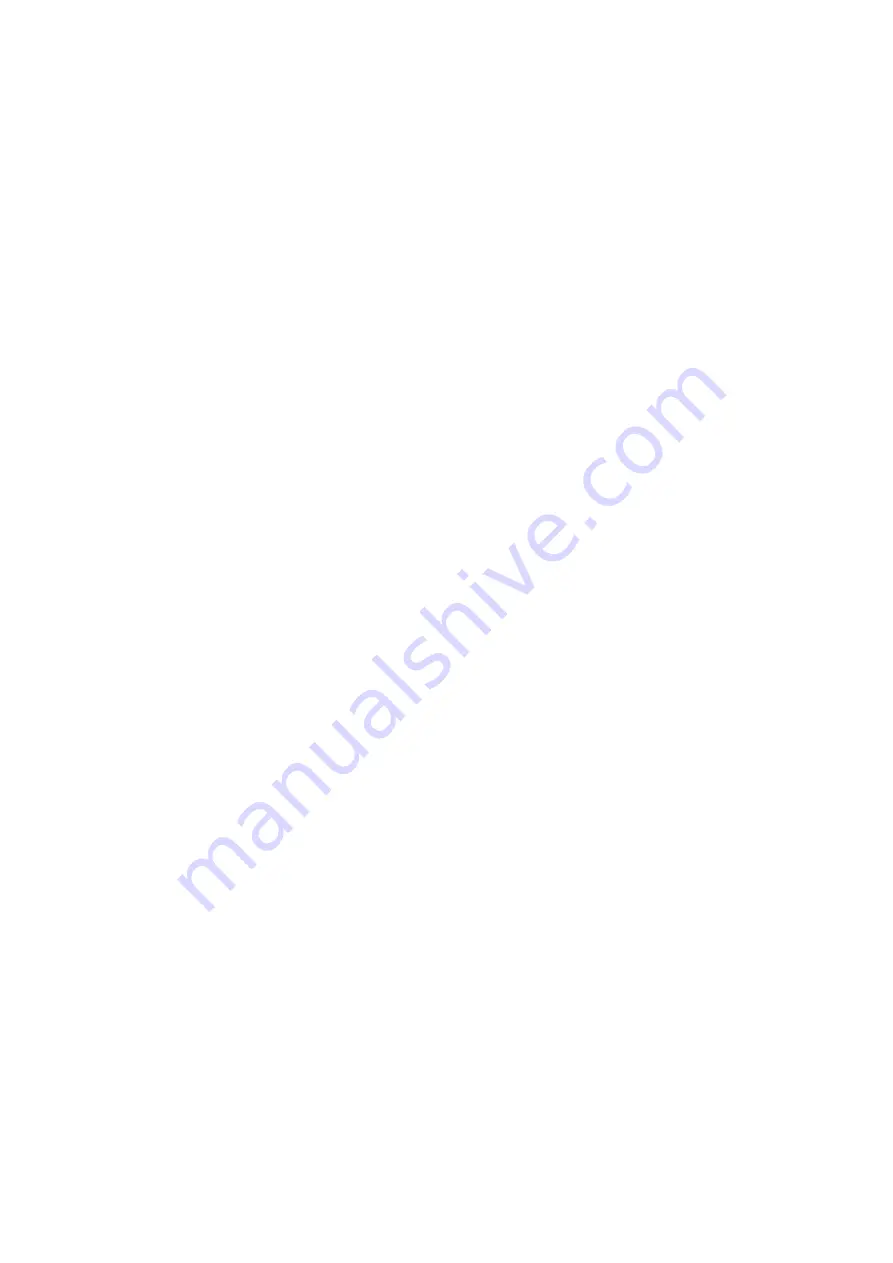
803 B – 04/07 D – pag. 2/24
New water cooled screw chillers McQuay PFS “B”
McQuay International introduces their newest water cooled screw chillers equipped with new single screw
compressors.
McQuay water cooled PFS chillers equipped with 1 or 2 McQuay screw compressors are a new range of the unit
using the StarGate
TM
single screw compressors. They are manufactured by McQuay to satisfy the requirements of
the consultants and the end user. McQuay PFS units are designed to minimise energy costs while maximising the
refrigeration capacities. Once again McQuay has developed a line of chillers unsurpassed in performance and
quality that will meet the most stringent requirements of comfort cooling, ice storage and process applications.
McQuay’s chiller design experience, combined with outstanding features makes the PFS chiller unmatched in the
industry.
Customer benefits
Design for every kind of requirement
Compared with competitors, PFS water cooled chiller offers surprising performance. PFS dual compressor unit
(with a single refrigerant circuit) takes full advantage of the total heat transfer surface over the use of two separate
refrigerant circuits when only one compressor is required to satisfy the thermal load.
McQuay has answered the challenge to create a reliable, energy efficient, environmentally safe with the
introduction of the new PFS screw compressor water-cooled chiller.
Lower noise – higher flexibility
The McQuay original compressor design with a single screw and twin rotors allows a constant gas flow. This
compression process completely eliminates gas pulsations. The oil injection also results in significant mechanical
noise reduction.
The twin gas compressor discharge chambers are designed to act as attenuators, based on the harmonic wave
principle with destructive interference, thus always resulting equal to zero. The extremely low noise compressor
performance affords the use of PFS chiller for all applications.
The reduced number of vibrations produced from the PFS chillers offers a surprisingly quiet operation eliminating
the noise transmission through the structure and the chilled water piping system.
Infinitely variable capacity control
Cooling capacity control is infinitely variable by means of a capacity slide controlled by microprocessor system.
Each unit has infinitely variable capacity control down to 12.5% (two compressors units), to 25% (one compressor
units). This modulation allows the compressor capacity to exactly match the building cooling load. The result is a
decrease in chiller energy costs, particularly at the part-load conditions at which the chiller operates most of the
time. In order to optimize control sequence, each compressor load (and unload) from 95 to 100 % of its capacity
by one step.
Unmatched serviceability
Field serviceability has not been sacrificed. Inspection covers allows visual inspection of the main screw and
gaterotors. Suction valves allow easy isolation and field servicing of this unit.
Outstanding reliability features
Full factory testing of all the units ensures a trouble free start-up. Extensive test makes certain that each safety
and operating control is properly adjusted, and operates correctly.
803 B – 04/11 D – pag. 2/24