the installation of wire
mesh strainers at the pump suction will protect the
pump and shells from foreign matter.
A preliminary leak check of the water piping should
be made before filling the system.
Vibration eliminators are recommended in all lines
connected to the SEASONPAK air cooled water
chiller, to reduce vibration transmission.
CHILLED WATER PIPING
A.
B.
Each cooler is provided with the connections as
indicated in Figures 4 and 5, Page 7. Also, a 1 / 4 ”
NPT vent and 3/4” NPT drain are provided.
Design the piping so that it has a minimum number
of changes in elevation. Include manual or auto-
matic air vent valves at the high points of the
chilled water piping, so that air can be vented
from the water circuit. System pressures can be
maintained by using an expansion tank or a combi-
FIGURE 9
TO COOLER
nation pressure relief and reducing valve.
All chilled water piping should be insulated to
prevent the nuisance of water dripping from the
lines. If insulation is not of the self-contained
vapor barrier type, it should be covered with a
moisture seal. Do not insulate piping until it has
been tested for leaks and until all vent and drain
connections have been extended beyond the pro-
posed insulation thickness to make them accessible.
The chilled water thermostat is mounted inside the
control center, and the control bulb, capillary tubing,
and control bulb immersion well are attached to
the unit with spring clips. The control bulb well
must be field inserted in the first tee installed in
the return water line as shown in Figure 9. The
bulb well is supplied with a l/2” NPT male thread.
Carefully unsnap the well from the holding clips,
remove the retaining bushing and slowly remove
the bulb from the well. Install into piping as indi-
cated in Figure 9. When installing the bulb, care-
fully remove it f rom the well so as to not w i p e off
the heat conducting compound supplied in the> well.
After installing the well, carefully insert t h e bulb
and
seal in with the excess compound. Insert t h e
retaining gasket and sealing hushing and clip or
tape the cap tube to the water line. Care should be
taken not to break or kink the charged capillary
tubing. Sufficient cap tube length is provided for
bulb insertion up to 10 feet from the unit; h o w e v e r ,
it is recommended that the bulb well be placed as
close to the cooler inlet as possible. Insulate over
thermostat well.
CAUTION: The thermostat hulh should not be e x -
posed to water temperatures above 125F since this
will damage the control.
THERMOSTAT WELL INSTALLATIONS
RETURN WATER
BUSHING
(BY
N.P.T.
Page 24